Sensori e strumenti: i punti chiave
I sensori a contatto ad ultrasuoni sono sensori risonanti. La loro sensibilità è un punto importante, ma non l’unico. La base del Condition Monitoring è il trend dei dati e l’esecuzione di un’azione correttiva quando scatta un allarme. Se non avete la garanzia che due sensori forniscano un risultato simile per lo stesso segnale, cambiate fornitore. I dati storici e le soglie di allarme diventano inutili quando si sostituisce un sensore difettoso!
Pertanto, come per tutte le tecnologie, le caratteristiche del trasduttore: sensibilità e frequenza di risonanza, devono essere chiaramente specificate e certificate dal produttore. SDT è in grado di fornire tali garanzie perché è in grado di offrire ai clienti sensori con una qualità di ricezione delle misure standardizzata.
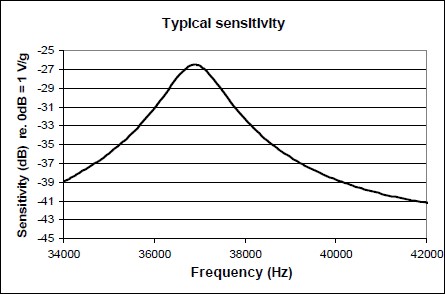
Specifiche del sensore filettato SDT RS2T
La stessa osservazione vale per il dispositivo di misura. Gli strumenti devono essere calibrati e intercambiabili senza indurre variazioni di misura. Idealmente, l’ingresso che riceve il segnale del sensore deve essere sotto controllo, non necessariamente l’uscita audio eterodina.
L’ascolto è la prima linea di difesa.
La prima funzionalità di un dispositivo ad ultrasuoni è quella di trasformare le alte frequenze in suoni udibili. L’operazione è chiamata eterodina. Chi non ha familiarità con gli strumenti ad ultrasuoni pensa che si tratti di un metodo antiquato e superato. In realtà non è così, soprattutto quando si ispezionano macchinari a bassa velocità. Un operatore senza conoscenze approfondite può distinguere un cuscinetto sano, che produce un segnale silenzioso e costante, da un cuscinetto difettoso, che provoca un suono intermittente o specifico e ripetitivo.
Tuttavia, l’ascolto non è sufficiente. Per costruire un solido programma PdM sono necessarie misure affidabili. Altrimenti, lo strumento non è altro che uno stetoscopio.
Misure statiche per il rilevamento dei guasti
Le misure statiche (valori complessivi) sono semplici da implementare, poiché il risultato è costituito da numeri. Sono facili da gestire per la memorizzazione, l’andamento delle curve e l’attivazione di allarmi. Per i cuscinetti a bassa velocità, si utilizzano due indicatori forniti dalle misure statiche: l’RMS, che caratterizza l’energia del segnale, ed il Picco, che caratterizza l’ampiezza del segnale. Combinando questi due indicatori, è possibile individuare facilmente gli inizi dei difetti.
Esempio di risultati di dati Statici
Ecco il confronto dei dati provenienti da un macchinario che funziona a 50 giri/minuto, utilizzando un tempo di acquisizione di 20 secondi:
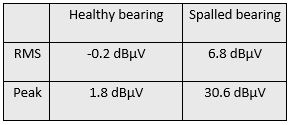
Misura dinamica: dal rilevamento alla diagnosi
In alcuni casi, ad esempio per un macchinario complicato o per guasti inaspettati e ripetuti, l’utente desidera andare oltre l’obiettivo di determinare la presenza di un guasto. L’esigenza può essere quella di determinare quale componente sia difettoso. Questo è il processo di diagnosi eseguito grazie alle misure Dinamiche.
Una misura Dinamica consiste nell’acquisizione di dati per una durata di tempo selezionata. Viene utilizzata per elaborare rappresentazioni nel dominio del Tempo e nel dominio della Frequenza (FFT o Spettro). Per la tecnologia ad ultrasuoni, la rappresentazione nel dominio del Tempo è lo strumento preferito, perché il segnale temporale lavora anche con eventi intermittenti e fornisce informazioni potenti sulla natura del guasto e sulla sua gravità.
In primo luogo, la forma del segnale temporale indica la presenza del difetto con l’interpretazione visiva del segnale temporale, mostrando, ad esempio, impatti ripetitivi. Il segnale temporale può essere analizzato in modo identico all’analisi delle vibrazioni per fornire un’indicazione della causa del guasto. Come per le vibrazioni, sono necessari la velocità di rotazione della macchina e uno schema dettagliato. Nel caso di un difetto del cuscinetto in fase avanzata, l’operatore può misurare la durata tra gli impatti. Il confronto con le frequenze note di rotazione dei 4 elementi del cuscinetto, identifica precisamente l’elemento difettoso, e di conseguenza, la causa del difetto. Infine, l’ampiezza dell’impatto è spesso un buon indicatore della gravità del guasto.
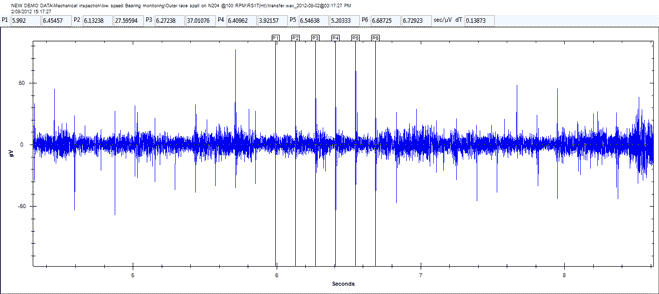
dynamicdata1
La durata tra impatti adiacenti fornisce la frequenza del difetto sul cuscinetto.
