The founding principle of predictive maintenance could be “better safe than sorry”. It requires sound knowledge of the machines, taking into account of early signs and economic realism.
Today, predictive maintenance is based on different technologies that maintenance departments can use to assess failure risks, frequency ratio and severity level.
But it’s another matter when it comes to selecting the right analysis tools, the right technology and the right indicators for the early detection of a failure on a rotating machine, in particular low-speed machines. Ultrasonic technology is used to issue this diagnosis, as it can be easily and efficiently implemented.
Recently, SDT International took up this challenge on a rotating machine with a rotation speed of 8 RPM.
More than a week earlier, the maintenance department of a world-renowned company had detected unusual noise on a strategic production asset. The sudden stop of this machine would have led to the complete shutdown of the production site. Not to mention the financial cost of replacing these 4 bearings, the time required for the procurement of these specific bearings and the cost of the maintenance labour.
There was a dual stake here: control the condition of these bearings and attempt to detect the origin of this noise.
A diagnosis could be issued using the new ultrasonic measuring instrument, SDT340, and its FOCUS mode that can generate sampling frequencies up to 256 K samples per second.
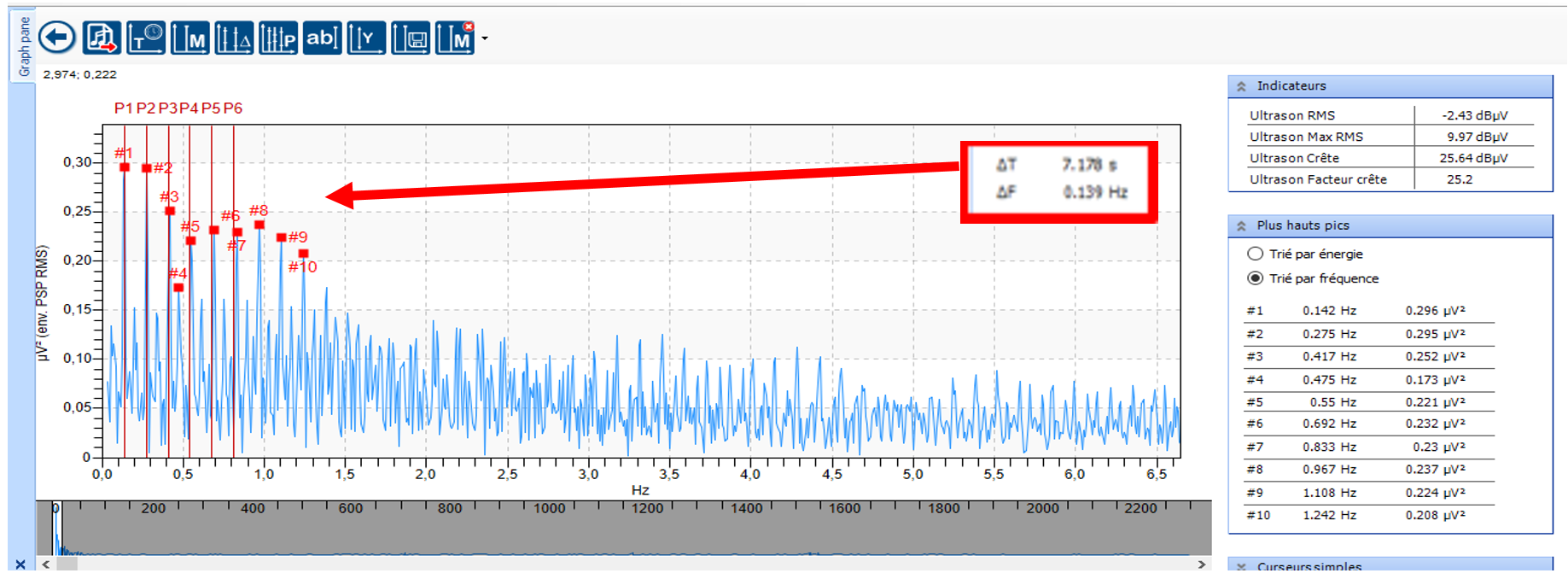
The spectrum shows an impact at the rotation speed (0.139 Hz) of the shafts of the rotating machine, along with its harmonics. Sub-harmonic frequencies can also be observed at 0.5 x the rotation speed, which is a characteristic spectrum for a rotational clearance due to friction or significant impacts. No impact due to bearing frequencies are observed. Our diagnosis is confirmed by the time spectrum.
