Ultrasound… Your first line of defense for Condition Monitoring
Ultrasound is considered the first line of defense for finding defects that can lead to asset failure.
The first signs of change in the operating condition of an asset are usually indicated in the ultrasound frequencies.
Only after the asset has progressed to a more severe stage of deterioration do other asset condition monitoring technologies begin to play a role.
For planners and schedulers, having the largest window of opportunity possible to order parts, plan downtime, and allocate labour represents a tremendous advantage.
Ultrasound is one of the three classification of sound:
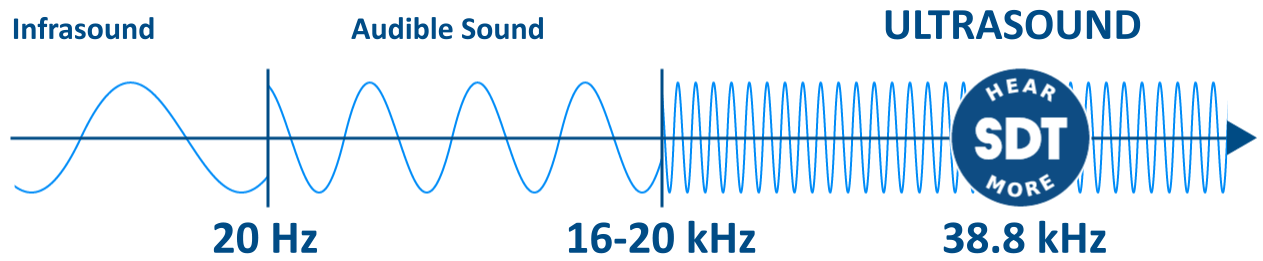
Besides Infrasound and Audible sound, Ultrasound refers to any sound pressure wave with a repetition frequency greater than 20 kHz. The characteristics of ultrasound, especially around 40 kHz are particularly interesting for inspectors listening for symptoms of assets failure.
Friction – Impact – Turbulence
SDT Data collectors, such as the SDT340 or the SDT270, let you detect, measure and analyze friction and impacting in mechanical systems. Turbulent flow from compressed air and steam leaks helps you quickly identify costly energy waste. Ultranalysis® Suite software lets you establish baseline readings and set alarms that tell you when your equipment is transitioning from good to bad.
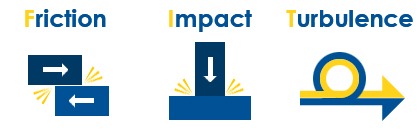
The Four Condition Indicators (4CI)
In the world of asset condition management you need dependable data to inform you about the condition of your production machines.
Before 4CI, ultrasound inspectors trended ultrasound data based on a single decibel measurement taken at an arbitrary point in time. Capture the measurement at the wrong time and the defect was either missed, or amplified beyond reality. 4CI allows inspectors to set the acquisition time prior to capturing the measurement. The result is a more representative and accurate collection of data.
By monitoring these four numbers on your ultrasound solution, you’re able to keep a pulse on the health of your facility and move from a reactive maintenance program to a condition-based approach.
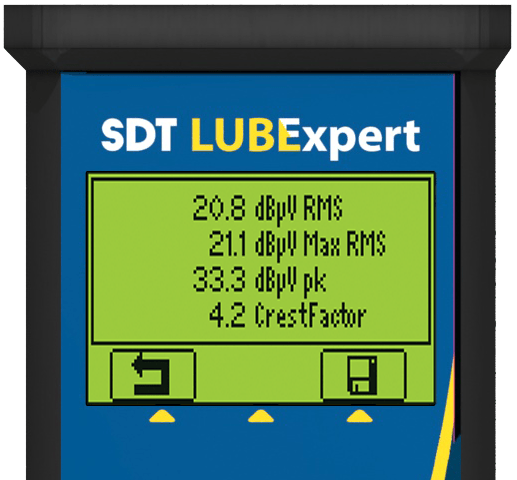