But Run to Failure is not an Option
Nearly all facilities Electric Motors are dominated by Seal For Life Bearings, the shear number poses an challenge to Asset Strategies.
The default strategy often chosen is to Run to Failure and replace as quick as possible, but this causes multiple downtime events which adds up over a year to be of concern. Half an hour here, and another hour there doesn’t bode well in this reactive environment.
Some facilities utilize Vibration Analysis but due to costs of Data Collection or Wireless Sensors small motors are often left off the list.
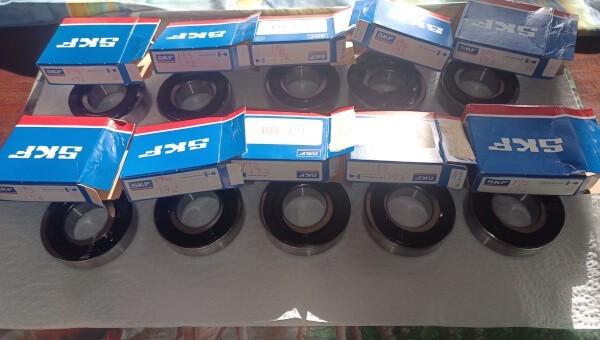
An alternative is to replace Motor, Pump, Conveyor, Agitators, Blowers, Vibrators etc during a shutdown. As with All Shutdowns resource is limited as is Time and many scheduled replacements are achieved. So good intentions of having NEW bearings is nearly always suboptimal, with lots of Assets being missed, and therefore the Run to Failure strategy is adopted.
While the implementation of Time Based replacements is difficult to manage there is a more concerning factor in this strategy.
Grease Charge affects Bearing Life
Many guidelines state Greased bearings should have approximately one third the volume filled with clean grease. The assumption is Sealed Bearings are filled to this guideline.
The Grease Service Factor (Ultimately the Bearing Life) is dominated by Grease Charge provided the Bearing isn’t overfilled.
This article explores the actual Grease charge in Sealed Bearings
On two occasions 3Phi Reliability has gently opened Newly purchased Sealed Bearings from an OEM supplier. These bearings were weighed initially and then reweighed once Ultrasonic cleaned removing all traces of the original grease.
The Results
One has 12grams, and the other 5 grams.
What this means is Grease Service Factor proportional to Grease Charge can vary by more than 200%, therefore the variability in Bearing Life is greatly determined by manufacture.
It appears in both these occasions the Initial Total weights are within a gram (Resolution of the scale) suggesting the grease fill is controlled to a total weight, irrespective of the Dry bearing weight.
Grease depletion is proportional to the initial Grease charge therefore it’s impossible to conduct a Time based replacement program with any accuracy.
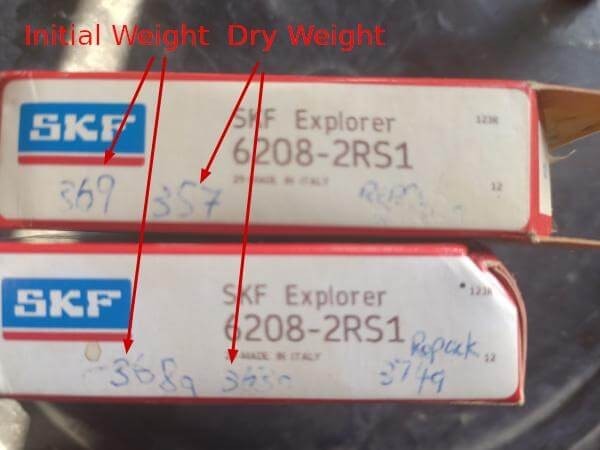
Time Based Replacements
A facility which has addressed Balancing, and Alignments, Environmental Conditions, Resonance and many other Reliability good practices is still not going to be able to define the timing for Replacements due to Grease Charge variation.
The strategy is Time Based Replacements is therefore extremely difficult to manage and is going to be sub optimal even under the best conditions.
Time Based replacements therefore are Expensive and don’t provide the reliability needed in a Best Practice Reliability Program.
