Torki works as a senior lubrication engineer at a cement manufacturer. He recently completed his Live Online Level One Ultrasound Certification with SDT Ultrasound Solutions and has since been applying what he learned during the course to his job as a lubrication engineer.
Torki was kind enough to share this lubrication case study with us. He co-authored it with his co-worker, vibration analyst, Khaled Salman Almarwany.
The initial task was simple. Lubricate the drive-end and non-drive-end bearings of a cooling fan using a LUBExpert Static.
Previously, the lubrication team at this cement manufacturer greased their bearings on a time-based schedule, rather than condition based. The calendar schedule called for 50 grams of grease every two weeks, regardless of the needs of the bearing.
Since switching to the ultrasonic condition-based method for greasing their bearings, Torki and his fellow lubrication technicians noticed a steep decline in grease consumed. Where it used to be 50 grams every two weeks for both the drive-end & non-drive-end bearings, it dropped to 16 grams for the drive-end and 14.4 grams for the non-drive-end during the most recent successful lubrication task, which can be seen in the following two figures.
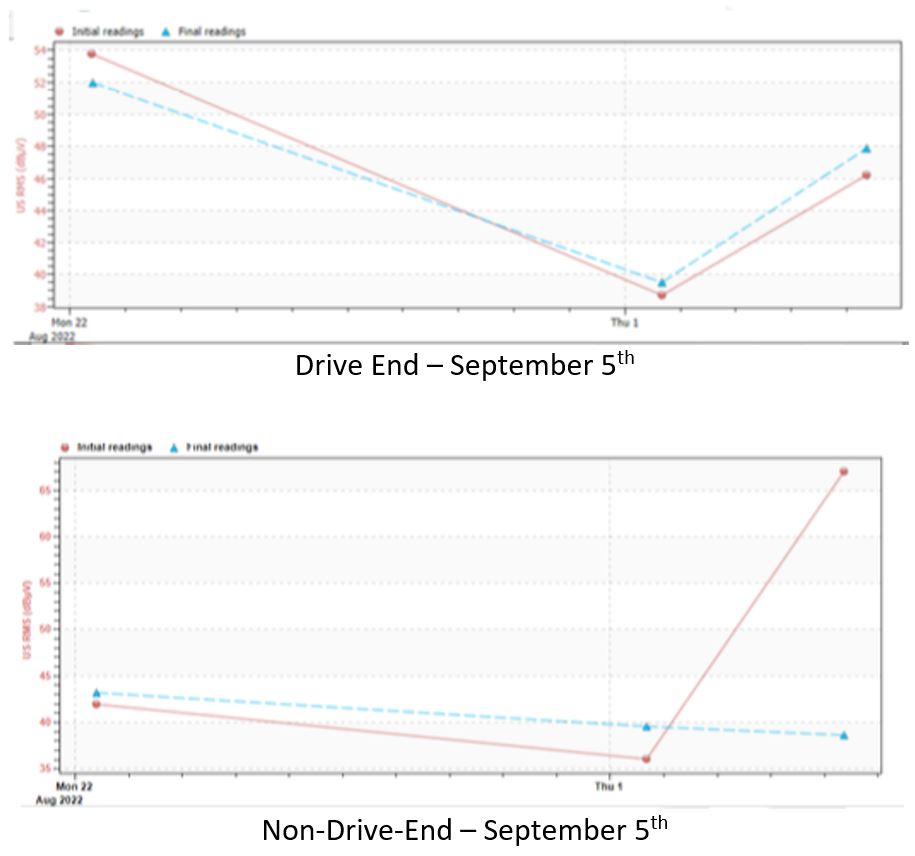
As seen here, lubricating the drive-end bearing increased friction, indicating over-lubrication or a suspected bearing failure. Lubricating the non-drive-end bearing drastically reduced friction, indicating a lubrication success. However, the LUBExpert still issued a suspected bearing failure warning on the non-drive-end bearing. This additional analysis from the LUBExpert was backed up by the vibration analysis performed by Khaled, which indicated mechanical looseness, as seen in the harmonics of the impacts in the vibration spectra below.
