It is an understatement to say that the fight against climate change and the various regulations that follow should encourage manufacturers to significantly reduce their energy consumption.
Is it difficult? No, gains can be generated in the improvement of a building itself, in utilities such as air conditioning, heating and lighting, but also – and this is our topic today – in the manufacturing process.
In 2014, the Belgian industry accounted for 47% of the country’s electricity consumption[1]. In this respect, it has a vast potential for savings, synonymous with productivity gains, and, therefore, improved competitiveness. According to a French study by the Centre d’Etudes et de Recherches Economiques sur l’Energie, 43% of transverse consumption (motors, compressed air, etc.) could be avoided, and half of this could be done with overinvestment that would be amortized in less than three years. Considerable gains are, consequently, still possible.
The objective of the ISO 50001 standard on energy management is to enable companies to achieve, through a methodical approach, the continuous improvement of their energy performance, which includes efficiency, use and energy consumption. This improvement process saves money and increases your company’s productivity while reducing its impact on the environment. When the commitment is made and the objectives are set at the management level, user-friendly and directly profitable methods are at hand.
Ultrasonic measurement and cost reduction
Ultrasonic measurement for the maintenance of production equipment allows a wide range of precise controls in many applications to detect incipient mechanical, hydraulic and electrical defects. It also shows its effectiveness in locating internal leakage defects on steam traps and valves. It is important to keep in mind that any equipment that does not function in its ideal operating conditions generates avoidable costs and energy overconsumption. We are, therefore, in the field of cost reduction and, so, improvement of competitiveness: firstly, by the strong reduction of the maintenance costs of the tool, by the application of preventive actions, and thirdly, by substantial reductions in energy consumption.
The best ultrasonic measuring devices and their associated sensors constitute a user-friendly and versatile solution for maintenance rounds. The TRAPChecker is an affordable solution that perfectly corresponds to these characteristics. It is the ideal answer to the current needs of maintainers who are aiming for a real improvement in profitability, in conjunction with their financial managers; easy-to-use instruments and software for those who want it and more advanced for those who need it.
30% of steam traps fail and cause a lot of damage and energy waste
Failed traps create huge energy wastes. Steam is an expensive energetic fluid, and given its high production cost, a steam trap monitoring program will result in significant energy savings. In addition, their malfunctioning and the breakdowns that result in failed traps can have serious consequences on production and logistics. Consequences that competitive objectives no longer allow! A predictive maintenance program for production facilities is therefore a decisive and strategic priority. How many traps do you have? Without regular inspections, there is a good chance that up to a third of them will be defective!

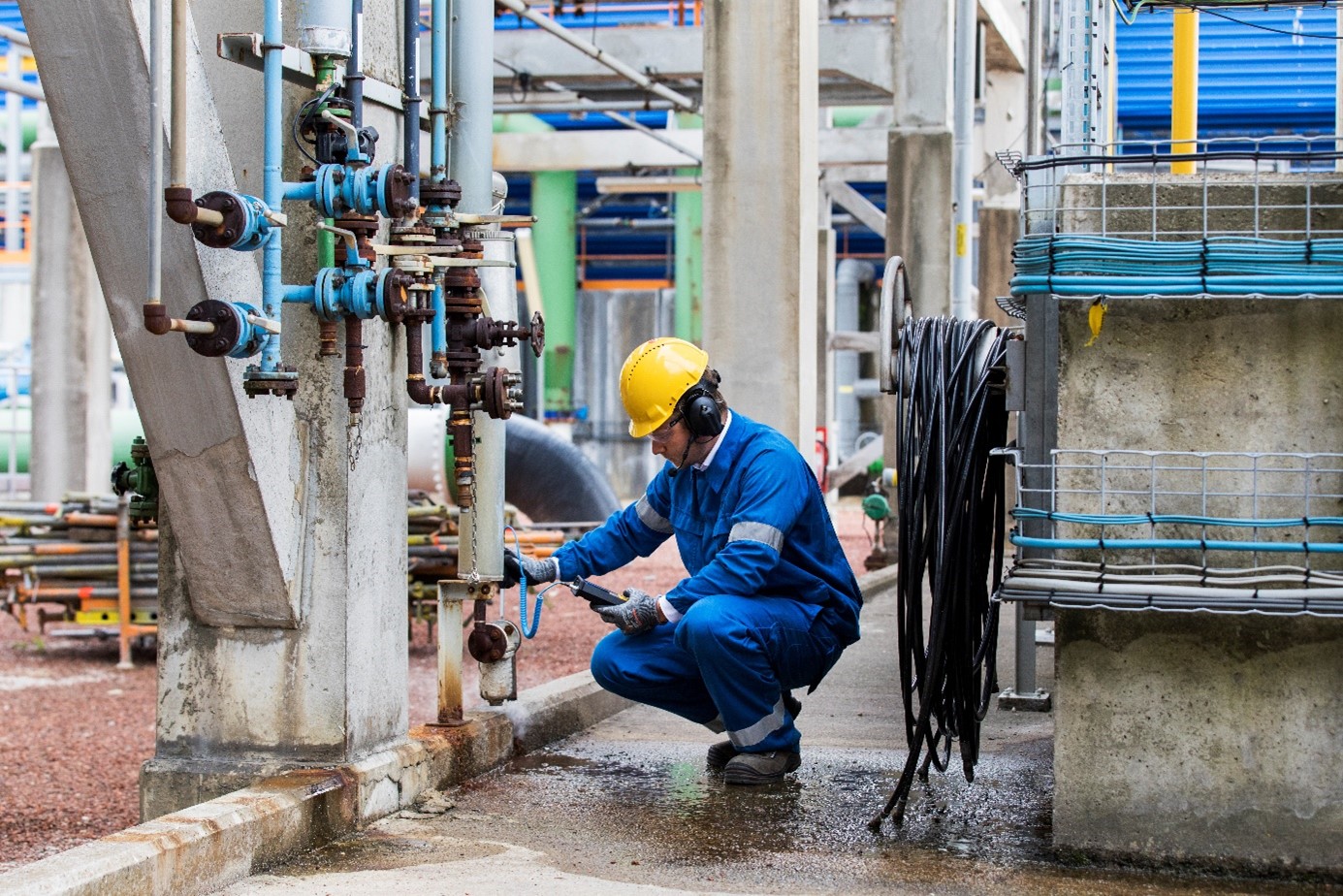
The commitment to optimize energy consumption responds to a triple concern that goes far beyond compliance with the 50001 standard. Just consider the recurring increase in energy prices, the depletion of raw materials and the global warming due to CO2 emissions to convince us of this.
Some companies decide to implement the standard, simply for the direct benefits it provides, and they are significant. Others choose certification to prove to third parties that they are implementing an energy management system, and this helps their image.
Apart from steam trap monitoring, the potential for continuous improvement of energy performance in the industrial process is much greater than you might think.
[1] Evolution of final electricity consumption by sector of activity. Source Eurostat 1990-2014 and Synergrid 2015; APERe graph.