Compressed air is essential to industrial operations, driving pneumatic tools, automation systems, and various processes across many sectors.
Its reliability, ease of use, and adaptability make it the fourth most widely used energy source in industry, following electricity, natural gas, and water. However, producing compressed air is not as efficient as it may seem. In fact, it’s one of the most energy-intensive resources in industrial settings, consuming a significant portion of a facility’s electricity.
The true cost of compressed air
While most industries recognize the value of compressed air, few fully grasp its hidden costs. On average, compressed air accounts for 13% of industrial electricity consumption in countries like France, with similar figures worldwide. But what’s surprising is that more than 90% of the electrical energy used in air compression is lost—primarily in the form of heat—leaving only 8-10% of the energy to perform useful mechanical work. The rest is simply wasted.
For facilities that run compressors 6,000 to 8,000 hours annually, energy consumption can constitute up to 80% of the total cost of compressed air production over five years. When one considers that a cubic meter of compressed air at 7 bar requires 200 Wh to produce, it’s easy to see why inefficiencies like leaks become so expensive.
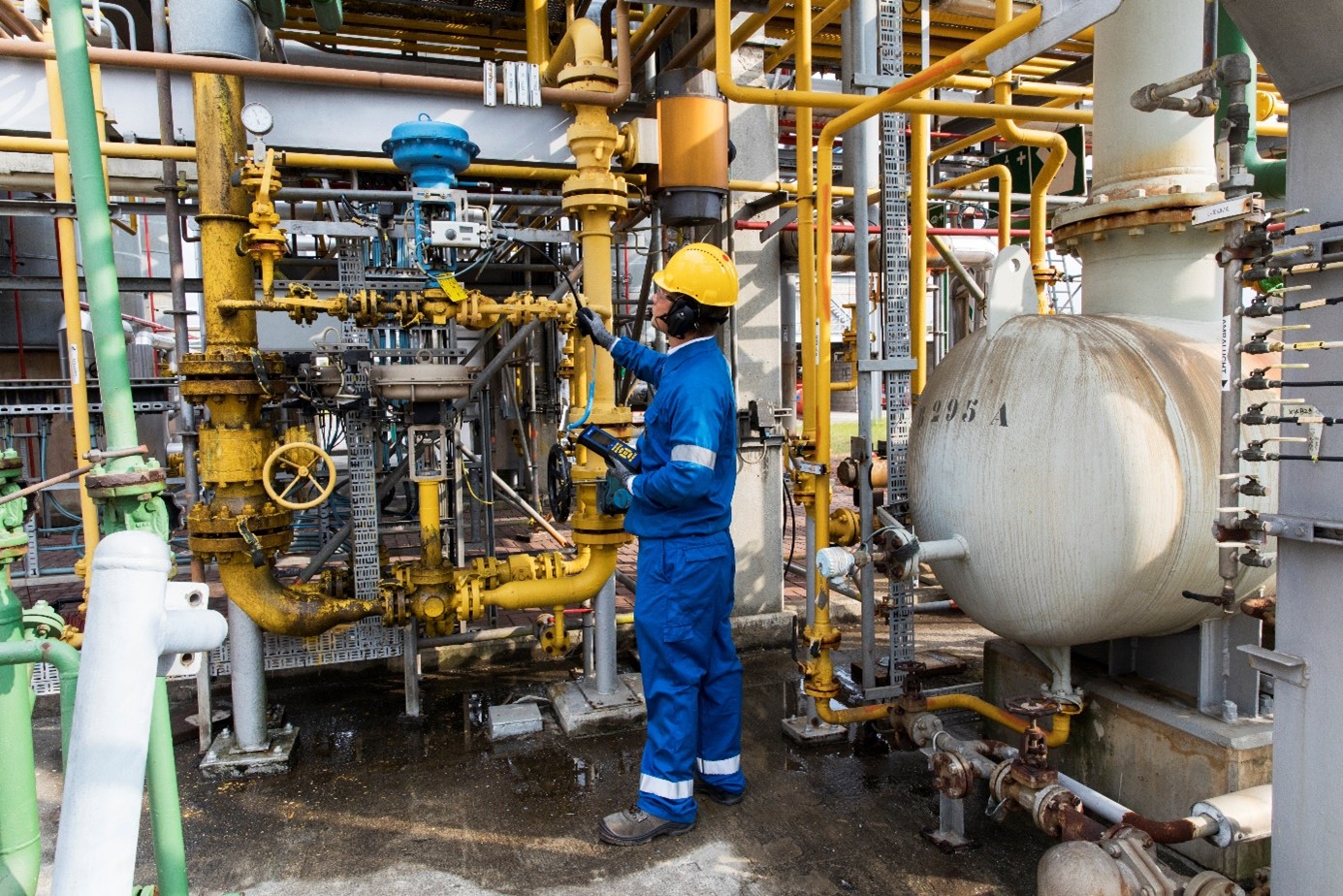
The hidden drain
One of the biggest contributors to this inefficiency is the presence of leaks within the compressed air system. While leaks don’t typically pose safety risks or directly disrupt production, they are a major source of energy waste. On average, 30-40% of compressed air production is lost through leaks. In some cases, this number can be even higher. Globally, the average leakage rate is estimated at 34%. This means that one out of every three compressors in a facility could be working just to supply the air lost through leaks—an unacceptable waste of energy and money.
