Acoustic Lubrication is just one of the 8 application pillars adopted by world-class ultrasound programs. And what an important one it is. Poor lubrication practices account for as much as 40% of all premature bearing failures. When ultrasound is utilized to assess lubrication needs and schedule grease replenishment intervals, that number drops below 10%. What would 30% fewer bearing related failures mean for your organization? Keeping up with the changes in on-condition bearing lubrication techniques is challenging. Technology advancements from SDT’s LUBExpert allows us to transform complex processes into simple, 5-step procedure.
How to Get Started
Success is dependent on organization and commitment. Without these two structural elements, your ultrasound lubrication program will find difficulty getting traction. A well-organized strategy and carefully planned execution will get the project started properly. Getting the commitment from all levels becomes much easier when a program can demonstrate structure and cohesion. Results will prove the program faster which will trigger easier access to funding to grow and sustain the program.
Clearly defining and communicating the objectives of your lubrication program is the best way to create a precision lubrication culture that benefits your entire organization.
Start by asking “Why start an ultrasound lubrication program and what improvements do we expect?” There is no one easy answer to the question. Saving money is an obvious benefit that gets the attention of management, but it is not specific enough. How will an ultrasound lubrication program save money?
- By reducing grease consumption;
- By raising awareness of the right types of grease to use;
- By making more effective use of lube tech’s time;
- By reducing unwanted machine breakdowns caused by lubrication failures;
- By extending bearing life expectancy.
A new beginning is the best opportunity to review what you have been doing previously. Identify what worked and improve or remove what did not. We will not go deeply into all aspects related to good lubrication practices. However, there are some basic and relevant points that should be noted.
Lubricant management program:
Keeping your bearings healthy requires a lubricant with the right quality for the application. By quality we refer not only to the quality of the grease manufacturer, but quality in a broader sense which involves all the processes from manufacturing to application. Some general recommendations are:
- Keeping high standards of housekeeping for storage, handling, and application to prevent contamination that degrades the quality of lubricants.
- Keep a detailed list of products to use for each lubrication point. Selecting the right lubricant requires technical knowledge in several aspects. Using the wrong product will jeopardize the useful life of the component. Don’t change lubricants without solid reasons. Consider contracting a lubrication consultant to direct advice on this.
- Provide training in every aspect relevant to lubrication practices and product knowledge to those responsible for lubrication.
- Set objectives to reach so you have a clear path to follow.
Application Guidelines:
Delivering the lubricant to the right point requires some type of device; usually a grease gun. There’s lots of different types but they all have one thing in common: they deliver grease with high pressure, enough to overcome the backpressure in the grease fitting.
Dirty grease and mixing grease types kills bearings. Therefore, it is necessary to extend the precautions for contamination and storage discussed above, to the application of lubricant through grease guns:
- Wherever possible, insist on using a dedicated grease gun for each grease type to avoid the risk of applying the wrong product through cross contamination. Label the grease gun with the associated grease to be used. LUBExpert manages multiple grease guns to prevent mixing of grease types.
- Standardize your grease guns so they all deliver the same quantity of grease per stroke.
- The same principle must be applied for your ultrasound device. If using SDT’s acoustic lubrication adaptor LUBESense1, assign a different one for each grease type. Grease remaining in the adaptor can mix with new grease causing a degrading chemical reaction.
- Always clean the grease fitting and grease gun before and after every application.
- Some bearings have drain plugs for purging old grease. If you open the drain, remember to clean the drain hole; it may be clogged. Use a clean brush like a bottle washing brush to clear the port.
- Apply grease slowly, one full stroke at a time (no more than 20% of the maximum designated quantity per injection) to avoid over greasing. This also avoids potential damage to the bearing as too much pressure can push the bearing cage into the roller elements.
- Always allow for churning time – the time required for freshly injected grease to work its way into the bearing.
