Nelle moderne attività industriali, pochi processi sono più importanti dell’aria compressa e nessun processo richiede un maggiore consumo di energia. L’aria compressa è un’utility fondamentale, che viene utilizzata per il funzionamento dei macchinari, per il trasporto nei sistemi di movimentazione e per la commutazione di strumentazione e sistemi elettrici, solo per citarne alcuni. Tuttavia, la domanda di energia subisce un impatto negativo quando pratiche di manutenzione inadeguate consentono alle inefficienze di andare fuori controllo, e il principale responsabile è rappresentato dalle perdite sul sistema.
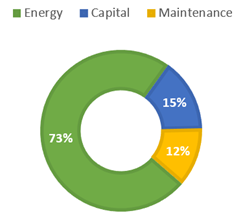
Guardate questa semplice ripartizione dell’investimento tipico che un’azienda dovrebbe fare per un semplice sistema di aria compressa. Il grafico rivela che l’energia rappresenta addirittura il 75% del costo totale del sistema.
Si tratta di una statistica sorprendente, in quanto la logica convenzionale ci farebbe credere che i costi di capitale iniziale e di manutenzione continua dovrebbero dominare. È vero che i costi di capitale per i compressori e i sistemi di erogazione sono significativi, ma non continui. Se un sistema è della giusta taglia e viene manutenuto bene nel tempo, i suoi costi di capitale possono essere ammortizzati.
Un sistema con perdite e scarsa manutenzione non soddisferà mai la domanda, prosciugherà continuamente le risorse e avrà un impatto negativo sull’energia. Un sistema inefficiente che spreca energia danneggia ulteriormente l’ambiente attraverso ulteriori e inutili emissioni di gas serra.
Il fatto che non sempre si pensi all’aria compressa in termini di consumo energetico spiega perché si presti così poca attenzione alla ricerca e alla riparazione delle perdite. Le perdite sono costose. Secondo il Dipartimento dell’Energia degli Stati Uniti, i sistemi medi sprecano tra il 25 e il 35% dell’aria solo a causa delle perdite. In un sistema da 1.000 SCFM, il 30% di perdite si traduce in 300 SCFM. Eliminare questa perdita equivale a risparmiare più di 45.000 dollari all’anno (a seconda del luogo in cui si trova l’impianto e dei costi energetici della regione, l’importo risparmiato può essere da tre a quattro volte superiore).
Per arrivare al nocciolo del problema è necessaria una migliore comprensione della compiacenza in materia di perdite. Perché prestiamo maggiore attenzione all’efficienza energetica dell’illuminazione (d’accordo, ci sono benefici da ottenere grazie ad una buona illuminazione e con usi efficienti) e continuiamo a ignorare i sistemi di aria compressa inefficienti? Una spiegazione è che le perdite di aria compressa non si vedono. Sono cresciuto sentendo i miei genitori dire “non lasciare le luci accese”, quindi l’illuminazione efficiente mi è stata insegnata fin da piccolo. Non hanno mai parlato di perdite. Eppure, ricordo ancora le linee aeree che perdevano aria nell’officina di mio padre.
In fabbrica, una perdita di vapore è evidente e una perdita di olio lo è ancora di più. Invece, le perdite d’aria non creano un pennacchio visibile e non sporcano il pavimento in modo pericoloso e scivoloso. Non hanno un odore sgradevole e, per lo più, ignoriamo o non sentiamo il loro sibilo continuo.
Quindi, è davvero un caso di “lontano dagli occhi, lontano dal cuore”? Lo spreco di energia e l’inefficienza del sistema sono ancora una priorità bassa per i produttori? Forse l’aria compressa è un processo di fondo dato per scontato? Considerate il vostro sistema di aria compressa e tutte le aree in cui la pneumatica è impiegata nella vostra struttura. Espandete la vostra riflessione oltre le mura della fabbrica, dove l’aria compressa rende possibili molte cose nella scienza, nella tecnologia e nella vita di tutti i giorni. Dai martelli pneumatici per le riparazioni stradali ai trapani sulla poltrona del dentista, dai pneumatici che ci fanno andare e tornare dal lavoro, dalla scuola e dal gioco, ai palloni da calcio e da basket gonfiati per i nostri figli, l’aria compressa è ovunque intorno a noi… e sì, è data per scontata.