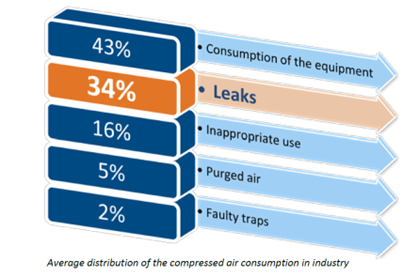
Because leaks are odorless, invisible, and often inaudible in noisy industrial environments, they frequently go unnoticed. But the financial impact of these leaks is significant. Not only do they contribute to skyrocketing energy costs, but they also increase the wear and tear on compressors, leading to more frequent maintenance and shorter equipment lifespans.
SDT340: The solution to compressed air leaks
The SDT340 ultrasound detector is a powerful tool designed to address this costly problem. Using advanced ultrasound technology, the SDT340 allows maintenance teams to detect and locate leaks with precision, even in challenging environments. Here’s how it works:
- Ultrasound detection: Leaks generate ultrasound signals due to the turbulence of air or gas escaping through a small opening. While these signals are beyond the range of human hearing, the SDT340 can detect them and convert them into audible frequencies using heterodyne technology. This makes it possible for technicians to hear and locate leaks that would otherwise go unnoticed.
- User-friendly features: The SDT340 is equipped with an intuitive interface, Bluetooth headphones, and easy-to-navigate software integration with Ultranalysis® Suite 3 (UAS3). This makes it simple to use in the field, providing real-time data and visuals that guide technicians toward the exact location of leaks.
- Pinpoint accuracy: Unlike traditional leak detection methods, such as using soapy water or listening for hissing sounds during production shutdowns, the SDT340 offers precise and efficient detection in live environments. It can identify leaks of all sizes and pressures, ensuring that even the smallest air leaks are located and addressed.
- Versatility: Beyond compressed air, the SDT340 is capable of detecting gas leaks, steam trap issues, and problems in hydraulic and pneumatic systems, making it a versatile tool for any plant’s condition monitoring strategy.