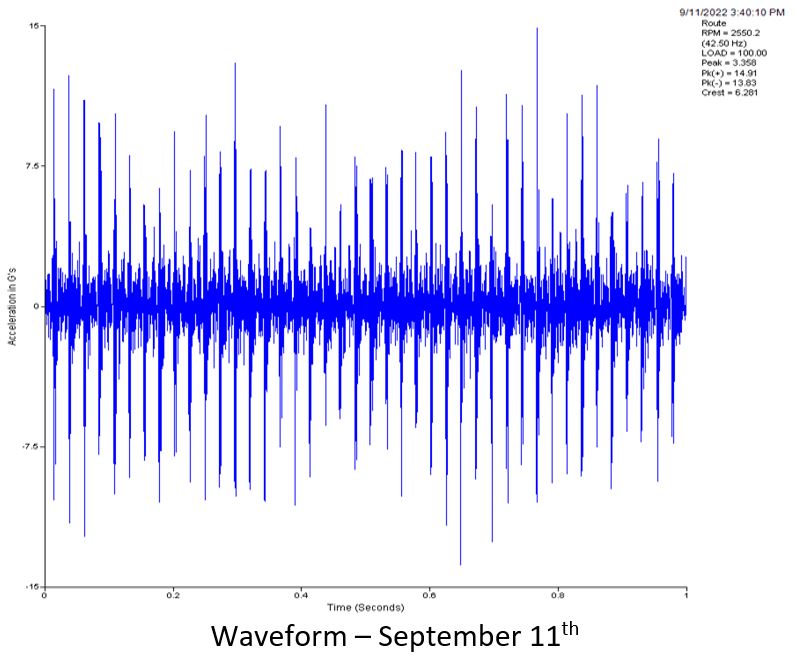
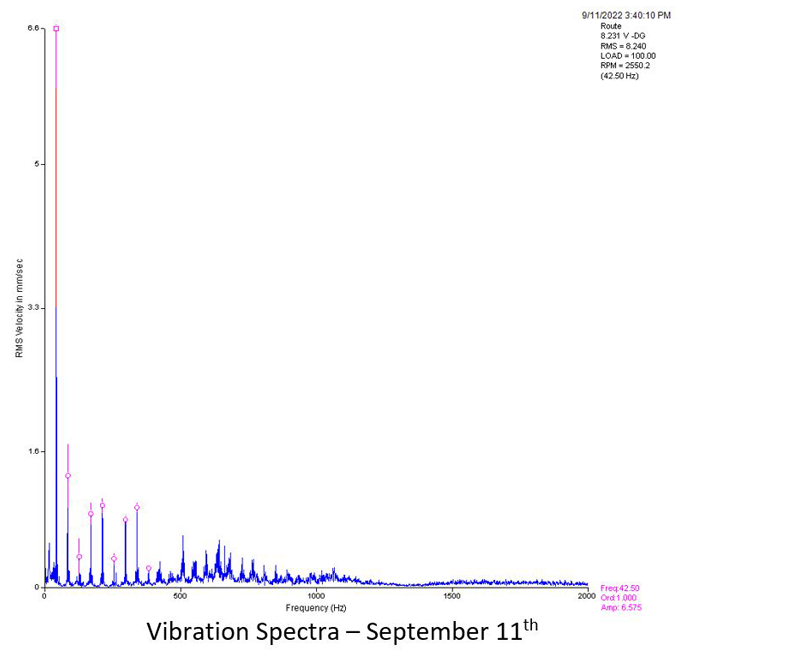
As seen in the vibration data, the bearings were in a failed state due to mechanical looseness and required replacement. They were replaced during the next shutdown, and new vibration measurements were taken on the machine. As seen below, the overall RMS went from 8.2 to 2.7 after the bearings were replaced.
