Les moteurs électriques et à combustion sont le pouls des opérations industrielles. Qu’il s’agisse de compresseurs, de convoyeurs, de pompes ou de ventilateurs, ils alimentent les processus qui font tourner les usines.
Cependant, les moteurs représentent également une part importante de la consommation mondiale d’énergie – environ 65 % de la consommation d’électricité dans l’industrie – ce qui en fait à la fois un atout vital et un centre de coûts important. Lorsque les moteurs deviennent inefficaces, même légèrement, les conséquences se répercutent sur les factures d’énergie, l’empreinte carbone et les budgets de maintenance.
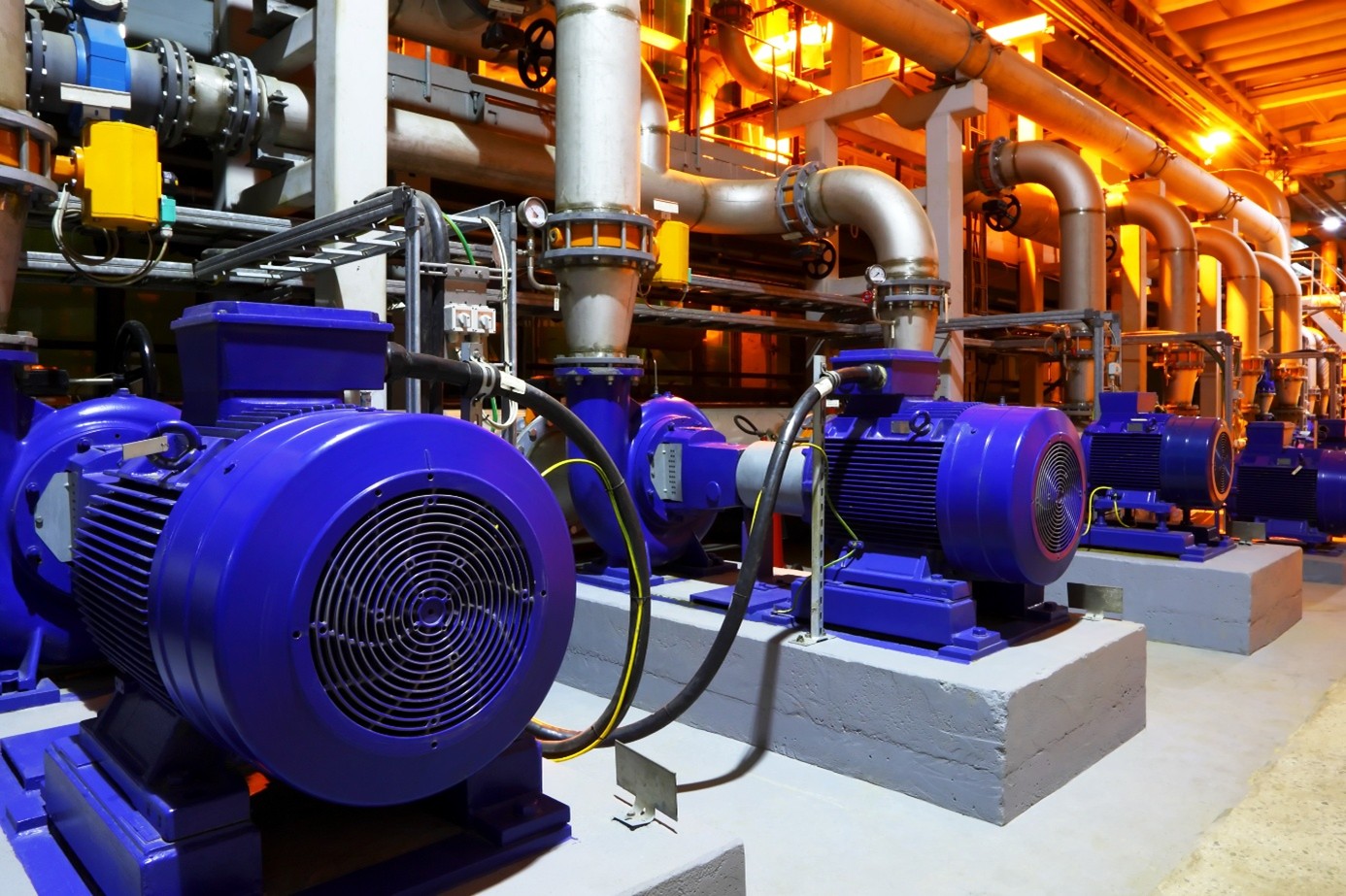
Le coût énergétique des moteurs dans l’industrie
L’inefficacité des moteurs passe souvent inaperçue. Les défauts d’alignement, la dégradation des roulements, les pannes de lubrification et le relâchement mécanique réduisent progressivement les performances, en augmentant les frottements et la chaleur. Ces problèmes subtils peuvent ne coûter que quelques points de pourcentage en termes de performances, mais au fil du temps, cela se traduit par des milliers d’euros en énergie gaspillée et en usure prématurée. Par exemple, un moteur électrique de 100 ch fonctionnant 24 heures sur 24 et 7 jours sur 7 peut consommer plus de 110 000 euros d’électricité par an. Améliorer l’efficacité de ce moteur de seulement 5 % peut permettre de réaliser des économies de plus de 5 000 à 15 000 euros par an. Si l’on multiplie ce chiffre sur un site comptant des dizaines ou des centaines de moteurs, il devient impossible de l’ignorer.
