This is a Hydro-Cyclone. It separates things. Solids from liquids, solids from solids, or even liquids from gases. The principle is simple enough. A slurry enters the inlet pipe.
Centrifugal force pulls large stuff to the sides and gravity lets them fall through the exit pipe. The vortex in the middle lifts smaller, lighter stuff through the top exit pipe.
Mines use hydro-cyclones in nests to separate sand particles from liquids in a slurry. If the sand particles become too large the cyclone clogs. A clogged cyclone is a safety risk, and results in asset damage and lost production.
The major components of each centrifuge within the nest can be seen depicted in Figure 1. Key components include:
- Feed Inlet (Where the slurry of pulp enters the centrifuge)
- Fluted Vortex Finder (Where the vortex occurs)
- Apex Nozzle (Where concentrated solids exit the vortex)
- Overflow (Where diluted solids exit the vortex)
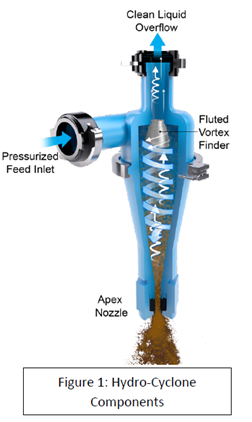
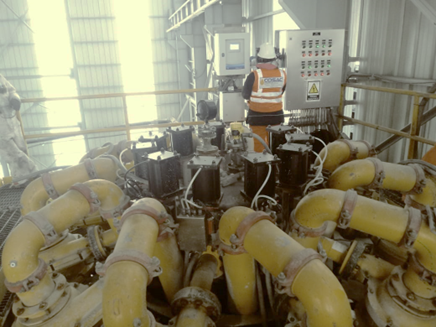
The Antapaccay Mine in Peru uses a group of 6 Centrifuge Hydro-Cyclones as part of their mineral separation process.
When hydro-cyclones are grouped together like this, they are called nests. A consistent reliability issue Antapaccay Mine faces with their nests is sanding and blockages leading to excessive wear on the centrifuges & their components, as well as stoppages to production.
Sanding is caused by the increased size of granular particles. Blockages occur when particle size increases even further. This can lead to pressure spikes which can lead to safety concerns for operators, loss of production and equipment damage.
Detect “sanding” and “blockages” in hydro-cyclones. Determining wear of internal rubber coatings on exit pipe.
A Permanent Monitoring Solution to Prevent Sanding & Blockages
The Vigilant System from SDT Ultrasound Solutions is a multi-channel online condition monitoring solution that combines ultrasound and vibration sensors for permanent monitoring of critical assets. The Vigilant answers the necessary demand to have advanced warning of critical asset failure in remote, or hard/dangerous to access areas.
The Vigilant is designed to provide reliability teams with continuous feedback about the health of their factory’s most critical assets. It combines data from the two most relevant asset condition monitoring disciplines (Ultrasound & Vibration) to provide advanced insight about potential machine failures.
Mineral Separation Process & Inspection
The process begins when pulp enters through the feed inlet. The cycloning then begins taking place in the feed chamber. The heavier particles move to the outer walls, and the apex. This is known as underflow. The lighter particles stay near the center of the cone and are carried by the vortex, which is called overflow.
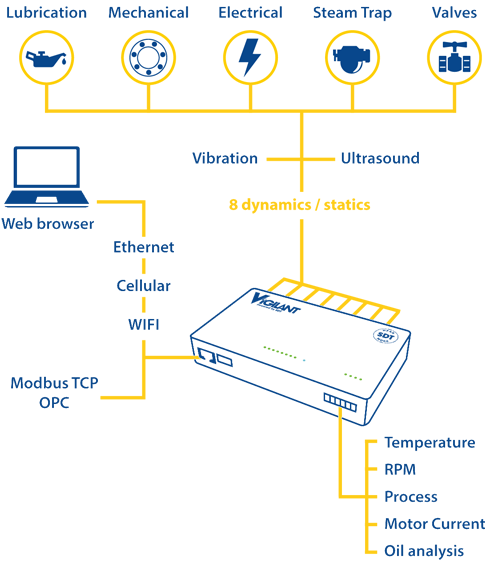
The process begins when pulp enters through the feed inlet. The cycloning then begins taking place in the feed chamber. The heavier particles move to the outer walls, and the apex. This is known as underflow. The lighter particles stay near the center of the cone and are carried by the vortex, which is called overflow.