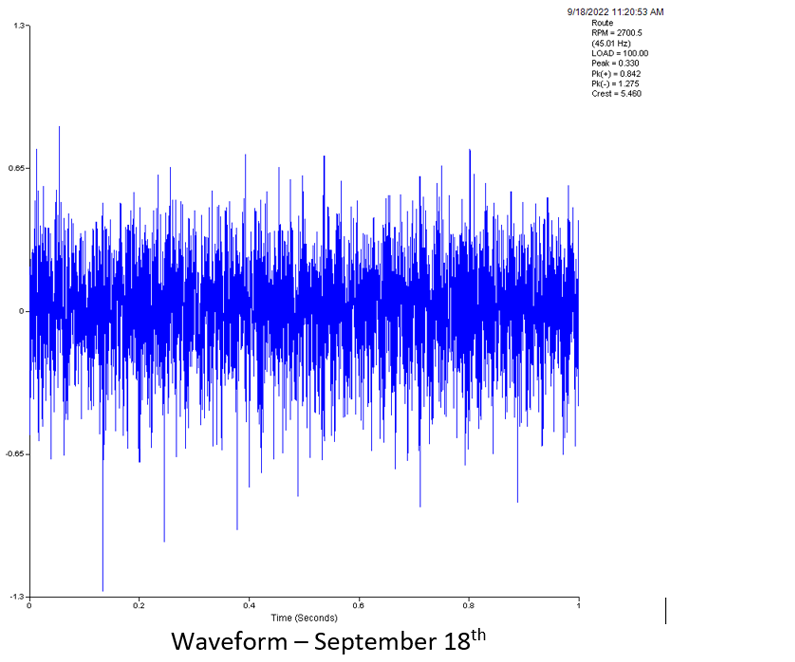

After the bearings were installed on September 18th, they were lubricated successfully 4 days later on the 22nd using the LUBExpert Static. The data can be seen below!
As seen in the vibration data, the bearings were in a failed state due to mechanical looseness and required replacement. They were replaced during the next shutdown, and new vibration measurements were taken on the machine. As seen below, the overall RMS went from 8.2 to 2.7 after the bearings were replaced.
This case demonstrates the effectiveness of combining LUBExpert, and lubrication reliability, with the vibration team, and their mechanical condition monitoring efforts! The lubrication team can communicate their results with the vibration team, and vice versa.
Cross referencing both sets of data leads to a more complete picture of bearing health. It allowed the lubrication and vibration team at this cement manufacturer to replace both compromised bearings before they failed, avoiding unplanned downtime. Both departments were also able to collaborate on the installation of the new bearings, preventing any installation failures.
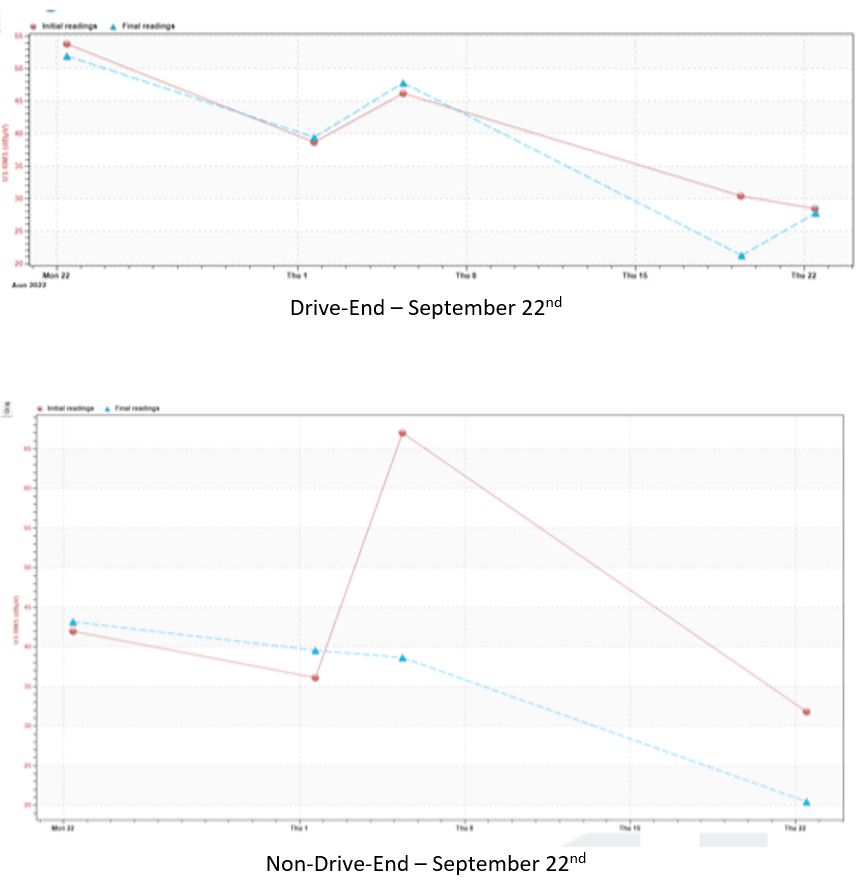