Le facteur négligé de l’efficacité
Les stratégies de maintenance traditionnelles, telles que la maintenance préventive réactive ou programmée, ne permettent pas de relever ces défis. Attendre qu’un moteur tombe en panne avant d’intervenir est coûteux, non seulement en frais de réparation, mais aussi en temps d’arrêt non planifié. La maintenance programmée, bien que meilleure, entraîne souvent des interventions inutiles ou des problèmes non détectés qui surviennent entre les intervalles. Ce qu’il faut, c’est une approche plus intelligente : une maintenance prédictive basée sur la surveillance de l’état, notamment à l’aide de technologies avancées telles que l’analyse des ultrasons et des vibrations.
Les ultrasons se distinguent par leur capacité à détecter les signaux à haute fréquence générés par la friction, les impacts et les turbulences, signaux qui précèdent souvent les vibrations et les anomalies thermiques. Ils sont particulièrement efficaces pour identifier les défauts des roulements, les problèmes de lubrification et l’instabilité mécanique, qui ont tous un impact direct sur les performances et l’efficacité énergétique des moteurs. Combinés à la surveillance des vibrations, les ultrasons constituent un outil puissant pour la détection précoce des défauts.
Le rôle clé du Vigilant
Le Vigilant est un système de surveillance en temps réel entièrement intégré, conçu pour l’évaluation continue de l’état des équipements rotatifs tels que les moteurs. Il utilise une combinaison de technologies ultrasonores et vibratoires pour obtenir une image complète de l’état des moteurs. Le système comprend huit canaux dynamiques pour les données acoustiques et vibratoires à haute fréquence, ainsi que quatre canaux statiques pour des capteurs supplémentaires tels que la température, les tachymètres ou les indicateurs de processus. Le logiciel embarqué de Vigilant analyse ces signaux et en dégage les tendances, fournissant des alertes précoces sur les conditions qui pourraient conduire à une inefficacité énergétique ou à une défaillance catastrophique.
En installant Vigilant, les usines peuvent identifier des problèmes tels que l’augmentation de la friction dans les roulements en raison d’une défaillance de la lubrification, des désalignements mineurs d’arbres qui augmentent les vibrations et la consommation d’énergie, ou des conditions de résonance qui peuvent conduire à la fatigue. Ces problèmes sont souvent invisibles à l’œil nu ou même aux outils de surveillance de base, mais ils se manifestent clairement dans les signatures ultrasoniques et vibratoires que Vigilant capture et interprète. Plus important encore, Vigilant fonctionne de manière autonome, en collectant continuellement des données et en s’intégrant aux plateformes SCADA, CMMS et numériques existantes via des protocoles ouverts tels que OPC et HTTP.

Combler le fossé entre fiabilité et durabilité
Au-delà de la fiabilité, l’adoption de ce type d’approche de maintenance intelligente présente de solides arguments en faveur de l’environnement et de la durabilité. Alors que les gouvernements et les industries poursuivent des objectifs de réduction des émissions de carbone, l’optimisation de l’énergie devient une voie essentielle. Une réduction ne serait-ce que de 5 % de la consommation d’énergie des moteurs contribue directement à la réduction de l’empreinte carbone d’une installation et à ses engagements ESG. La maintenance prédictive réduit également les déchets : moins de réparations d’urgence, moins de remplacements de pièces inutiles et des équipements qui durent plus longtemps signifient moins d’utilisation et d’élimination de matériaux. Ces facteurs s’alignent directement sur des initiatives telles que le Green Deal européen et les normes de gestion de l’énergie ISO 50001.