The inspection process for this reliability issue was very simple with the help of a permanent monitoring system. SDT techs first attached a RS2T sensor to each of the 6 hydro-cyclones. We then used the ultrasonic signals produced during the cycloning process to determine if one of the following was occurring:
• Small particles (normal condition)
• Large particles (sanding condition)
• Without Flow (clogging condition)
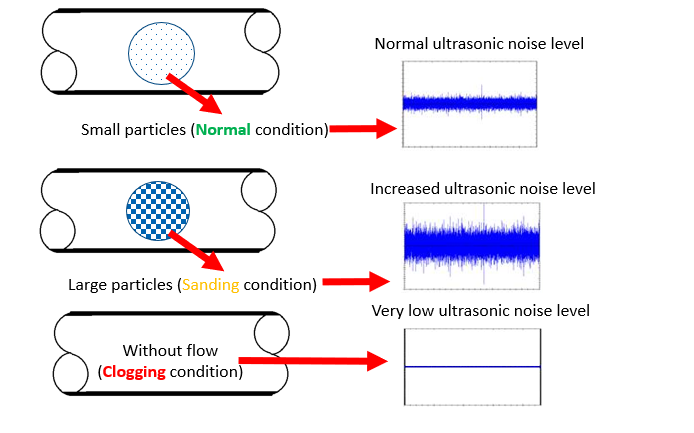
Figure 2: Normal, Sanding, Clogging Condition & their Ultrasound Signals
These can be further illustrated in Figure 2.
Ultrasound is easily able to identify these failure modes as friction & impacting can be monitored closely and trended with SDT’s resonant sensors and advanced software.
Even when the hydro-cyclones are functioning as they should, there is lots of ultrasound produced from friction between minerals & against pipe walls. These ultrasound levels just increase when there is sanding occurring.
We conducted preliminary tests to ensure the installation & permanent monitoring would work. The results can be seen in Figure 3 below.
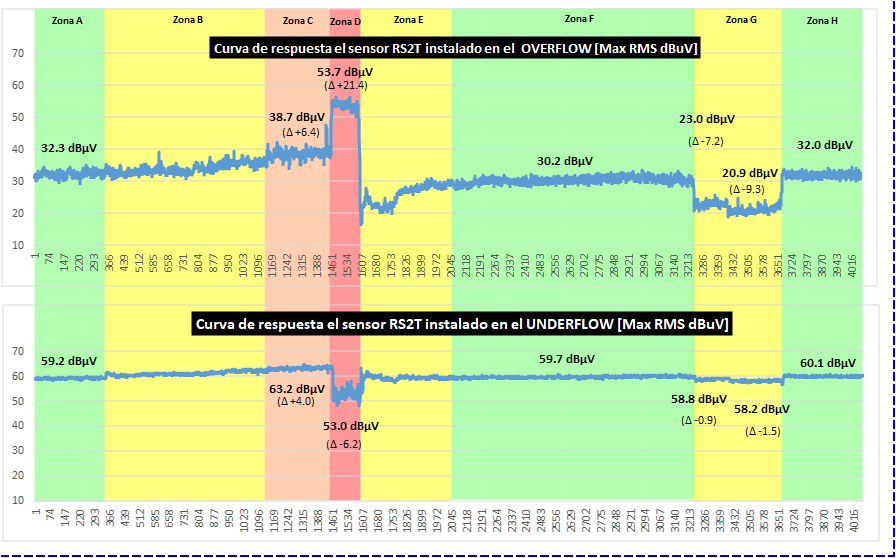
Figure 3: Preliminary Test Data
We tested our sensors & permanent condition monitoring solution against the different granularities of minerals that would most likely be passing through this hydro-cyclone.
- Zone A indicates normal condition
- Zone B, C, D indicates sanding as it is intentionally induced gradually
- Between Zone D & E – Clogging occurred, the Emergency Stop was triggered
- Zone E – Process was restarted after the clog was removed
- Zone F – Normalized operation was achieved again
- Zone G – Flow was intentionally decreased
- Zone H – Normalized Operation was achieved again
In conclusion, we were able to determine that ultrasound was able to detect both sanding and clogging conditions in this mine’s hydro-cyclone nests. We were able to determine whether or not the hydro cyclones were functioning as they should non-invasively. Installation was not difficult and monitoring the asset from the maintenance and reliability control room proved easy with the Vigilant’s ability to relay condition monitoring through ethernet or cellular networks.