Experimente la retroalimentación sobre la implementación de un programa de mantenimiento preventivo basado en ultrasonidos.
Hoy, nos gustaría compartir una experiencia de la retroalimentación de una fábrica de papel que ha implementado un programa de mantenimiento preventivo para monitorear máquinas rotativas utilizando tecnología de ultrasonido. SDT International ayudó a implementar este programa de monitoreo mediante la capacitación y el entrenamiento de los equipos a cargo de la confiabilidad del mantenimiento mecánico. El propósito de este programa es monitorear una flota de aproximadamente 70 máquinas rotativas durante el año posterior a su implementación y extenderla a 100 máquinas durante el segundo año.
Esta fábrica de papel ha confiado durante muchos años en el mantenimiento preventivo, utilizando tecnologías conocidas y probadas para el monitoreo de máquinas rotativas. En 2018, decidieron extender este monitoreo a equipos con velocidades de rotación de hasta 30 RPM, así como a sus engranajes de los reductores de velocidad.
Compraron un detector de ultrasonido tipo SDT270, en versión DU, junto con su software Ultranalysis (UAS), y conjuntamente SDT International y el departamento de confiabilidad de la fábrica de papel desarrollaron un programa de capacitación adecuado para el programa de monitoreo de la maquinaria rotativa. El primer paso consistió en crear la base de datos que incluía estas 70 máquinas, y luego en registrar una medición inicial del estado mecánico de cada rodamiento y cada engranaje. Después de un simple análisis in situ (escucha ultrasónica) y un análisis más detallado (mediciones generales o estáticas y mediciones espectrales o dinámicas) utilizando UAS, se asignaron valores de pre-alarma, alarma y peligro para cada punto de medición.
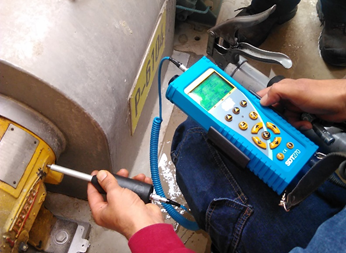
Este trabajo de fondo, que es necesario, permite a los técnicos del departamento de confiabilidad a cargo de las rutas de medición obtener una visión general rápida de la jerarquía de activos y ver inmediatamente las máquinas que tienen un estado de alarma.
Visualización de la base de datos en el software UAS
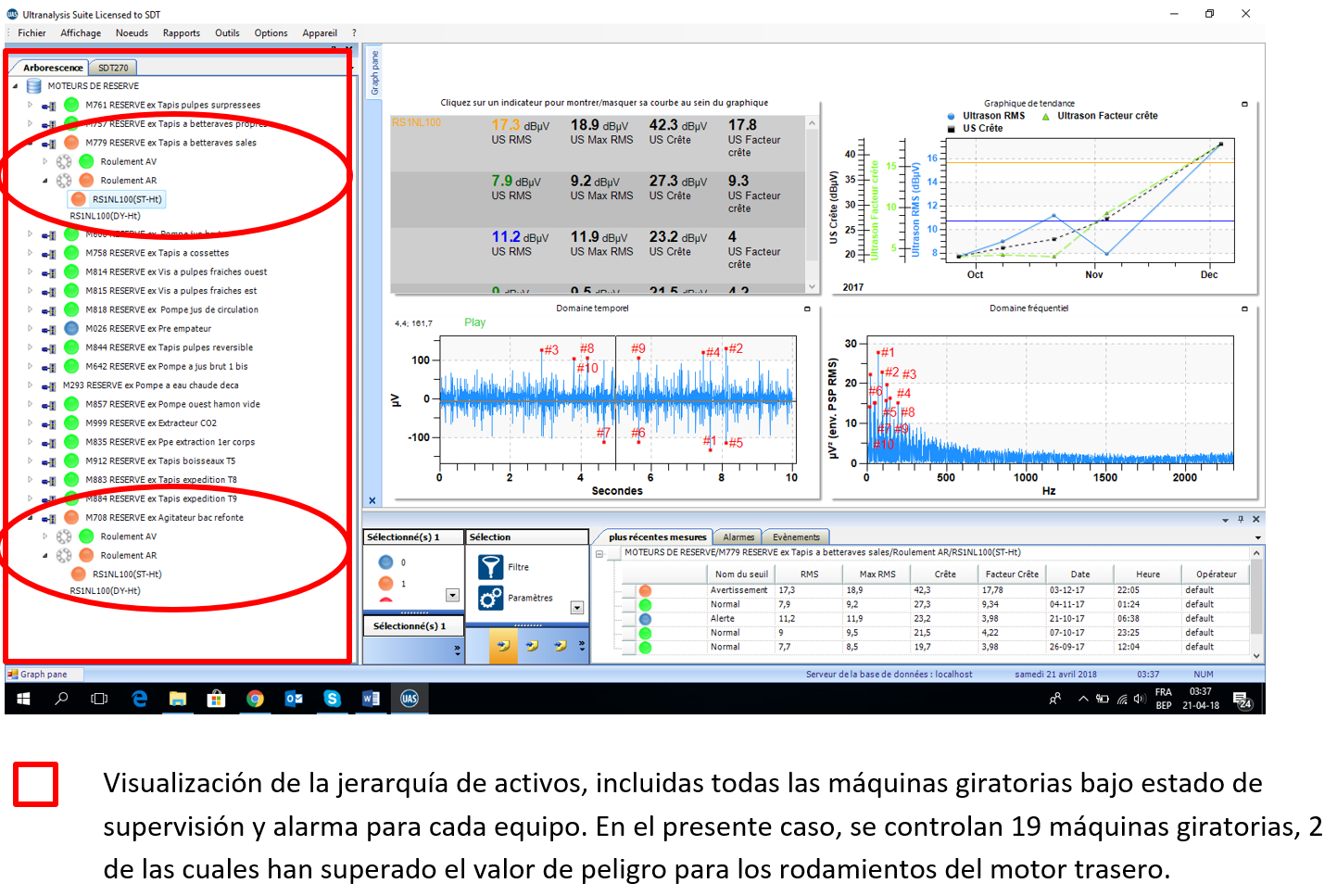
Problema
Este programa de mantenimiento preventivo tiene 3 objetivos:
- Resaltar la eficiencia de las mediciones de ultrasonido en máquinas giratorias.