Recommended Strategy
Due to the unpredictable nature of Sealed Bearing life this situation lends itself to On Condition monitoring and when the Grease has depleted and friction levels rise a targeted replacement program is implemented.
This strategy is not affected by Environmental & Grease variations and maximizes service life and gains optimal reliability.
Due to cost constraints stated above a strategy needs to be integrated into Lubrication technicians existing resource, and take approximately the same time.
A Report of any change in friction levels can then be highlighted to a Vibration Analysis program, and close attention can be made. Lubrication Activities must align closely to Vibration Analysis and communication is vital, but often not attempted. Back office analysis struggle here especially if off site and misdiagnosis is common.
This has analogies of Hospitals, where trained nurses do much of the monitoring, application of medication, tests, patient inspections and observations. Deviations are reported for Doctor rounds.
“SO SEND FOR NURSES”
This hospital strategy optimises skills, lower total cost of ownership, and gets a controlled outcome.
How to achieve this Strategy
A well known technology of Ultrasonics is well suited to measuring friction levels in Bearings and other components. The use of Ultrasonic in a Lubrication strategy can optimise friction levels by providing the Right Amount, at the Right Time and for Sealed Bearings determine when grease depletion has occurred before failure.
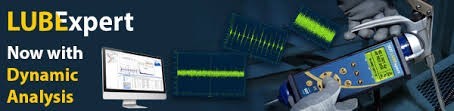
An instrument coupled inline with a grease gun or swapped for a magnet mounted sensor for Sealed Bearings takes a Ultrasonic measurement which is much more directional than Vibration Data due to the frequency attentuation.
By trending these readings a for Sealed Bearings and tayloring alarm limits based on history an accurate assessment can be made of Lubrication condition.
When Sealed for Life Bearings grease deplete then a planned intervention can be made.
Further Blog post at https://www.3phi-reliability.com/blog/how-to-manage-small-sealed-for-life- bearings-in-motors
An acoustic camera can be used to identify lubrication defects but the difficulty arises in Controlled Data collection and getting consistant on regular collection points. This strategy requires a trend to be established. Acoustic camera will identify gross problems and may be worthwhile to get into control quickly. It is recommended to hire or have an initial survey with a camera.
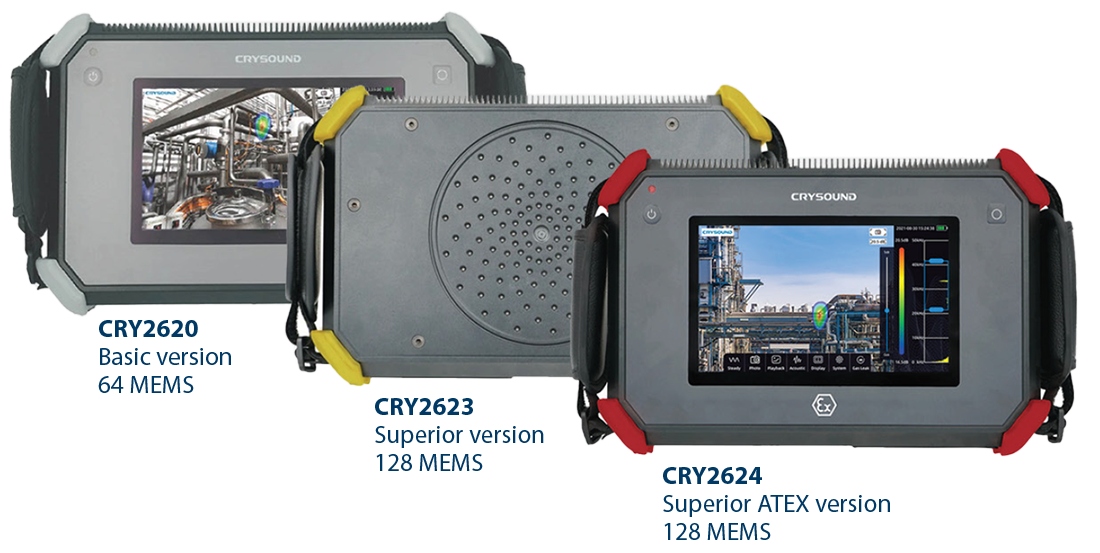
Effects of the “On Condition” Strategy
This strategy allows for the bearing to remain in service until the Lubrication depletes and due to many variables maximizes service life. The defect can be detected early allowing planning for replacement to be made.