Esempio di risultati di dati Dinamici
Ecco il confronto nel dominio del Tempo proveniente da un macchinario che funziona a 25 giri/minuto, utilizzando un tempo di acquisizione di 5 secondi.
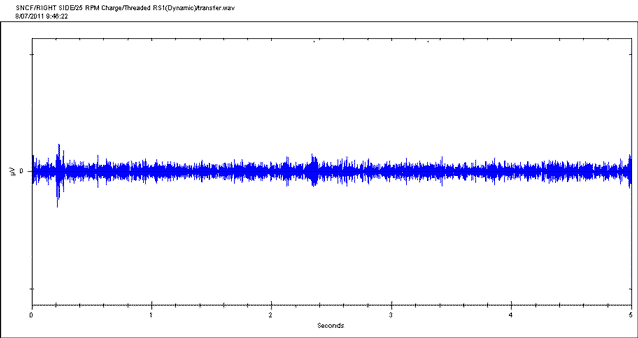
dynamicdata2
Segnale nel Tempo di un cuscinetto sano
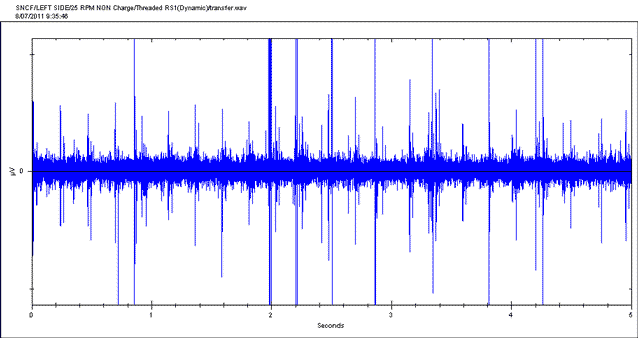
dynamicdata3
Segnale nel Tempo di un cuscinetto difettoso
Nota: per i due segnali temporali sopra riportati è stata utilizzata la stessa scala verticale.
La durata tra gli impatti corrisponde alla frequenza di passaggio della sfera sulla pista esterna (BPFO). La diagnosi è che il cuscinetto presenta dei danni sulla pista esterna.
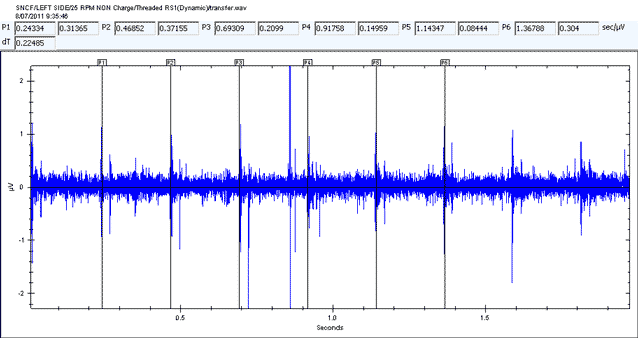
La durata indica la frequenza del difetto sul cuscinetto.
La diagnosi è di danneggiamento della pista esterna di questo cuscinetto.
Il Bearing Toolbox
Per rendere la vita ancora più facile ai tecnici della manutenzione quando effettuano queste diagnosi, SDT ha sviluppato un Bearing Toolbox nel software UAS3. Niente più lunghi calcoli e ricerche infinite nei manuali dei produttori di cuscinetti per trovare i dati necessari. Con questa funzione, si può semplicemente selezionare un cuscinetto dal database (oltre 50.000 riferimenti), quindi inserire la velocità di rotazione del macchinario per identificare se un segnale acquisito (vibrazione, ultrasuoni) corrisponda o meno ad una delle quattro frequenze di guasto note del cuscinetto.
Guardate questo video informativo per capire meglio quanto si possa risparmiare tempo!
Conclusione
In definitiva, gli ultrasuoni sono un metodo eccellente per trattare i macchinari a basso numero di giri.
I vantaggi offerti da questa tecnologia sono evidenti: efficienza, semplicità, possibilità di combinare un facile rilevamento con una diagnosi più elaborata e risparmio di tempo grazie al Bearing Toolbox.
Ricordiamo l’osservazione pertinente di un Responsabile di Manutenzione: “Il mio reparto non ha il budget per coprire le spese di un team di 5 esperti di vibrazioni. Inoltre, con 5 persone, monitoreremmo solo le macchine critiche. Con i nostri strumenti ad ultrasuoni, la prima linea di difesa è gestita da tecnici di base, anche i tecnici della lubrificazione, e la maggior parte delle macchine viene ispezionata regolarmente. L’80% dei problemi riscontrati viene risolto con gli ultrasuoni. Il mio singolo esperto di vibrazioni viene utilizzato per risolvere il restante 20%”.
LUBExpert in modalità Dinamica può aiutare in situazioni come questa. Infatti, il tecnico della lubrificazione può effettuare le misurazioni durante la lubrificazione, in modo che il team di Condition Monitoring (CM) non debba controllare nuovamente queste macchine.
SDT ha una soluzione, si chiama Ultrasuono.