- Emitir un diagnóstico relevante.
- Ofrecer un mantenimiento preventivo con indicadores fiables.
Experimente los comentarios después de las sesiones de medición en sitio de octubre de 2018 a noviembre de 2019
Seguimiento de un engranaje de reducción paralelo
- Máquina: Decantador – Cojinete de entrada de alta velocidad del engranaje de reducción
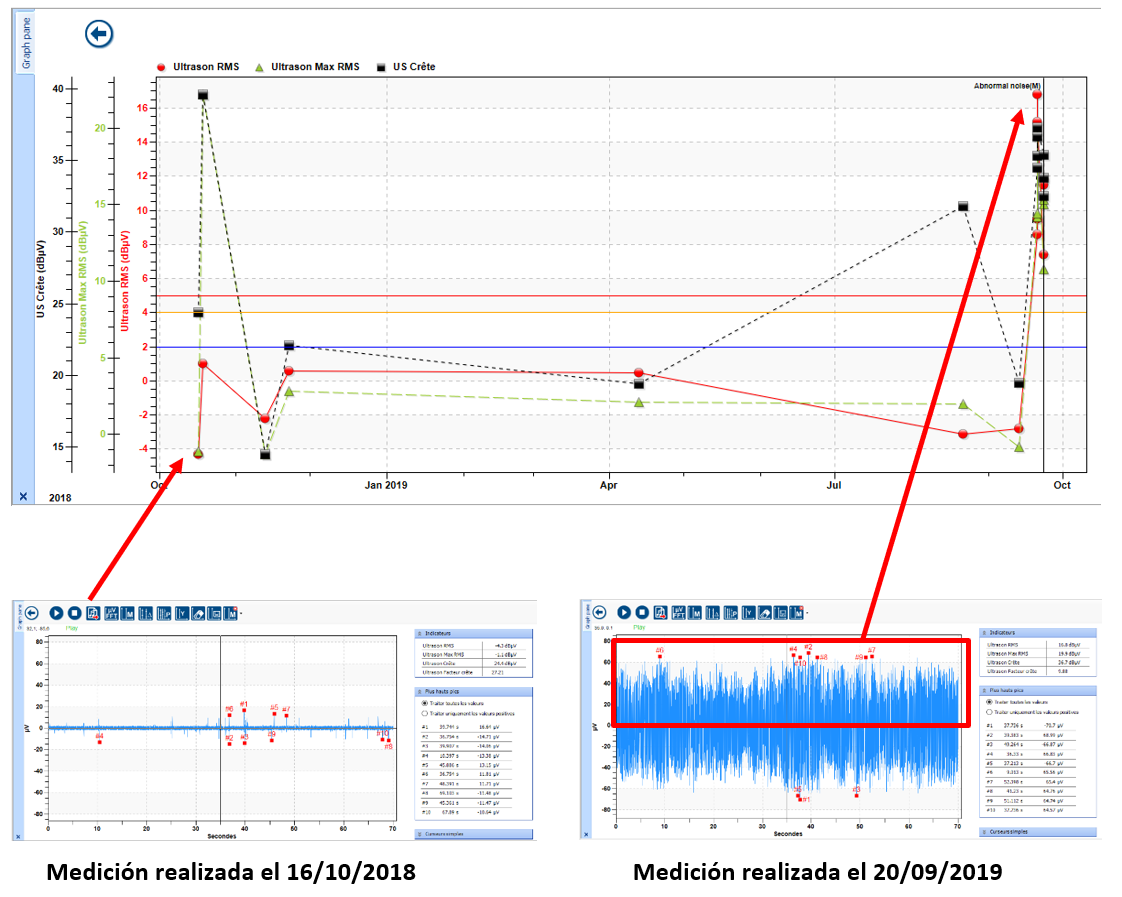
En los espectros de tiempo (misma escala), podemos observar la ocurrencia de choques en comparación con la primera medición realizada en 2018. Las curvas de tendencia muestran la evolución del valor estático RMS: de -4,3 dBμV en 2018 a +16,8 dBμV en 2019.