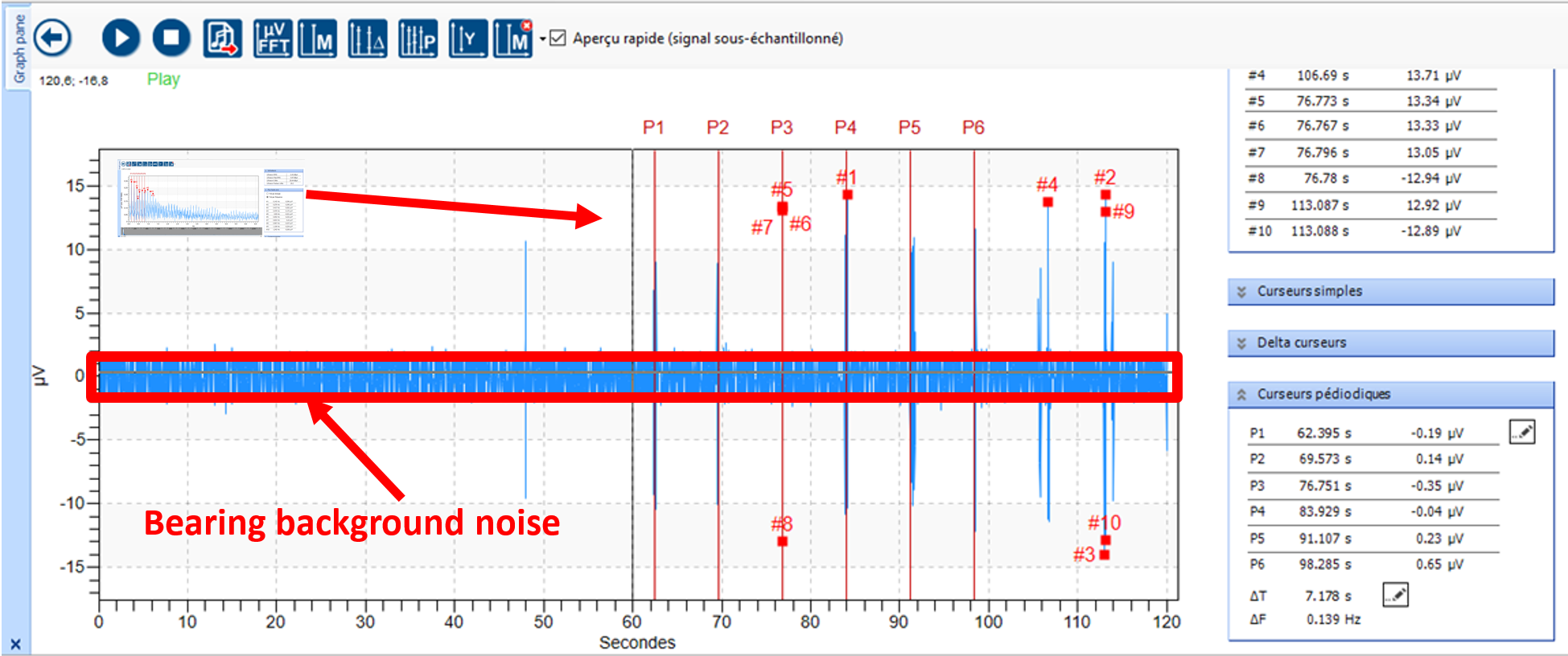
The time spectrum shows that the observed impacts are indeed associated with the rotation speed of the shafts of the machine at 0.139 Hz, i.e., a rotation speed of 8.34 RPM.
In terms of energy, these impacts are not necessarily constant for each shaft revolution (time signal recorded over a period of 2 minutes).
The encountered problem is due to the wear of the shafts and of the disks that are mounted onto these shafts and generate friction.
Now, the maintenance department knows the origin of the noise and the condition of the bearings, which just need to be monitored on a periodic basis.