Hydraulic Systems Monitoring
Non-rotating asset components seldom receive the routine surveillance they need
Hydraulic systems represent another way industry converts electricity to mechanical energy. A pump, normally powered by an electric motor, moves hydraulic fluid through a system. The system is typically made up of a reservoir to hold the hydraulic fluid, high pressure lines to carry the fluid, control valves that ensure the fluid is sent where needed, relief valves for safety, and cylinders to produce mechanical energy.
The pump and motor receive attention while the balance of the system is run-to-failure. Surely, ultrasound testing could change this lackadaisical approach; especially considering its versatility, ease of use, and applicability to most hydraulic defects.
How to detect hydraulic leaks? What are the most common failure modes?
Failure modes in hydraulics systems include external leakage, internal leakage, by-passing, and blockages. Ultrasound detects them because they produce Friction, Impacts, and Turbulence.
- Friction
- Bearings in the motor and pump
- Rubbing of the head against the inside of the barrel
- Rubbing of the rod against the gland seal
- Impacting
- Cavitation on the vacuum (inlet) side of the pump
- Cavitation on the discharge (pressure) side of the pump
- Bearing and coupling failure
- Turbulence
- Passing fluid past the head seal or wiper
- Passing fluid past the valve body of an isolator valve
- Bursting of small bubbles on any internal leak.
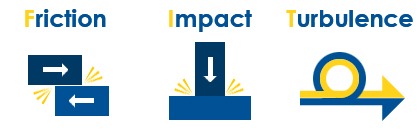
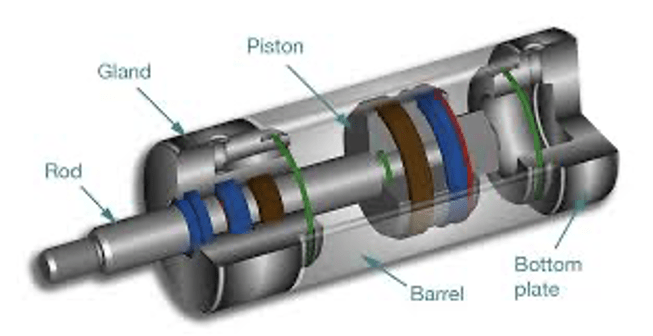
External and Internal Leaks
Visual inspections can be helpful to detect external leaks. Some external leaks, like a ruptured hose or fitting, are easy to spot. Simply follow the trail of spilled oil. Meanwhile, others are not so obvious. These slow seeping leaks weaken system function gradually until failure. It is uncommon for them to produce any usable ultrasound signal for inspectors to detect. As a result, the best one can hope for is to trace the pooling of oil back to its source.
Internal leakages are surprisingly more detectable with ultrasound than external. That’s actually opposite thinking when compared to compressed air and vacuum leaks. An internal leak in a hydraulic cylinder slowly passes by the seal on the piston. Therefore, the best position for the contact probe is downstream from the fluid flow.
Valves
Valves play a critical role in hydraulic systems. Simple or complex, their job is to direct the flow of fluid to where it’s needed. There are many opportunities for ultrasound to detect problems in hydraulic valves.
A two-way valve controls fluid flow through two paths. One path allows mechanical movement to extend the cylinder and the other contracts. When that valve is either passing or blocked the system loses functional ability.
An isolation valve stops the flow of hydraulic fluid in a given direction. Isolators are usually used for maintenance on the system or for safety reasons. They may be used to temporarily stop the system while ancillary equipment is connected. A functional isolator should have no downstream flow. Place a contact sensor above, on, and below the direction of flow. Then, listen for turbulence either in the form of a steady stream or bursting bubbles on the downstream side. The differences may be slight so comparing dBµV values at all three positions should prove enlightening.
What Happens if we do Nothing?
Many opportunities exist to advance the reliability of hydraulic systems with ultrasound. Just because they don’t rotate does not mean they cannot contribute to unscheduled downtime. Therefore, reliability teams need to elevate the importance of hydraulic systems in their condition monitoring regimens. Today’s technology is simple and effective. For this reason, run-to-failure on hydraulic systems powering critical processes is inexcusable.