Basado en criterios de SDT, este aumento corresponde al fallo temprano de una parte mecánica del engranaje de reducción (rodamientos y/o engranajes).
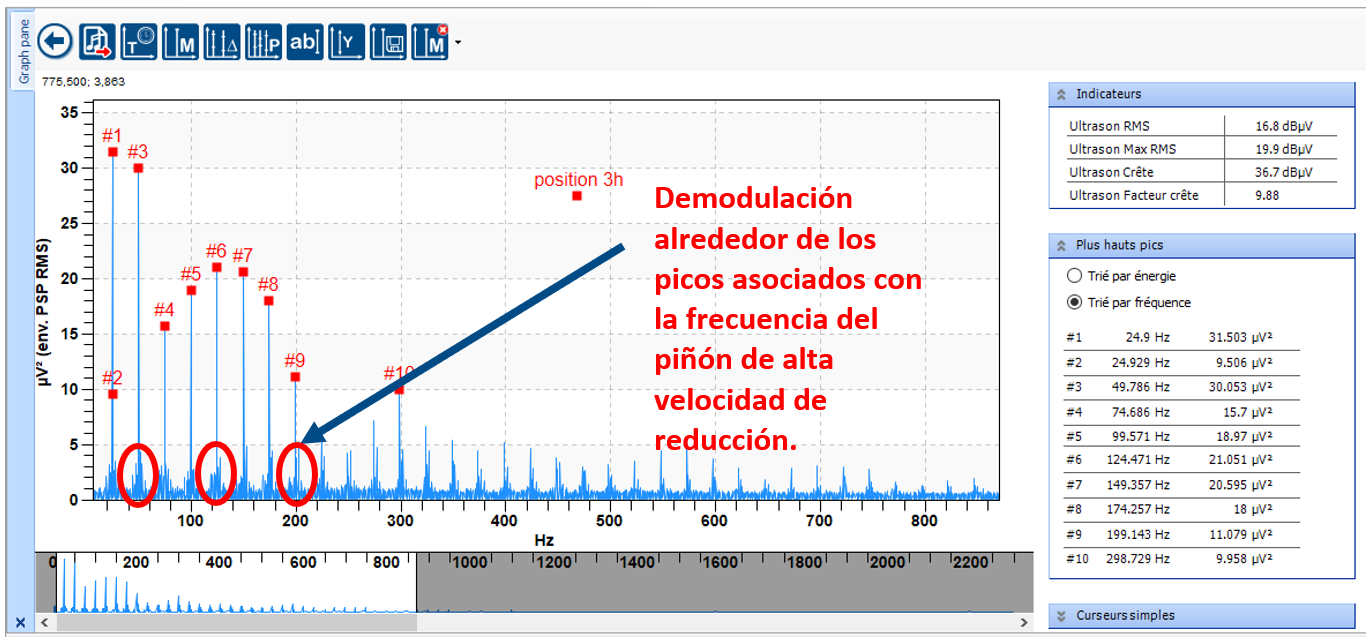
Escuchar el rodamiento y analizar los espectros de frecuencia (ver gráfico a continuación) ha permitido confirmar este diagnóstico al observar la aparición de picos significativos asociados con este daño del engranaje.
Podemos observar choques repetidos asociados a la frecuencia del piñón de accionamiento de entrada de alta velocidad del engranaje reductor (24,93 Hz y sus harmónicos) con demodulación en cada pico. Despeje de dientes rotos y dientes. La sustitución del engranaje reductor durante una parada de producción programada evitó una avería inesperada que podría haber generado gastos significativos debido a las pérdidas de producción.
Desgaste detectado en el diente del tornillo de gusano de un engranaje de reducción, rueda y tornillo:
- Máquina: Agitador del filtro de lodo de cal – Cojinete de entrada de alta velocidad del engranaje de reducción

Podemos observar que entre cada revolución del tornillo del gusano, se produce un fenómeno, que se puede escuchar a través del detector de ultrasonido como un deslizamiento del engranaje (tornillo del gusano / rueda de bronce).
