Plus que jamais, le contrôle des coûts de production affecte les activités des services de maintenance.
Si son rôle consiste toujours à connaître l’état de santé des machines, ses coûts associés doivent rester les plus bas possibles. Pour l’opérateur, l’idéal est alors de disposer d’outils polyvalents permettant un diagnostic rapide et fiable : des instruments simples pour résoudre 80% des dérives et des instruments plus avancés pour les 20% restants. Une combinaison des techniques de vibration et d’ultrasons dans le même instrument ? Les problèmes sont détectés par des mesures statiques, tandis que les mesures dynamiques sont utilisées lorsqu’un diagnostic plus approfondi est nécessaire.
Contrôle des coûts
La situation économique actuelle impose aux entreprises un contrôle maximal des coûts de production. Pour ce faire, elles utilisent des installations de plus en plus performantes, donc de plus en plus complexes. Leur objectif est évident : produire plus et mieux. Mais ce n’est pas tout. Les entreprises tendent aussi naturellement à optimiser la maintenance de leur processus, ce qui prend alors une toute autre dimension. Non seulement elles doivent limiter les pertes de production, planifier et optimiser le reconditionnement, tout en limitant le stock de pièces détachées, mais elles doivent aussi accomplir cette mission avec des ressources humaines et financières réduites. Elles ne peuvent plus gaspiller les heures de travail des ouvriers en collectes de données chronophages et en analyses inutiles. En tenant compte de ces aspects, le Vigilant de SDT équipé de capteurs CONMONSense est une solution qui permettra la collecte continue de données sans que le personnel n’ait besoin de collecter des mesures. Toutes les informations sont automatiquement disponibles sur le logiciel Vigilant embarqué afin que l’équipe de Maintenance conditionnelle puisse les analyser en restant assise à son poste de travail.
Vers une maintenance optimisée
Abordons la question sous un autre angle : pourquoi consacrer du temps à la collecte et à l’analyse des mesures ou pourquoi confier ce travail à un spécialiste, si l’on constate finalement que l’équipement est en bon état ? C’est plutôt inefficace, vous ne trouvez pas ? C’est le cas de 80 % des équipements contrôlés. La recherche de l’optimisation passe par l’utilisation d’un outil simple (donc accessible au plus grand nombre), rapide (pour limiter le temps de collecte) et efficace (pour confirmer le bon fonctionnement de 80% des machines). Mais ce n’est pas tout. Sur les 20% de machines suspectes, la cause de la dérive est facile à résoudre pour 80% d’entre elles. Là encore, un outil simple utilisé par un opérateur est la solution la plus adaptée. Enfin, un diagnostic plus poussé est nécessaire pour 20% des 20% restants. En d’autres termes, disons que sur 1000 machines, 200 peuvent avoir des problèmes. Sur ces 200 machines, 160 auront des problèmes faciles à résoudre. Sur les 40 machines suspectes restantes, 8 nécessiteront un diagnostic plus approfondi. Des mesures avancées effectuées par un spécialiste sont alors nécessaires.
La polyvalence est essentielle
Outre la rapidité et la facilité d’utilisation, un outil polyvalent doit être choisi en fonction de la maîtrise des coûts d’investissement. Un instrument de mesure qui peut s’adresser à la fois aux machines tournantes et au contrôle des coûts énergétiques. La complémentarité entre les ultrasons et les vibrations prend ici tout son sens. Les ultrasons sont les champions incontestés des économies d’énergie : air comprimé, vapeur et, dans une certaine mesure, décharges partielles. Pour les machines tournantes, c’est la solution la plus simple pour détecter les phénomènes de frottement (lubrification des roulements), les phénomènes d’impact (défauts des roulements, y compris les roulements lents, et défauts des engrenages) et les phénomènes d’explosion de bulles dans les liquides (cavitation des vannes ou des pompes).
Les mesures vibratoires sont idéales pour détecter les problèmes de désalignement, de balourd, de fondation, d’accouplement et de poulie, ainsi que les phénomènes aérauliques et les défauts affectant les moteurs électriques. Le SDT340 s’appuie sur cette approche, qui combine les techniques de vibration et d’ultrasons : un outil de base pour ceux qui recherchent l’optimisation et l’efficacité de leur programme de maintenance. Basé sur des techniques combinées d’ultrasons et de vibrations, cet instrument de mesure polyvalent permet d’aborder à la fois le contrôle des coûts énergétiques et la surveillance des machines tournantes. Le technicien peut détecter les anomalies, de manière simple et rapide, en utilisant des mesures statiques. Le SDT340 bénéficie également de fonctionnalités avancées pour le spécialiste en charge de la recherche des causes de pannes à l’aide de mesures dynamiques.