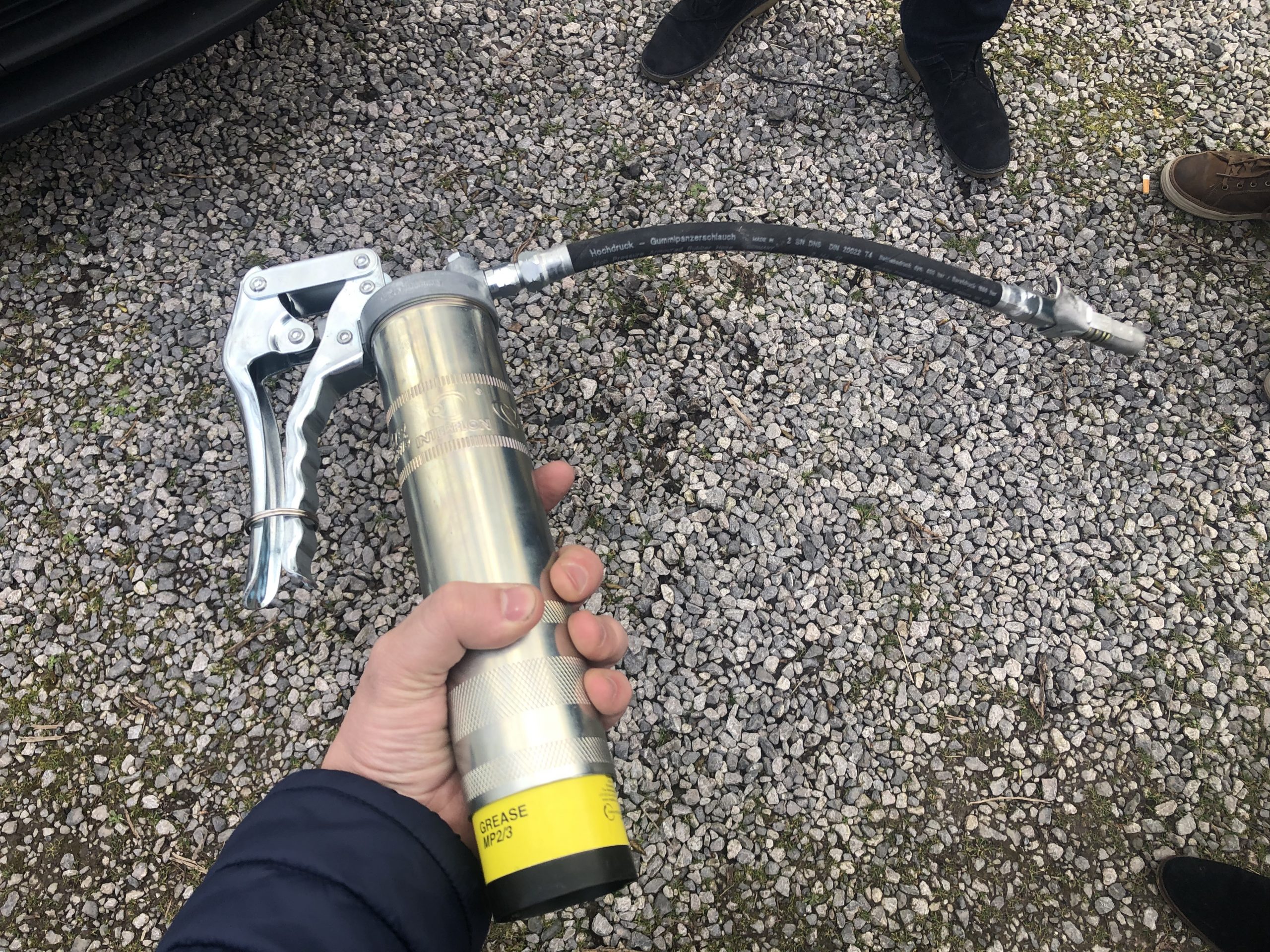
Type of bearing inside:
Don’t assume that a grease fitting installed on a bearing housing means a path to grease the bearing. Sometimes, motors are fitted with both grease fittings AND sealed for life bearings. You must identify every grease point to be managed within the ultrasound program. Identify the bearing inside to know its size for lubrication quantity, its particulars for defect diagnosis, and the type of grease typically used. Here are some helpful tips regarding the use of acoustic lubrication.
- Friction produces ultrasound. Bearing friction is produced by the contact between race, rolling elements and seals or shields.
- Less contacts means less friction. A ball bearing produces less friction than a same size roller bearing under the same lubrication conditions, speed and load.
- Plain bearings produce the lowest friction levels. Their ultrasound baseline often trends in the single digits or low teens. Typically, they remain consistent for their lifespan and only display sudden upward trend lines when the oil film becomes contaminated or the bearing is near failure.
Benefits of Ultrasound
Ultrasound performs well at sensing and measuring changing in friction levels. It’s the perfect technology to guide lube technicians during the lubrication-replenishment task. Ultrasound assisted lubrication of plant assets offers significant benefits that calendar based lubrication cannot. The days of relying on calendars and calculators are over. Use our 5-Step Acoustic Lubrication Procedure and start greasing bearings the right way!