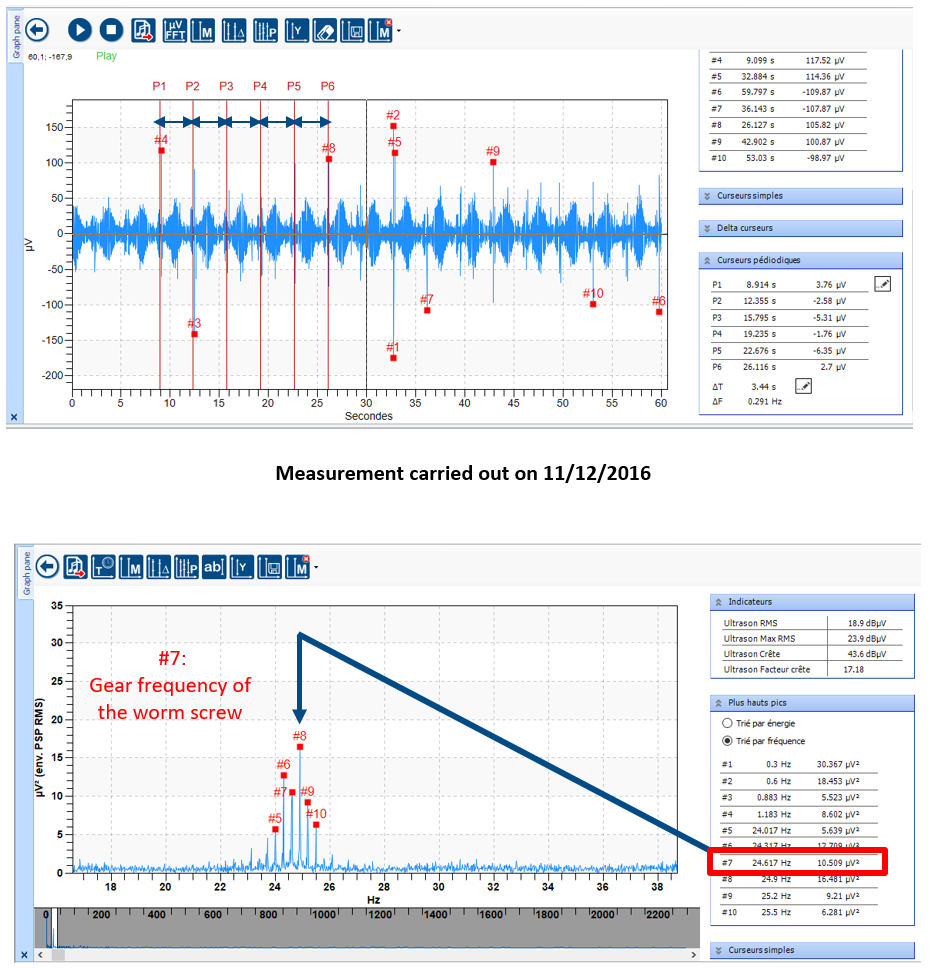
El zoom en el espectro de frecuencias FFT permite resaltar la disimetría de la modulación alrededor de la frecuencia de engrane, que es característica de una frecuencia de paso de engranajes dañados.
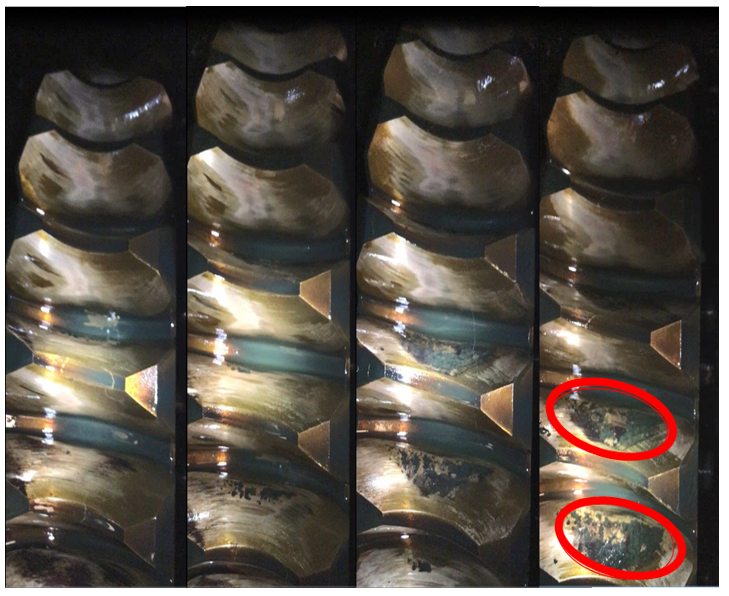
La inspección video endoscópica del tornillo del gusano del engranaje de reducción confirmó la diagnosis del ultrasonido.
El cliente cambio el engranaje de reducción durante un paro de producción.
