Every plant is different. The machines inside them, the production processes they power, and the loads and conditions in which they operate. But one thing almost all share in common is bearings on rotating equipment. Bearings are the driving force behind industry, and it is the grease that helps them run smoothly and last longer.
While almost every plant in the world has rotating equipment and almost every maintenance technician is familiar with bearing grease replenishment, bearings are still a sadly misunderstood asset. Which is why as much as 80% of all bearings fail prematurely.
SDT Ultrasound Solutions has helped manufacturers across the globe properly grease millions of bearings through training, technology, and services. Throughout our journeys across the world trying to improve bearing reliability we’ve noticed these three common bearing greasing mistakes, and we want to share them with you.
Bearing Grease Replenishment Mistake 1: Calendar Base Greasing
Performing bearing grease replenishment once per week or once a month may seem like a sensible thing to do. After all, performing scheduled maintenance at regular periods is an age-old concept ingrained in each of us early on. Even OEMs still advise best practices based on time intervals to ensure maximum asset lifespan.
The problem with any blanket solution is that they ignore the effects of variables.
Two motors may be the same out of the box but end up in entirely different situations. While one lands in a hot and humid climate, another could be installed in a cold and arid climate. One may be used in a high-speed low load application while another at low speeds but with frequent starts and stops.
Bearings need grease for one reason only; to reduce friction. As long as the grease is performing that service well, there should be no need to change it. Yet we frequently do, with catastrophic results.
Replenishing bearing grease just because your calendar told you “time’s up!” is the first mistake. Monitor ultrasound friction and know when it’s the right time to grease
Bearing Grease Replenishment Mistake 2: Over and Under-Greasing your Bearings
The second mistake we should all avoid is adding too much, or not enough bearing grease. Too much grease builds up pressure pushing the rolling elements through the fluid film and against the outer race. Increased friction and temperature dramatically shorten your bearing’s life. Not enough grease will have the same life-shortening effect.
How do we know when just the right amount of grease has been added? Ultrasound of course. Listen to the bearing and measure the drop-in friction as the grease fills the bearing cavity. As the decibel level approaches normal baselines and stabilizes carefully slow the application of lubricant. Should the decibel level begin to increase slightly, STOP! The job is done.
Bearing Grease Replenishment Mistake 3: Relying on Subjective Bearing Data
Like any job there is a right way and a wrong way to do things. Simply listening to a bearing with an ultrasound device that gives no quantitative feedback is a recipe for disaster. The audible feedback is too subjective to draw any comparative conclusions. No two people hear the same and there is no way to remember what the bearing sounded like a month ago.
The third mistake is depending solely on subjective ultrasound data when precise quantifiable data is available. Always use an ultrasound instrument with digital decibel metering. Better still, use a device that provides multiple condition indicators. Max and Peak RMS decibel measurements indicate alarm levels and greasing intervals while Ultrasonic Crest Factor provides insight about the bearing condition in relation to its lubricant. Crest factors help us differentiate between bearings that need grease and bearings that need to be replaced.
Bearings produce less friction when they are properly greased. But how do we know?
- How can you be confident that friction forces are where they should be?
- How can you confidently apply just the right amount of grease to return friction levels to normal?
- How can you distinguish between a bearing that need grease and a bearing that is failing?
Ultrasound Helps!
Using an ultrasound measurement tool with digital decibel metering is a proven method for:
- Establishing a historical baseline for friction levels
- Monitoring changes in friction levels at regular intervals
- Triggering alarms when friction levels elevate
- Evaluating data to differentiate failure from friction
The basic concept of CBM (Condition Based Maintenance) is to monitor the condition (CM) of a machine over time and use conditional data to predict the need for maintenance to take action (PdM). Let’s apply this concept to a bearing grease replenishment task on a rolling element bearing
Using an SDT ultrasound instrument (simple or advanced), lube-techs collect data which indicates the current condition of the bearing. What are some of the Condition Indicators collected by SDT?
Simple “STATIC” Condition Indicators
Ultrasound STATIC data provides an instantaneous snapshot about bearing condition.
- RMS – The average of the ultrasound signal over the duration of the measurement time
- Max RMS – The highest RMS signal observed over the duration of the measurement time
- Peak – The highest amplitude observed over the duration of the measurement time
- Crest Factor – A linear ratio between the Peak and the RMS (CF=Peak/RMS)
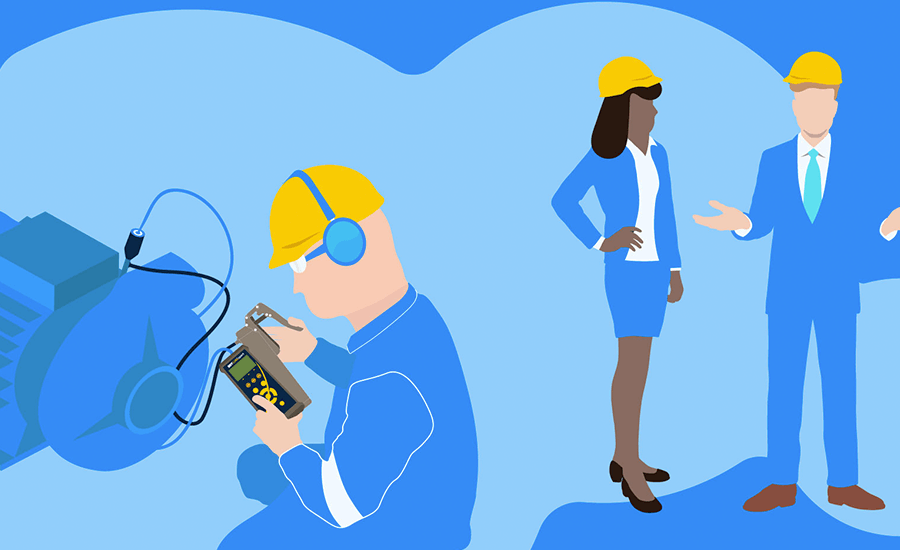
LUBExpert Essentials™
Our comprehensive body of knowledge is designed to help you Grease Bearings Right. Whether you are a Lube Tech, Lube Engineer, Lube Strategist, Reliability Engineer, or Reliability Leader, LUBExpert Essentials starts you on the journey to creating a world-class lubrication team.
LUBExpert Essentials™ is a two-part course consisting of 16 modules. In total, there are more than 20 hours of mentor-lead instruction, inter-modular quizzes, followed by an exam that, challenged successfully, awards you with your very own digital LUBExpert Essentials Badge.
Posted by Tristan Rienstra