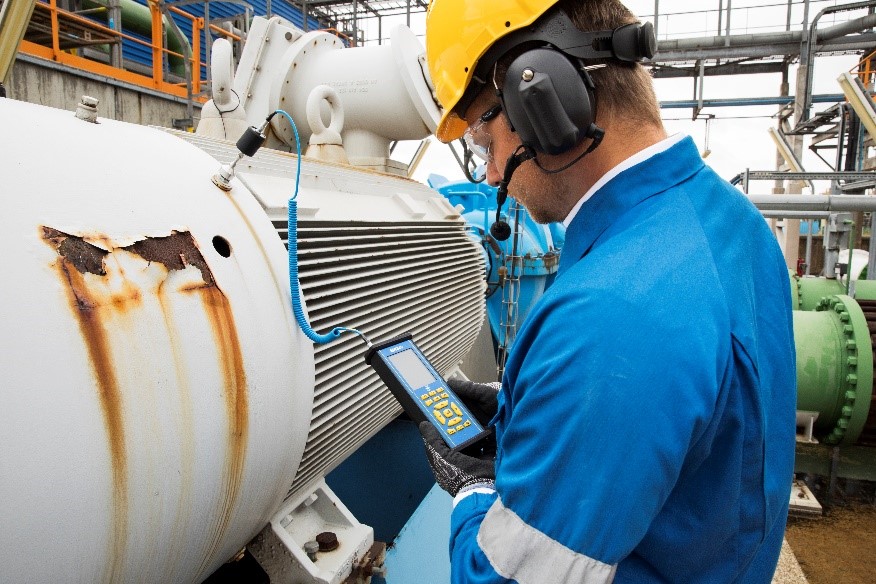
Mesures statiques pour détecter les problèmes
Les mesures statiques (ou mesures globales) sont faciles à mettre en œuvre car leur résultat est un chiffre. Elles sont collectées par le technicien ou l’opérateur en charge de la lubrification et constituent la base d’un programme de maintenance. Elles permettent de créer des courbes de tendance et de mettre en place des seuils d’alarme. Elles visent à prendre une décision rapide sur l’état de la machine : bon ou suspect.
Voici deux exemples concrets :
- Le premier exemple concerne un réducteur de la ligne de transmission principale d’un navire. Des mesures statiques par ultrasons ont permis de détecter un dommage sur l’un des roulements :
- Le deuxième exemple concerne un ventilateur, toujours sur le même poste. La mesure globale a mis en évidence une vitesse de 5,82 mm/s dans la gamme 10-1000 Hz, supérieure au seuil d’alarme de 4,8 mm recommandé par la norme ISO 10816-3. Comme dans l’exemple précédent, les mesures statiques ont permis au technicien de détecter le comportement suspect de ce ventilateur.
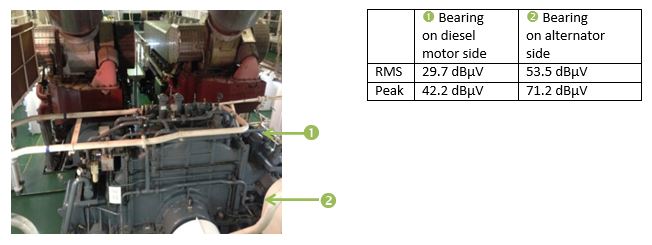
Dans les deux exemples, le technicien a procédé à l’acquisition sur place des signaux provenant des machines incriminées. Ils ont ensuite été analysés par un spécialiste qui n’a pas eu à se déplacer sur place inutilement.
Mesures dynamiques pour un diagnostic plus approfondi
La mesure dynamique consiste en l’acquisition du signal sur une période choisie. Elle permet de générer des représentations temporelles et fréquentielles (FFT). Dans le cas de la technologie des ultrasons, la représentation temporelle est privilégiée. Elle permet par exemple de détecter la présence de chocs répétés par une simple interprétation visuelle. A partir de la référence du roulement et de la vitesse de rotation, l’opérateur pourra identifier l’origine du défaut. Enfin, à partir de l’amplitude des chocs, il évaluera la gravité du défaut.
En ce qui concerne la technologie des vibrations, la représentation des fréquences est plus couramment utilisée. La cinématique de la machine et la connaissance des images vibratoires du défaut permettront au spécialiste de déterminer la cause de la panne. Comme précédemment, la gravité du défaut et son évolution seront évaluées en fonction de l’amplitude des lignes du spectre.
Voici deux exemples concrets :
- La représentation temporelle du signal ultrasonique montre l’apparition de chocs répétés toutes les 0,138 seconde correspondant à la fréquence du défaut de la bague extérieure.gLa représentation temporelle du signal ultrasonique montre l’apparition de chocs répétés toutes les 0,138 seconde correspondant à la fréquence de défaut de la bague extérieure.