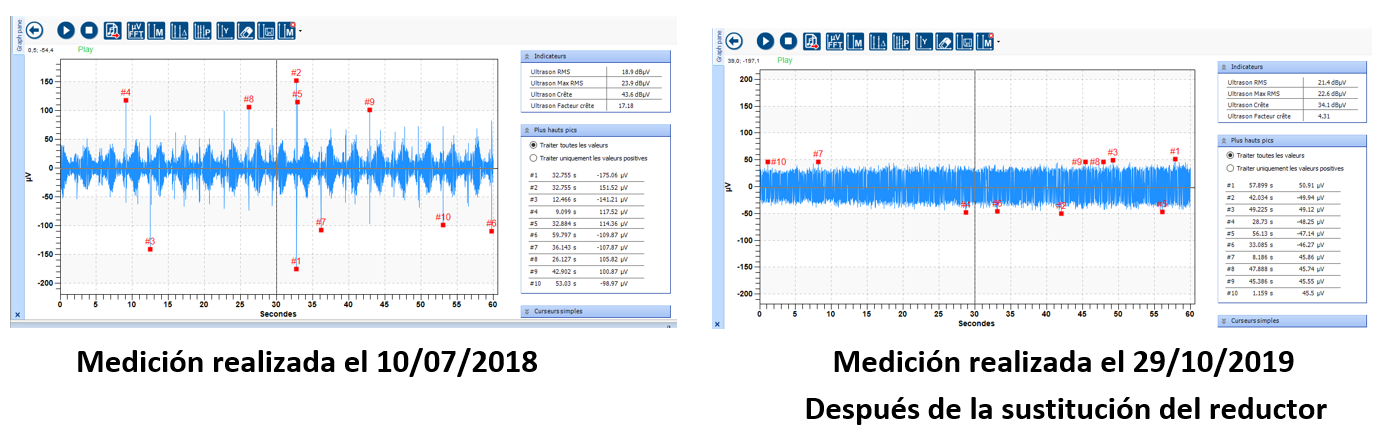
Control de la degradación del rodamiento de un reductor de baja velocidad (transmisión opuesta):
- Máquina: Engranaje de reducción separador de vértices – Engranaje de reducción paralelo de 4 trenes
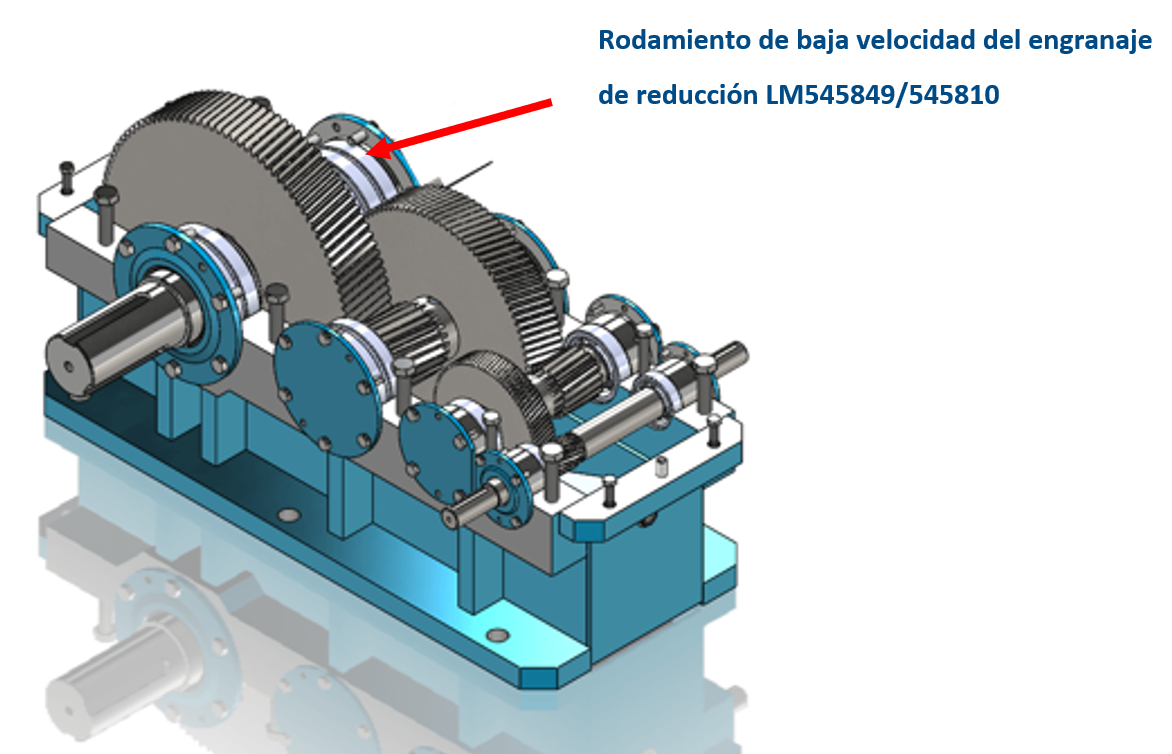
Desde el inicio del monitoreo de este engranaje reductor (agosto de 2018) utilizando tecnología de ultrasonido, se puede observar la ocurrencia de choques en el espectro de tiempo.