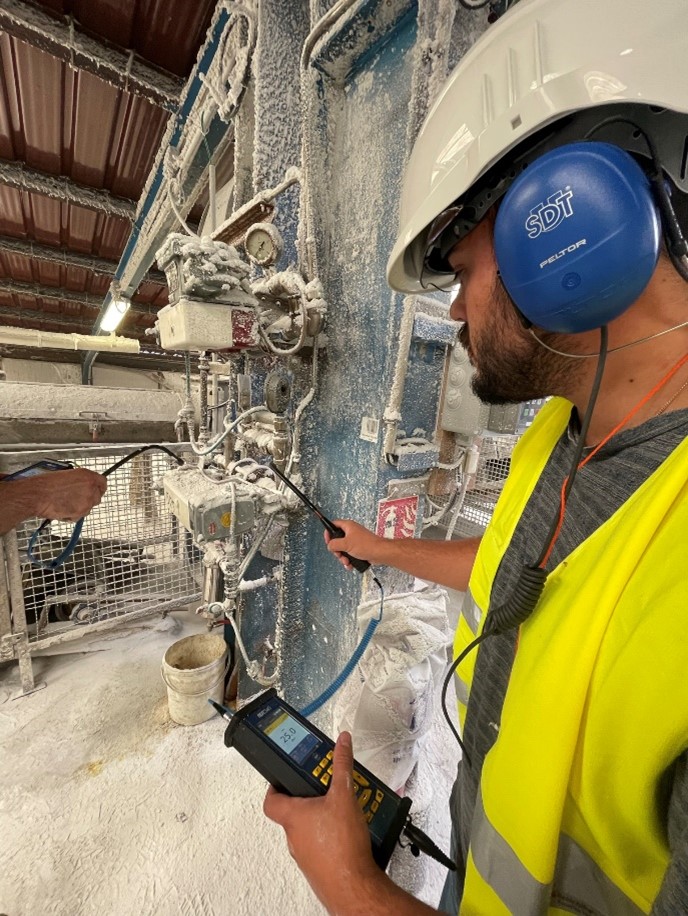
Immediate ROI: Why leak detection is a priority
Identifying and repairing compressed air leaks is one of the most cost-effective strategies for improving energy efficiency in industrial settings. Unlike other optimization measures, such as installing variable speed controls or upgrading equipment, leak detection requires minimal investment and delivers immediate returns.
Training a maintenance team to use the SDT340 takes just a few hours, after which leak detection can be incorporated into regular maintenance routines. The result is often a drastic reduction in energy consumption, with plants saving thousands or even tens of thousands of euros annually by fixing leaks that previously went undetected.
How much can you save?
To put the savings into perspective, consider that the production of a cubic meter of compressed air at 7 bar consumes 200 Wh of electricity. By knowing your plant’s average air consumption, the number of operating hours per year, and the cost per kWh, you can estimate how much energy is wasted through leaks. For example, a facility with high compressed air consumption might discover that it is losing tens of thousands of cubic meters of air annually through leaks—translating to significant energy costs.
Even small leaks can have a major impact. A single 3mm hole in a compressed air pipe can cost a facility more than 1,000€ per year in wasted energy. Multiply that by several leaks across a large system, and the potential savings from detecting and repairing leaks quickly adds up.
The green cherry on top
In addition to the financial benefits of detecting and repairing compressed air and gas leaks, the use of the SDT340 contributes significantly to sustainability efforts. By minimizing energy waste associated with leaks, industries can reduce their carbon footprint and lower greenhouse gas emissions. As compressed air systems are energy-intensive, optimizing their efficiency through ultrasound leak detection not only saves money but also helps facilities achieve greener, more environmentally friendly operations. Implementing proactive maintenance strategies like these plays a vital role in driving long-term sustainability and supporting global efforts to combat climate change.