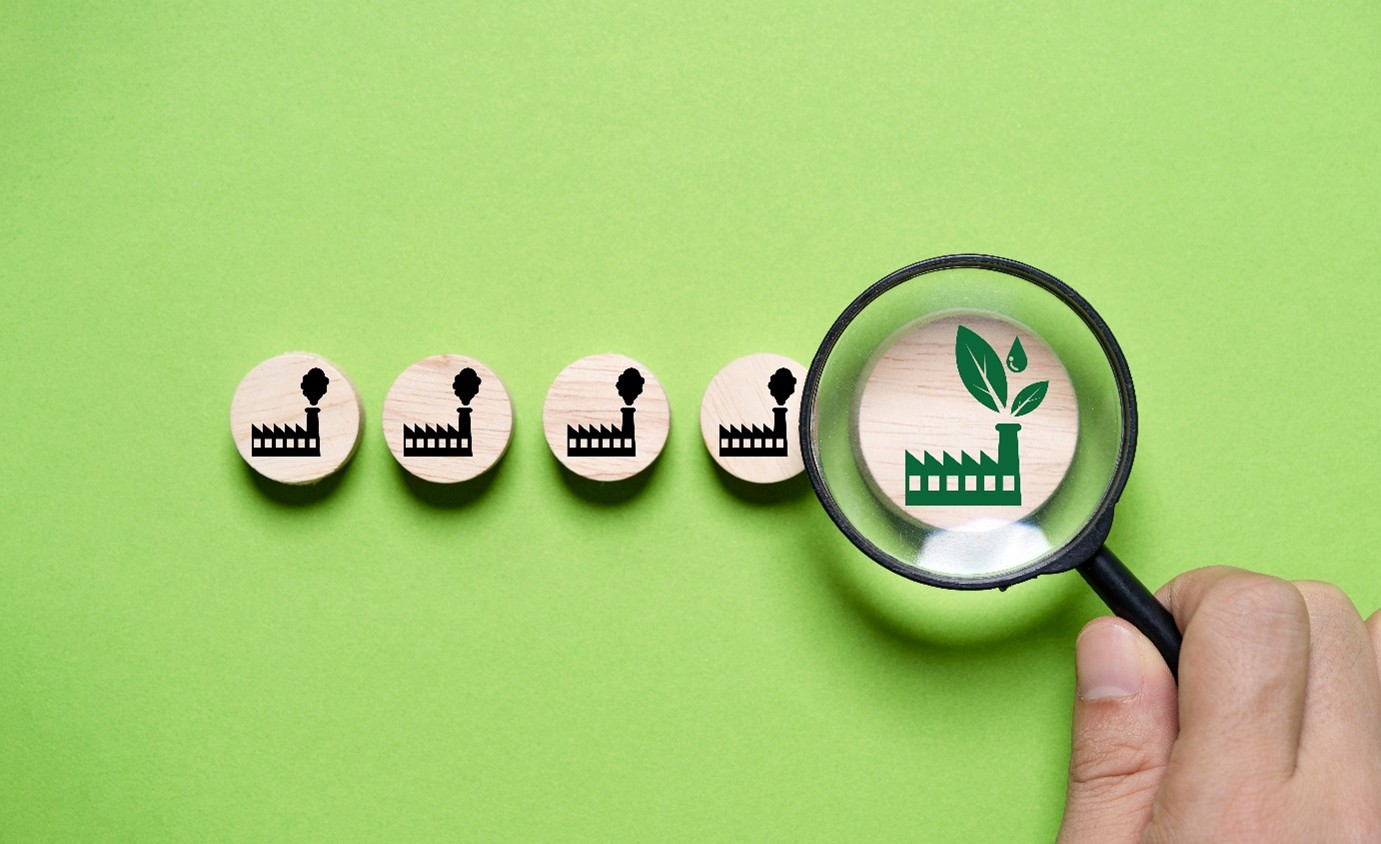
Vigilant permet aux équipes de maintenance de prendre plus rapidement de meilleures décisions. Par exemple, si un moteur commence à montrer des signes d’usure précoce des roulements ou de déséquilibre de la charge, le système alerte l’équipe avant que l’efficacité ne diminue de manière significative ou qu’une panne ne se produise. La maintenance peut alors être programmée de manière proactive, ce qui minimise l’impact sur la production. Au fil du temps, les données provenant de plusieurs actifs peuvent même être utilisées pour optimiser les programmes de lubrification, équilibrer les charges de travail ou détecter des problèmes systémiques dans l’ensemble des installations.
Un investissement intelligent avec un ROI mesurable
Le retour sur investissement est convaincant. Dans un cas documenté, la maintenance prédictive par ultrasons a permis de réduire de 20 % le remplacement des roulements et, dans un autre cas, de réduire de 80 % les pannes de moteur non planifiées. Si l’on ajoute à cela les économies d’énergie, la prolongation de la durée de vie des actifs et l’amélioration de la fiabilité, il est clair que les systèmes comme Vigilant ne sont pas seulement des outils de surveillance, mais aussi des actifs stratégiques.
À une époque où le temps de fonctionnement, les coûts énergétiques et le développement durable sont plus importants que jamais, la maintenance conditionnelle basée sur les ultrasons et les vibrations n’est pas seulement un avantage. C’est un élément essentiel d’une exploitation plus intelligente et plus écologique. Avec Vigilant, SDT offre une solution qui permet aux industries d’atteindre leurs objectifs d’efficacité sans compromettre la performance ou la fiabilité.