The insides of a bearing consist of four important components. The inner and outer raceways form a path for the rolling elements to glide on a thin film of lubricant. A metal cage separates the rolling
elements, keeping them evenly spaced to distribute the load and stop them from crashing into one another. These four components move in concert, producing frictional forces from rotational inertia, surface load, misalignment, imbalance, and defects. Zero friction is impossible, but optimal levels of friction are achievable with correct installation techniques and the proper amounts of lubricant.
Determining optimal friction is best done with an ultrasound condition monitoring (CM) program. Ultrasound detectors measure Friction and Impacting as acoustic energy from rolling friction and defect impulses. When lubricant levels are optimum, the energy created is at its lowest. As frictional forces increase, so does the acoustic energy.
Use ultrasound to sort bearings with high levels of friction from those with normal levels. Establish trends from ultrasound measurements.

Figure 1 - Basic Bearing Anatomy
Frequency
How often should machines be greased? There is no single answer and there are as many possibilities as there are philosophies. In a program that adopts ultrasound condition-based lubrication replenishment, we can approach this with simple logic:
Q: Why do bearings need grease?
A: To reduce the frictional forces between the surfaces of the bearing’s rolling elements.
Q: Ok, so when does new grease need to be added to a bearing?
A: When the bearing’s frictional forces increase beyond a set quantifiable level.
Q: What is a reliable and easy to use technology that determines changes in frictional forces?
A: Ultrasound
Back to the original question then, “how often should grease be replenished?” First, it is important to remember that a 6 dBµV increase represents a doubling of the ultrasonic amplitude. Considering this, a reasonable approach is to state “whenever the ultrasonic measurement indicates an increase of 8-10 dBµV over the previous reading or other reference value, a safe point for establishing lubrication interval alarms for condition-based monitoring is reached.”
With recent improvements in technology and software, such as the LUBExpert’s Onboard Ultrasound Assistant’s algorithm developed by SDT, ultrasonic equipment can now detect more subtle changes in asset conditions and provide guidance to lube technicians. This allows for fine tuning of critical assets, as well as confirming judgments made by lubrication technicians.
When in the field, a lubrication technician may not have historical information for each specific bearing, but he still has a job to do. An increase of as little as 2 dBµV, after the initial addition of a small amount of lubricant, can indicate that a bearing is already over lubricated. Similarly, a decrease of a few decibels can indicate that the bearing is under lubricated and needs additional greasing.
Another improvement is the identification of bearing defects. For example, after introducing lubricant to a bearing, one should allow a delay before taking another ultrasound measurement. This is called the “Churning Phase” and it allows time for new lubricant to work its way into the bearing. The duration for the Churning Phase varies with the size and RPM of the bearing. An increase in the decibel levels between the time you first add grease and the end of the churning phase may indicate a bearing defect. Alternatively, it could indicate that the bearing is over-greased.
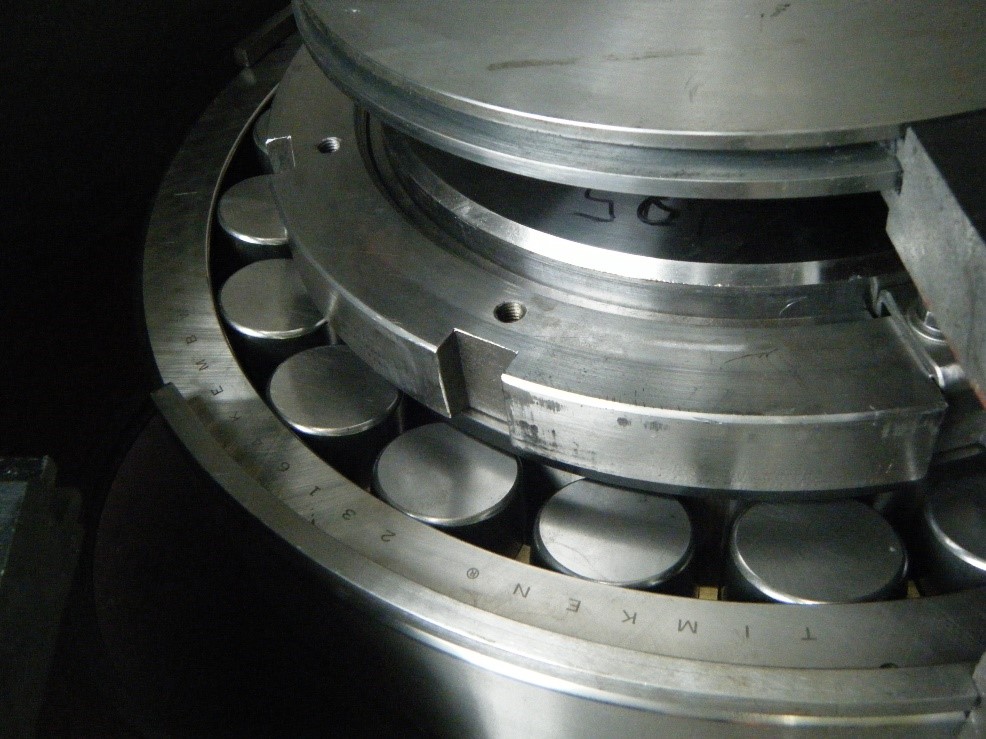
Reporting
The objective of good reporting is to provide information and build awareness to those who need to be informed. They need to know what work they must do to bring an asset back to best condition. They need to know when that work should be done and the consequences of not acting on the work in a timely fashion. The job of the report generator can be compared to that of a translator. This job normally falls on the person responsible for collecting condition-monitoring data. CM data is the
machine, the valve, the pump, the motor, the “whatever it may be” talking to you in an ultrasonic language. You are trained to understand that language. It is your job to translate what the asset is telling you into meaningful information that the planner, the repair crew, production and management can understand. That is what a good report should be; a product of considered engineering opinion based upon the facts you have gathered.
A report should NOT be data spewing. Time signals and spectra are merely hieroglyphics to most and while they may look pretty to techies, they will not impress upper management. Should they be included? Absolutely. But only include illustrations that support a clear explanation of the problem. Indeed, using the graphics in the example above, including explanations and best recommendations form the essence of any good report.
What message should you be conveying then? Your report should start by stating the problem: “There is an issue with this machine, or this valve, or this bushing, or this transformer. Additional follow-up with vibration analysis and an oil lab report is recommended to confirm the problem.” Identify the asset and the issue. Then clearly state what needs to be done to bring it back to best acceptable condition. A good report should also include a message about the consequence of doing nothing: “You can fix it now and the cost for the repair, including spares, labor and scheduled downtime, will be $500. Or you can leave it alone. However, besides continuing to impact production and product quality, the cost to fix it on an emergency basis will be $50,000.”
What is wrong with writing a strong messaged opinion such as this in your report? Is it politically incorrect to make that assertion and state the blindingly obvious? Or is there lingering fear of making a bad call. The latter is a confidence issue that relates either to distrust in the technology used for CM or the person charged with collecting the data. Both can be addressed through expert training.