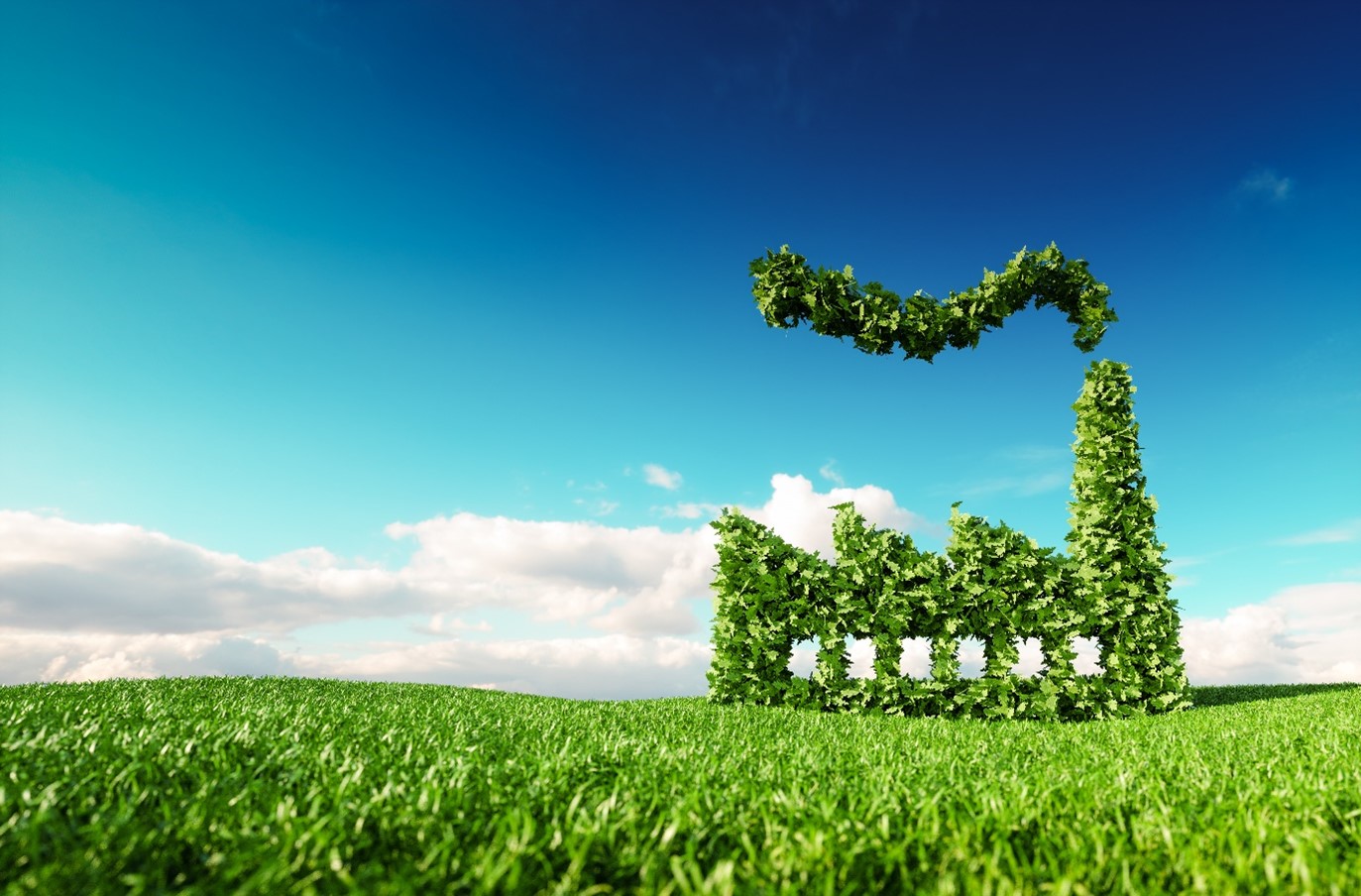
A comprehensive tool for optimizing compressed air systems
Detecting leaks is just one part of optimizing compressed air systems, but it’s a crucial step. In addition to leak detection, the SDT340 offers tools for valve condition monitoring, steam trap testing, and hydraulic system analysis, ensuring that all parts of the system are running efficiently.
Because ultrasound technology is highly effective at detecting fluid turbulence and friction—whether in air, gas, or liquid systems—the SDT340 provides a multi-dimensional solution to maintenance teams. The device’s High Signal Resolution (HSR) feature enhances its sensitivity, making it ideal for identifying even the smallest anomalies in pressurized systems.
An industry standard
Traditional leak detection methods—such as using soapy water—are labor-intensive, time-consuming, and often ineffective in large, complex plants. Ultrasound sensors used with SDT340, however, are recognized as the industry standard for leak detection, delivering fast and reliable results in various settings. Whether you’re inspecting hard-to-reach areas or monitoring large facilities, the SDT340’s rugged design and adaptable sensors make it the go-to solution for leak detection.
Start saving with the SDT340 today
Compressed air is a valuable resource, but its energy-intensive production makes leaks an unacceptable waste. With the SDT340 ultrasound detector, detecting and fixing leaks has never been easier or more efficient. By incorporating leak detection into your regular maintenance routine, you can drastically reduce energy waste, improve system efficiency, and extend the life of your equipment.