Dibamba Power Development Company è una centrale elettrica a olio combustibile pesante, il primo produttore indipendente di energia elettrica in Camerun. L’azienda, che opera nel settore della produzione di energia elettrica in Camerun e fa parte del Gruppo Globeleq, ha l’obiettivo di partecipare alla crescita dell’Africa attraverso lo sviluppo e la gestione di centrali elettriche.
La centrale elettrica a olio combustibile pesante di Yassa-Dibamba richiede aria compressa a due livelli di pressione: 30 bar per l’avviamento dei motori dei compressori dell’aria e 7 bar per la strumentazione ausiliaria. Per produrre l’aria per i macchinari, l’impianto dispone di 3 compressori d’aria che funzionano più di 5.000 ore all’anno con tempi di stand-by molto brevi.
Per ottimizzare i costi e garantire la disponibilità contrattuale delle sue macchine, l’azienda ha pensato di applicare soluzioni proattive che le consentissero di anticipare i diversi guasti delle macchine e di pianificare meglio le azioni di emergenza necessarie.
Utilizzando il loro nuovo rilevatore ad ultrasuoni SDT340 e il suo sensore flessibile, hanno iniziato a cercare le perdite d’aria per migliorare la loro efficienza, dato che uno dei compressori è attualmente fuori servizio.
Questa ricerca li ha portati a identificare diverse fonti di perdite d’aria, alcune delle quali potevano essere corrette istantaneamente, mentre altre richiedevano ulteriori interventi.
Ad oggi, gli effetti sono convincenti. Nonostante alcuni interventi siano ancora in fase di attesa, i tecnici della manutenzione sono già stati in grado di osservare effetti istantanei, ovvero la riduzione del numero di ore di funzionamento dei compressori rimanenti, fino al 30%. Ciò si traduce in una riduzione di oltre 4 ore al giorno, per compressore, nelle ultime due settimane. E questo nonostante l’assenza di uno dei compressori. L’impatto sarà quantificabile con i costi relativi al consumo energetico e alla manutenzione in base alle ore di funzionamento e quindi al consumo annuale di materiale.
Le ricerche sulle perdite di aria compressa hanno permesso di ridurre lo stress sui compressori d’aria in fase di avviamento e quindi i costi legati al loro funzionamento, per citare solo alcuni esempi. L’applicazione LEAKReporter ha aiutato il management a comprendere l’impatto di queste ispezioni da un punto di vista finanziario, con analisi molto semplici da visualizzare.
Sono in corso studi per definire la periodicità dei cicli di ispezione regolari per mantenere o addirittura migliorare queste condizioni.
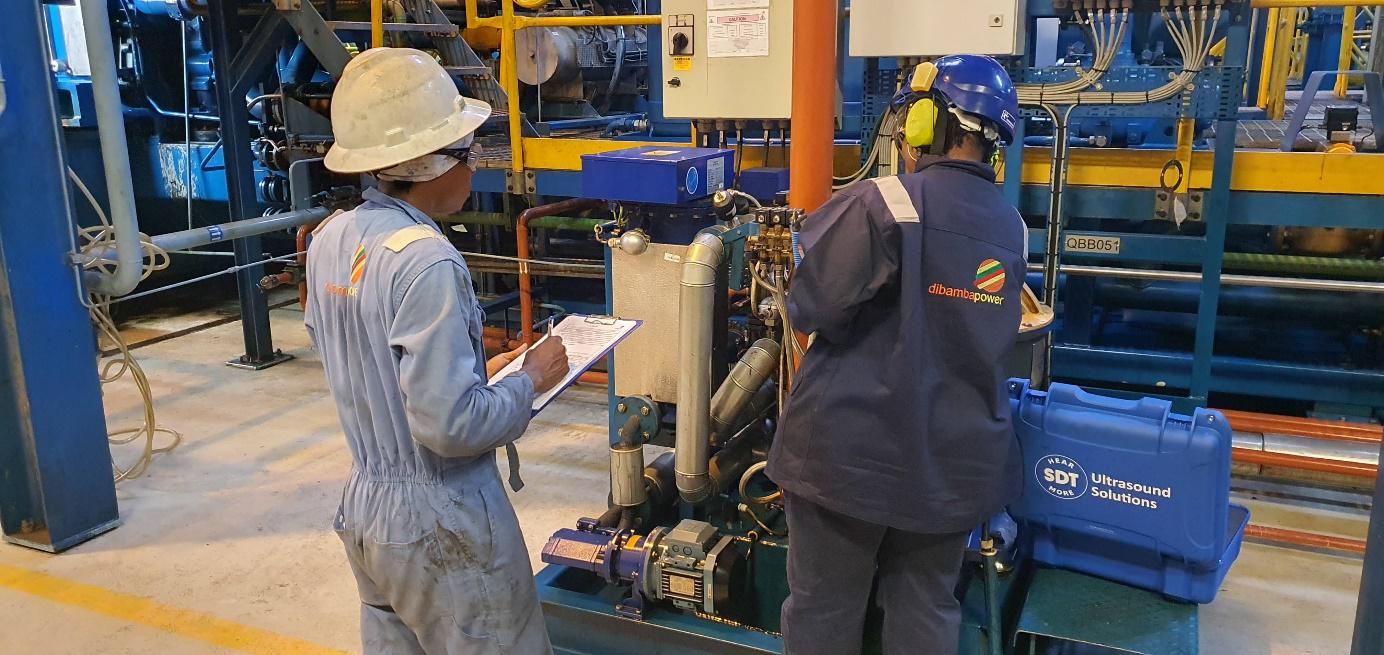
L’olio combustibile pesante, per dare uan idea, richiede un processo di trattamento piuttosto complesso che sollecita diversi macchinari, la maggior parte dei quali dotati di pompe a vite che, prima del 2019, erano le principali fonti di spese per la manutenzione dell’azienda, con una media di 200 milioni di franchi CFA (franco centrafricano) spesi all’anno. Questo dato non include i tempi di inattività dovuti a guasti, e nemmeno gli straordinari generati dalle squadre di manutenzione su chiamata.
L’affidabilità degli impianti dipende dallo stato dell’importante numero di sistemi ausiliari (pompe, separatori centrifughi, compressori e altri) che contribuiscono alla produzione degli 8 gruppi che la centrale conta, ognuno dei quali può produrre 11MW (potenza installata).
Nel caso di queste pompe a vite, sono state messe a punto delle ispezioni di routine ad ultrasuoni che, insieme alla definizione di valori di riferimento base, hanno permesso di monitorare gli stati di guasto per raccomandare azioni correttive/proattive in tempo utile per evitare dei fermi. Questo ha permesso di ridurre notevolmente i costi di manutenzione fino all’80% sulle pompe a vite.