Pendant des années, le reclamer d’une usine de production de papier du Nord-Ouest de la France avaient fonctionné de manière fiable, pivotant grâce à trois pignons montés sur des réducteurs. Celui-ci sert à récupérer des copeaux de bois sur un tas afin de les véhiculer par des godets. Cependant, de façon tout à fait inopinée, la structure qui supportait ces équipements connut un affaissement. Heureusement, l’entreprise avait mis en place un programme de suivi préventif mensuel pour surveiller l’état de ces couronnes d’orientation.
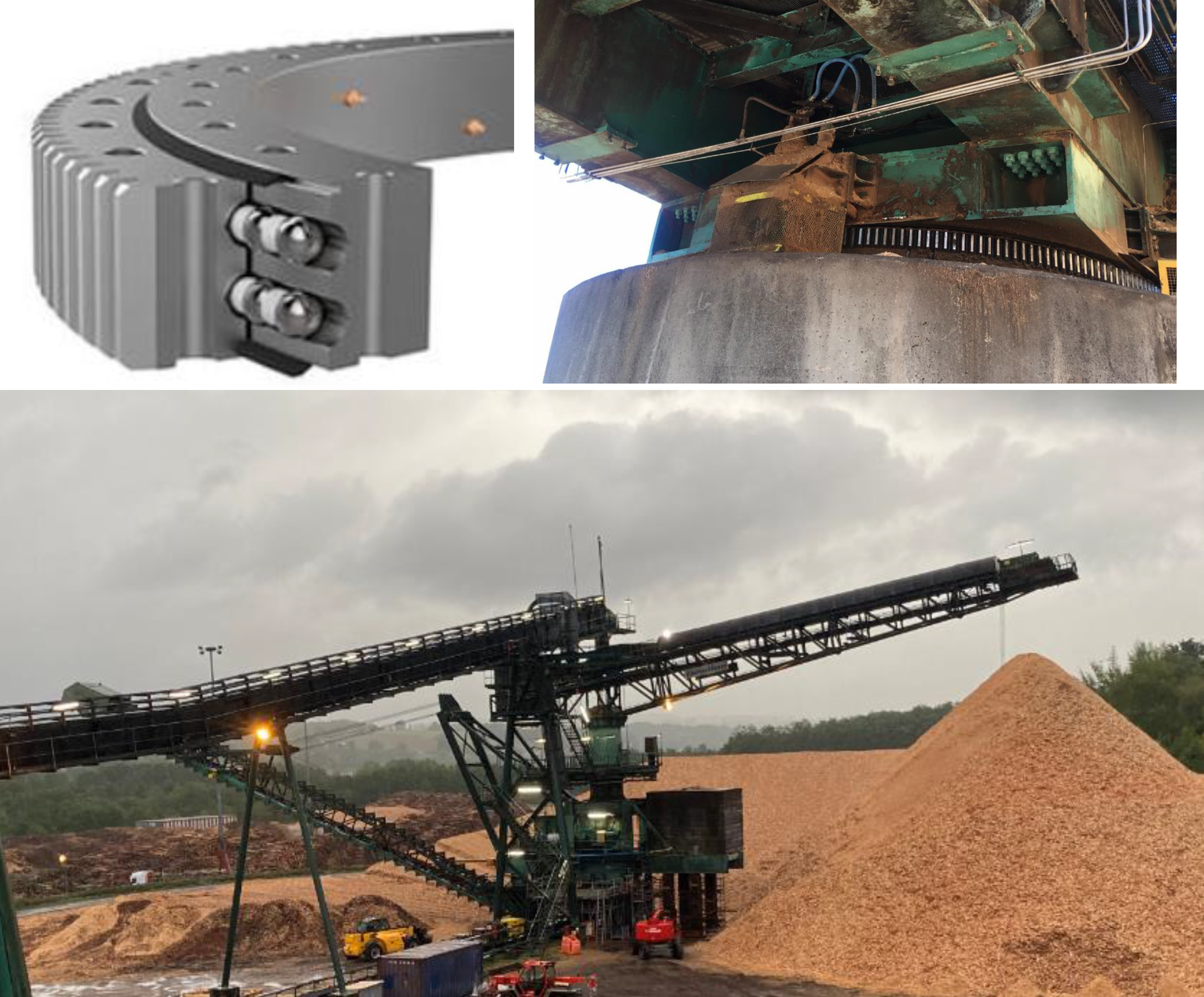
C’est à ce moment que l’entreprise prit une décision clé. Ils ont décidé de s’appuyer sur une technologie de pointe pour évaluer la gravité de la dégradation de la couronne après l’affaissement. Ils ont utilisé un dispositif de mesure ultrasonore (SDT340), la seule technologie qui pouvait fournir une analyse approfondie de la situation. Des mesures de référence préalables à l’incident ont été conservées pour permettre de comparer l’état actuel à l’état initial.