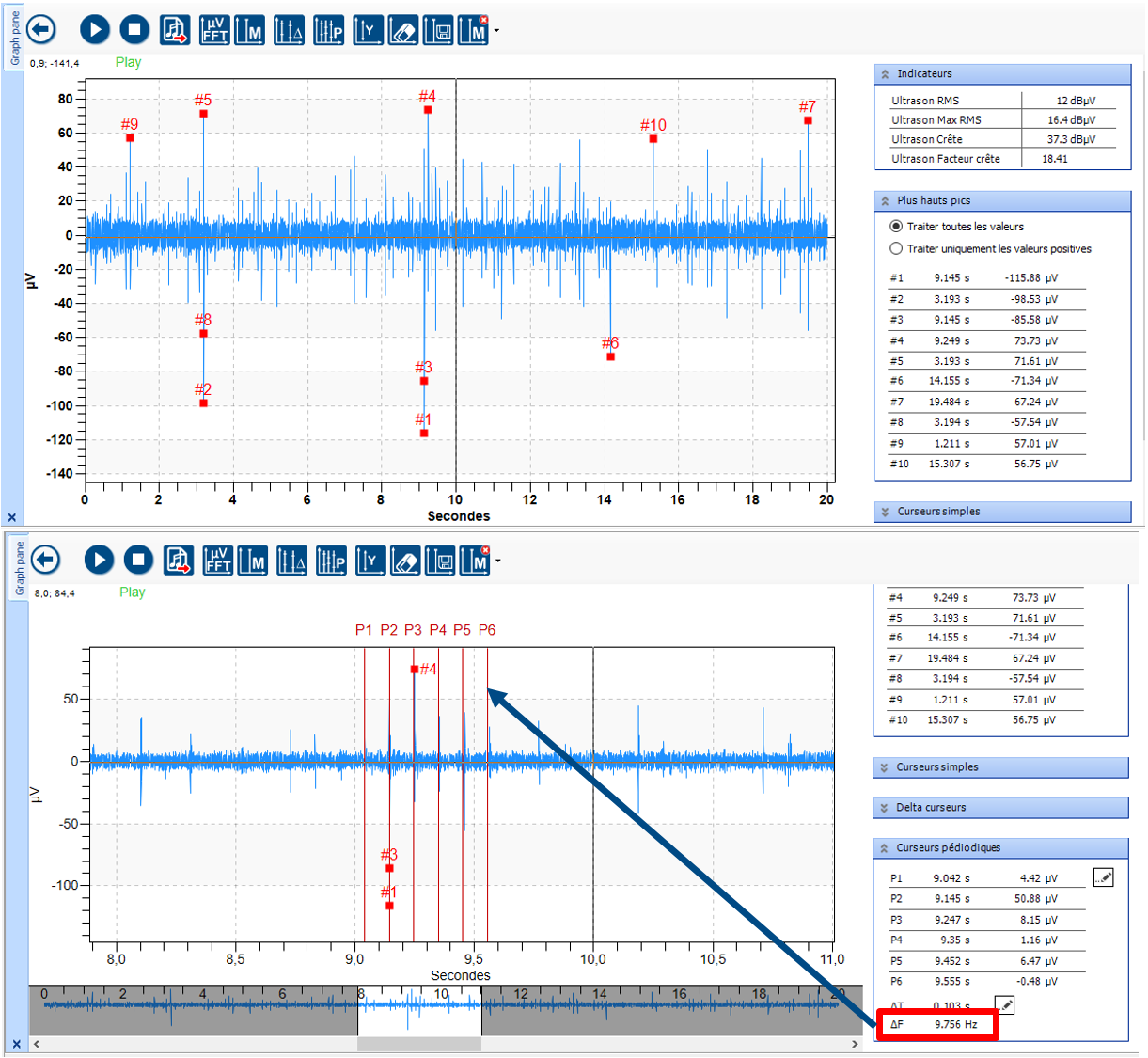
Al hacer zoom en los espectros de tiempo, se pueden observar choques repetidos a 9.756 Hz (ver la tabla de frecuencias características a continuación) relacionados con la frecuencia del aro interno del rodamiento del engranaje de reducción de baja velocidad (lado opuesto de la transmisión). Diagnóstico confirmado en el espectro de frecuencias (ver más abajo).