Si sta verificando un cambiamento culturale nell’industria, dove è più necessario. L’industria rappresenta il maggior consumatore e, quindi, il maggior guadagno potenziale. Si tratta di una doppia sfida e di una doppia opportunità. La sfida consiste nell’investire in un’energia più efficiente e in pratiche consapevoli dal punto di vista ambientale. L’opportunità è migliorare la redditività e rallentare gli effetti del riscaldamento globale. Abbiamo un’insaziabile sete di elettricità e i combustibili fossili necessari a placare la nostra sete si stanno consumando a ritmi che non possiamo permetterci. Due effetti collaterali che riguardano tutti sono la diminuzione dell’offerta di fonti di combustibile non rinnovabili e l’effetto che l’aumento dei livelli di CO2 ha sul cambiamento climatico globale. La diminuzione dell’offerta significa un continuo aumento dei costi dell’energia, mentre il cambiamento climatico globale rappresenta qualcosa di molto più costoso.
Non tutte le aziende se ne stanno con le mani in mano ad aspettare che altri agiscano. Molte hanno già avviato programmi che riguardano l’efficienza energetica e si rivolgono specificamente al sistema dell’aria compressa. AFG Glass è il secondo produttore di vetro del Nord America e il più grande fornitore del mercato del vetro per l’edilizia e di quello speciale. Fondata nel 1978, AFG ha sede a Kingsport, nel Tennessee. Con le sue tre divisioni, è un fornitore completamente integrato. Una divisione si occupa della produzione di vetro piano, un’altra di rivestimenti avanzati ad alta efficienza energetica e una terza divisione di fabbricazione che aggiunge valore al prodotto finito attraverso la tempra, la laminazione e l’isolamento. In totale, AFG ha nove stabilimenti di produzione del vetro, 34 centri di produzione/distribuzione, 4 linee di rivestimento, 5 impianti di isolamento e un impianto di laminazione. Gli impianti in Nord America contano più di 4.800 dipendenti.
AFG ha implementato programmi di rilevamento ad ultrasuoni in alcune delle sue divisioni produttive. Gli ultrasuoni sono stati presi in considerazione soprattutto per la loro reputazione come strumento di manutenzione predittiva e di risoluzione dei problemi. Quando diversi tecnici hanno frequentato il Level 1 Ultrasound Certification Training, hanno capito che la tecnologia in cui avevano investito sarebbe stata utilizzata per molto di più che per la risoluzione dei problemi.
I rilevatori di perdite ad ultrasuoni funzionano come semplici microfoni sensibili ai suoni ad alta frequenza che vanno oltre l’orecchio umano. Ci permettono di sentire i problemi dei macchinari in fabbrica, indipendentemente dal rumore di fondo. I rilevatori di ultrasuoni possono essere semplici rilevatori di perdite o raccoglitori di dati avanzati in grado di analizzare e diagnosticare i guasti alle macchine e le inefficienze dell’impianto.

Un tipico impianto di aria compressa può essere ispezionato per individuare le perdite in uno o due giorni. Gli impianti più grandi possono richiedere più tempo, ma i vantaggi di trovare e riparare le perdite valgono l’investimento di tempo.
Douglas Bowker è il Responsabile di Manutenzione alla AFG Industries Greenland, impanto TN. Ha contribuito in modo determinante all’implementazione di test ad ultrasuoni per migliorare il benessere delle apparecchiature dell’impianto.
“L’aria compressa non è gratuita”, scrive Bowker. “La fornitura di aria compressa all’impianto costa a Greenland circa 137.000 dollari all’anno. Quindi le perdite d’aria ci costano soldi. Una piccola perdita non rilevata dall’orecchio umano può contribuire a un costo di 3.000 dollari all’anno. L’apparecchiatura ad ultrasuoni può ora essere utilizzata in modo da risparmiare sui costi per rilevare tali perdite e ripararle in modo proattivo”.