The number of defects at any one time is far less than a time based replacement program therefore easier to manage. Either strategic spares or vendor purchase can take place in a lower stressed environment.
Provided this planning is managed well and use of existing maintenance windows the Unplanned Downtime to the facility can be lowered to a much more acceptable level.
The cost of implementing this strategy has a very high Return on Investment and a single downtime event overted often outweighs the Time & Effort.
This strategy provides the opportunity for a facility to reinforce the culture of Best Practice Motor Management and Break the Reactive Cycle which often plaques maintenance teams.
These reliability wins celibrated and backed by training builds a great culture, making your facility a place people like to contribute. Elevating Lubrication to Best Practice ensures the contribution of your Lubrication technician is appreciated and worthwhile, and maintains job satisfaction.
This is Only half the story
The reason 3Phi Reliability cleaned those bearing was to repack them with a Poly-urea based thickener in an application of high moisture. The grease used was Mobil Polyrex EM.
Poly-urea based thickeners can be incompatible with other greases so Sealed Bearings are an ideal application as greases can not be mixed.
A trail at a dairy plant showed using Poly-urea thickeners over Standard lithium thickeners outlasted by a factor of at least five times. This has a massive impact on the total cost of ownership.
The strategy of on condition replacement plus changing thickener type is proven return Reliability and Cost savings and is part of 3Phi Reliability Best Practice Motor Management.
Our Bearing Vendor organized for the repacking of Sealed Bearings as the lead time to source Poly- urea thickener was in excess of 12 months.
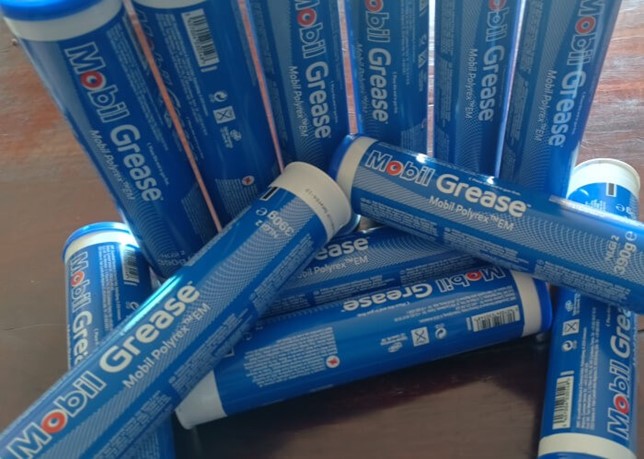
Chula Jayawardene Manager (Motion Industries) had bearings repacked for our facilities and those were named “MGC Specials”. The MGC Specials were then restocked into the maintenance stores as a standard SKU.
Li/M is the Lithium based Thickener, and in comparison the PU/M is the Poly-urea based thickener showing a GLF (Grease Service Factor) significantly higher with an average well above x5.
Cite Paper. The Grease Life Factor concept for ball bearings
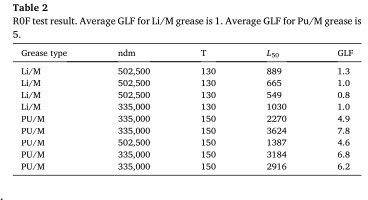
Due to the environmental factors two other initiatives are recommended:
1. Only use 2 RS type shields as Moisture ingress is factor in grease life, with Poly-urea less prone than Lithium thickeners.
2. Use of Stefa Shaft seals on Drive End Bearing.
by Mark Gurney – 3phi-reliability.com (3Phi Reliability distributes & Implements Ultrasonic Lubrication using SDT LUBExpert, SDT340 Detectors and Crysound Acoustic Cameras. )