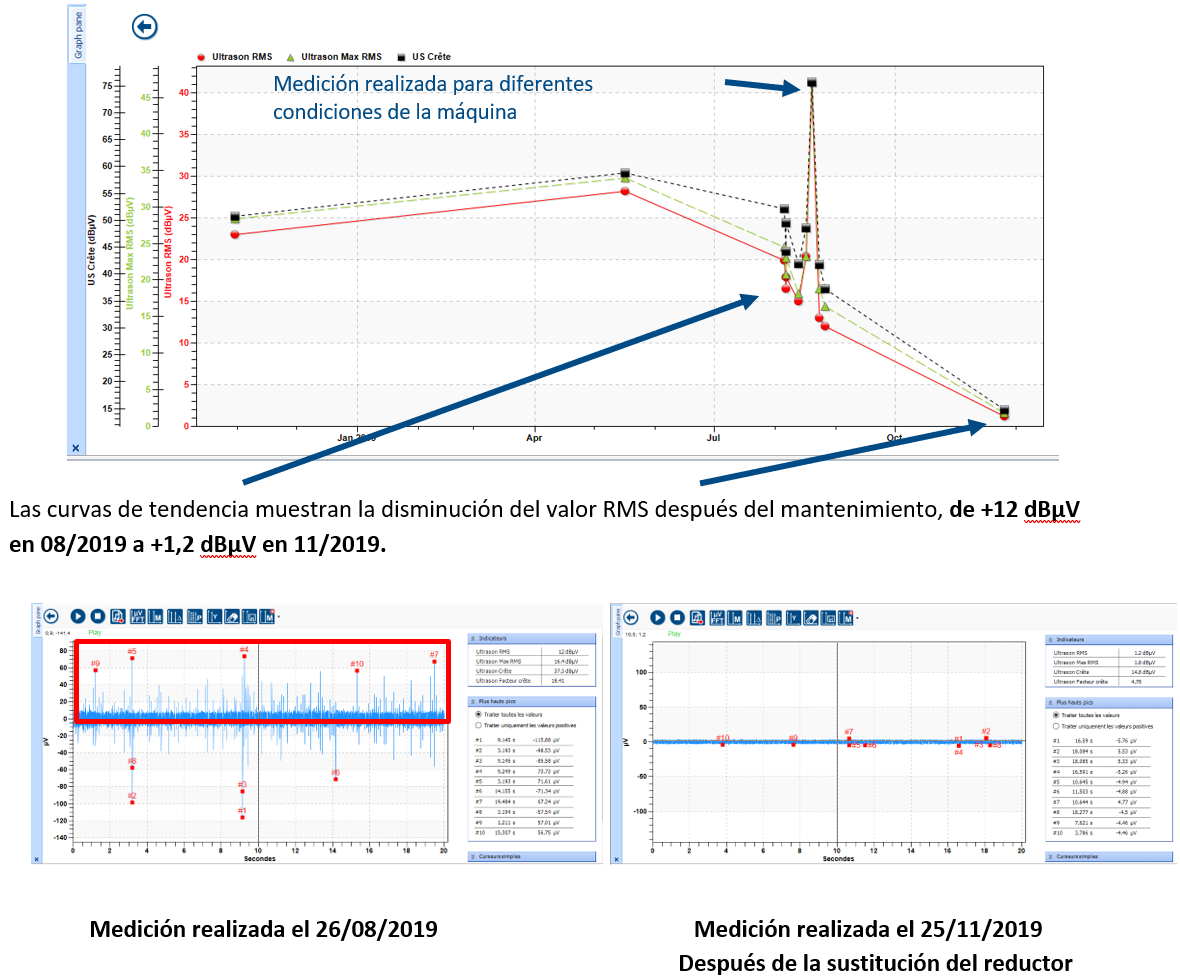
Sustitución del engranaje reductor durante una parada de producción programada, lo que evitó una avería inesperada que podría haber generado gastos significativos debido a las pérdidas de producción.
Control de la degradación del rodamiento de un reductor de baja velocidad (transmisión opuesta):
- Máquina: Filtro de barro de cal – Cojinete de transmisión opuesta 23140 CCK – 14.28 RPM
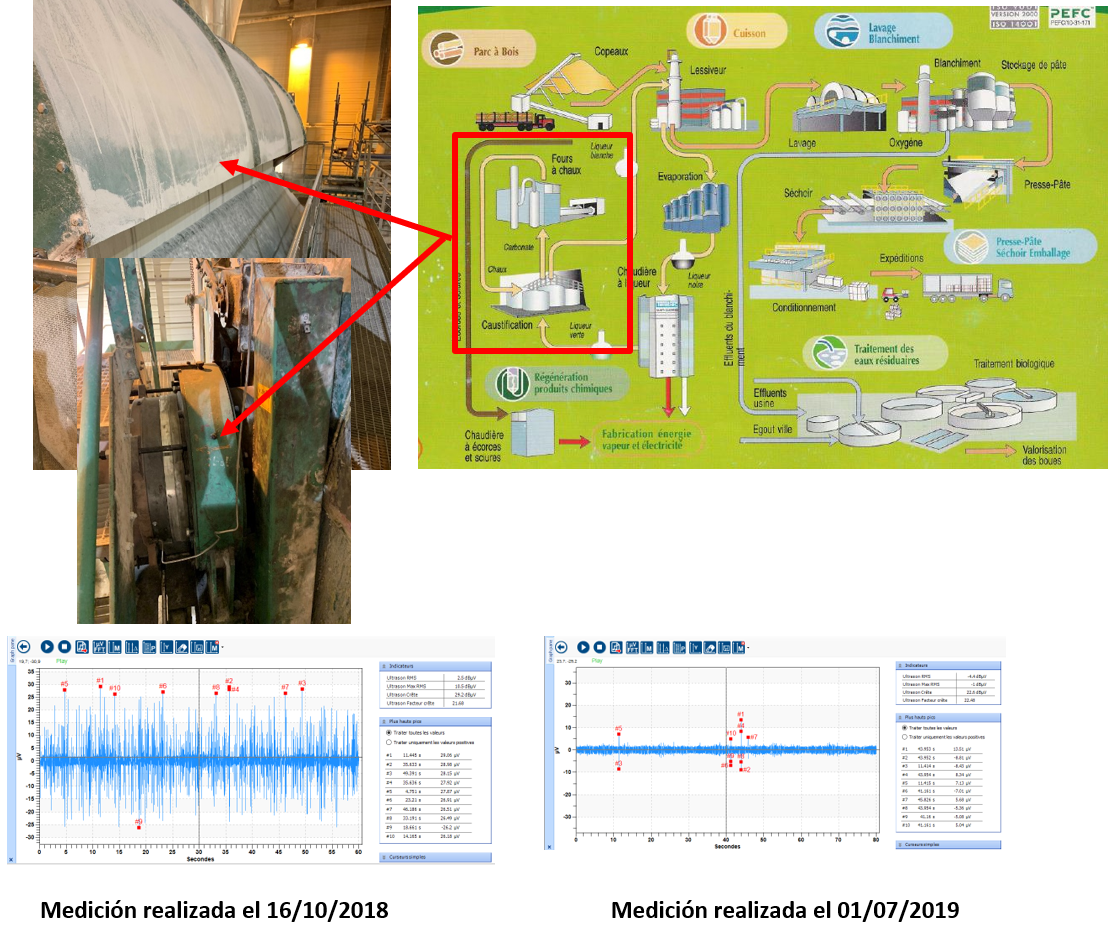
En los espectros de tiempo (mismas escalas), se puede observar la ocurrencia de choques desde el principio de la supervisión de este rodamiento. Después del reemplazo del rodamiento, todos los choques desaparecieron. Los elementos rodantes ya no se mantenían en sus carcasas.
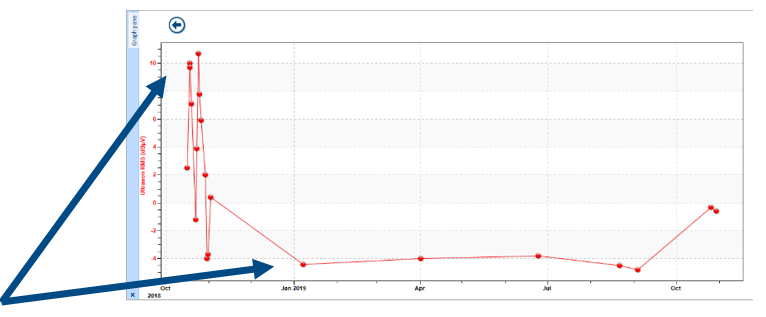
Las curvas de tendencia muestran la disminución del valor RMS después del mantenimiento (de +10,7 dBμV en 10/2018 a -4,4 dBμV en 01/2019).
Conclusión
El reto fue asumido por el equipo de Confiabilidad de esta fábrica de papel. La implementación de un programa de mantenimiento preventivo para 70 máquinas rotativas ha tenido un resultado beneficioso y decisivo. Se extenderá a otras 100 máquinas a lo largo de 2020.
SDT International ofreció una solución simple y herramientas de medición adecuadas, junto con un programa de capacitación certificado por ASNT LEVEL 1. Los usuarios han adquirido un dominio integral de esta tecnología, que era nueva para ellos.
- Utilizando la tecnología de ultrasonido para monitorear máquinas giratorias de baja velocidad, esta fábrica de papel pudo evitar una serie de paradas no programadas (ver ejemplos a continuación) y resaltar la complementariedad de las tecnologías de ultrasonido y vibración.
- Basándose en esta experiencia, el departamento de Confiabilidad ha decidido iniciar campañas de engrase asistidas por ultrasonido. Utilizando equipos adecuados (software y hardware), este programa de lubricación acústica garantizará un engrase perfecto al indicar:
- la grasa adecuada,
- el lugar de engrase adecuado,
- el intervalo de engrase adecuado,
- la cantidad correcta de grasa para añadir,
- los indicadores adecuados para la condición de lubricación.
De este modo, se garantizará la trazabilidad completa del programa de lubricación.
- La versatilidad del detector de ultrasonido SDT270DU también permitió la implementación de:
- Una política de ahorro de energía (detección de fugas de aire comprimido, control de trampas de vapor).
- Control de sopladores de tubo (detección de fugas en válvulas de vapor).
- Mantenimiento preventivo de sistemas eléctricos de alta tensión (corona, seguimiento, arco).
Autor: Patrice DANNEPOND – Area Sales Manager SDT Ultrasound Solutions