Le processus de mesure était complexe. Pour effectuer une évaluation précise, ils devaient faire tourner l’équipement entre deux des trois pignons pendant un cycle de rotation, ce qui prenait environ deux minutes. De plus, il n’y avait pas de fréquence connue, du moins aucune fournie par le constructeur, pour ces couronnes d’orientation. La vitesse de rotation n’était pas toujours constante, rendant la tâche encore plus compliquée.
Cependant, l’entreprise ne se découragea pas. Ils savaient que seule une représentation temporelle et une écoute attentive pouvaient révéler les signes d’un problème potentiel. En analysant les données recueillies grâce à la technologie de mesure ultrasonore, ils purent identifier des anomalies et des déformations dans la couronne, indiquant une dégradation importante.
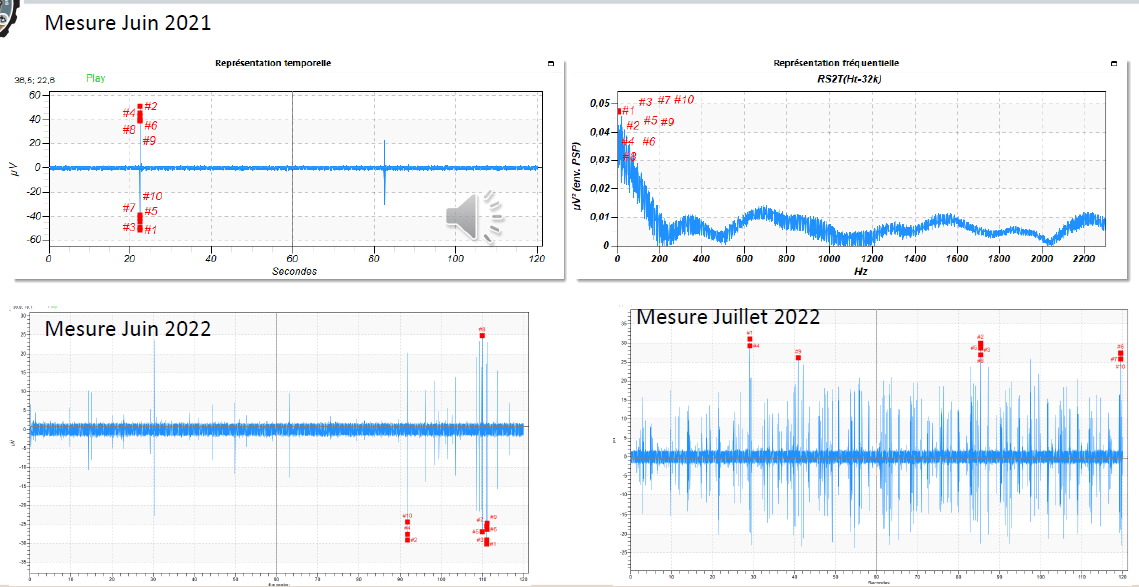
L’image ci-dessus montre une représentation temporelle plutôt évolutive. Des mesures relativement normales en juin 2021 basculent progressivement vers les prémices de chocs inhabituels en juin 2022, pour aboutir à une situation nettement plus grave au mois de juillet suivant.
Après un travail approfondi, l’équipe a pu déterminer qu’il manquait à certains équipements un certain nombre d’éléments roulants essentiels à leur bon fonctionnement. Les éléments de roulement manquants étaient probablement dus à l’usure des « entretoises » entre les billes faisant office de cages.
Grâce à cette découverte précoce, l’entreprise put prendre des mesures correctives pour éviter un dysfonctionnement majeur qui aurait eu des conséquences graves sur la sécurité et l’efficacité de leurs produits. Ils ont entrepris des réparations immédiates et renforcé leurs procédures de maintenance préventive.
La décision d’investir dans la technologie de mesure ultrasonore s’est révélée être un choix judicieux pour cette entreprise. Non seulement elle a permis de prévenir un incident majeur, mais elle a également renforcé leur réputation en tant que leader de l’industrie, démontrant leur engagement envers la qualité et la sécurité de leurs produits. Cette success story illustre comment la technologie ultrasonore de pointe, la prévention et l’innovation peuvent sauver des entreprises de situations potentiellement catastrophiques.
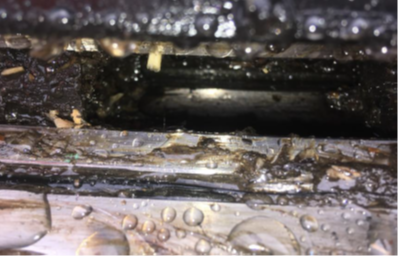