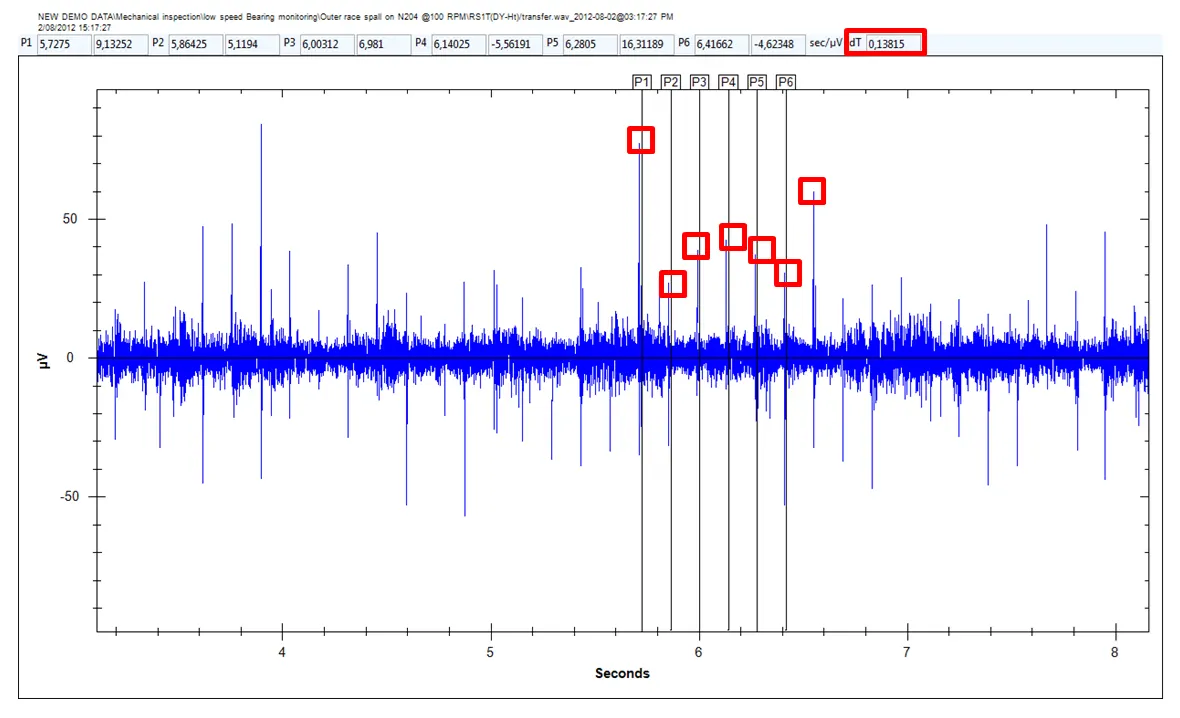
- Le deuxième exemple concerne un ventilateur. Le spectre des vitesses permet de détecter un déséquilibre par la présence d’un pic à la fréquence de rotation de la machine, soit 29,11 Hz, et un problème de soudure sur l’une des 6 pales du ventilateur par un pic à l’harmonique 6 de la fréquence de rotation, soit 174,6 Hz.
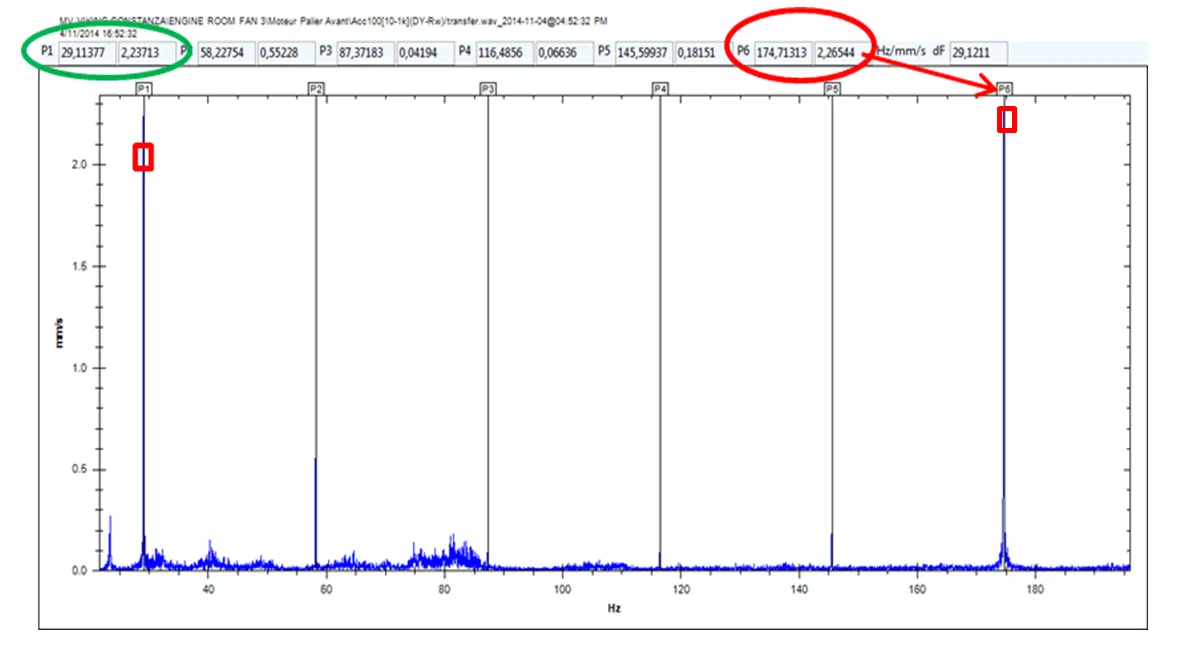