It is becoming more and more recognized and accepted among industrialists that lubrication is a cornerstone of reliable operations. Yet, understanding the intricacies of why and how to lubricate remains a challenge for many. The question “Why lubricate?” might seem simple, but the answers vary and reveal the complexity behind this essential practice.
Why do we lubricate?
When asked why lubrication is necessary, common responses include “to fight friction” and “to reduce heat.” While these answers are accurate, they only scratch the surface. The primary reason to lubricate is to create a separation between moving surfaces, preventing direct contact that leads to wear and failure. This principle applies not just to motor bearings, but to pistons, chains, gears, and linear bearings. Proper lubrication ensures these surfaces remain separated, reducing friction, wear, heat, and energy consumption.
Lubricants, particularly greases, also offer additional benefits such as corrosion control. Additives in grease can prevent rust and shield moving parts from contaminants, provided the grease is applied and stored correctly. Despite the evolving science of lubrication over millennia, the fundamental goal remains the same: maintaining separation to prolong asset reliability.
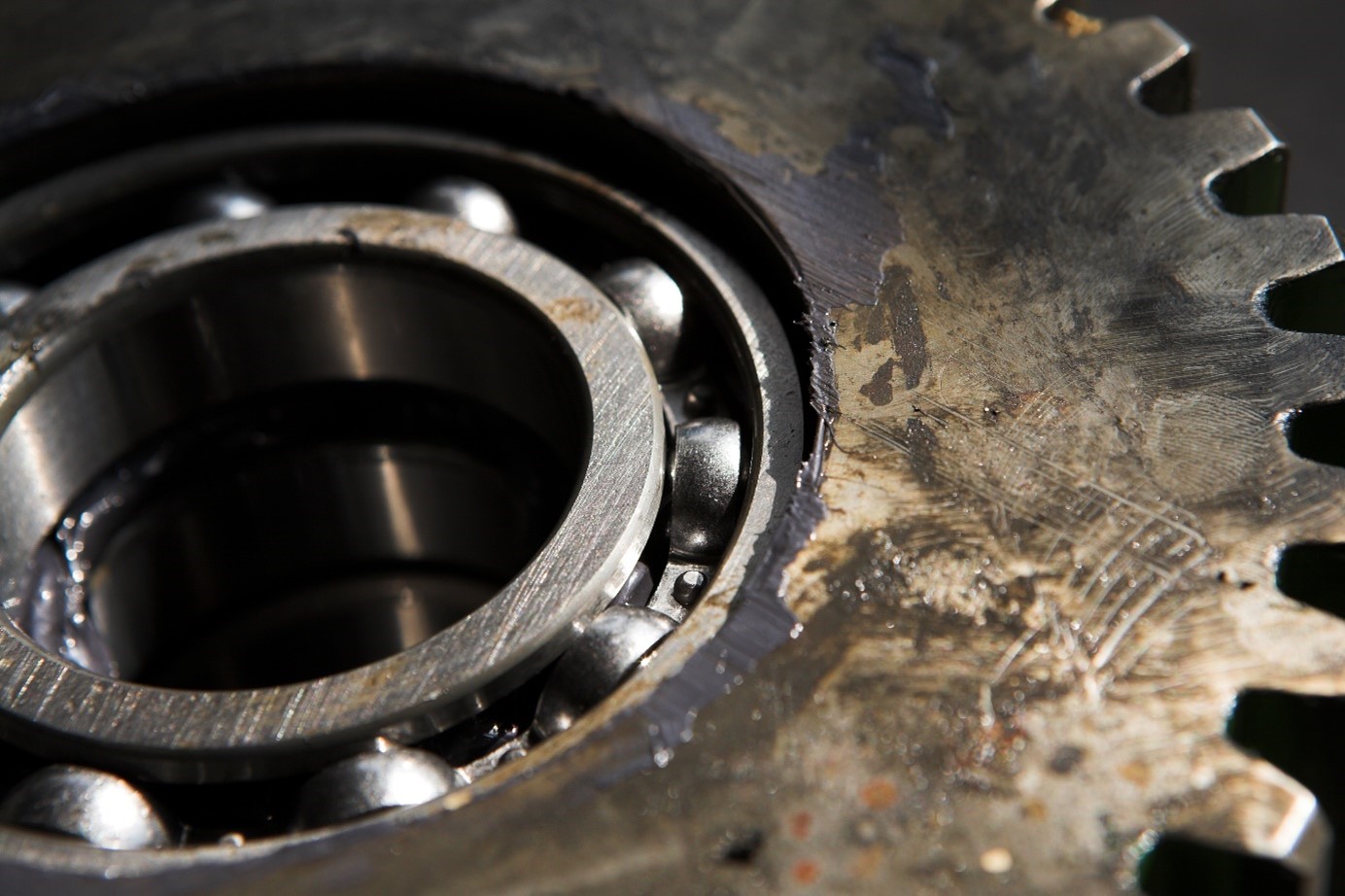
Understanding grease and its properties
The science behind grease formulations is intricate, tailored to various applications. Grease is composed of base oil, thickener, and additives. The base oil forms the hydrodynamic film that separates metal components, ensuring functional separation. Thickeners hold the base oil in place, allowing grease to be effective in any machine orientation, while additives enhance lubricity, fight oxidation, and handle extreme pressures. However, additives degrade over time, making precise lubrication intervals crucial.
Debunking greasing myths
Misunderstandings about grease often lead to poor practices. Over-greasing is a common mistake, causing increased friction and heat, while under-greasing fails to protect components adequately. Contrary to some beliefs, more grease does not equate to better cooling. Bearings need air space to dissipate heat. Moreover, not all bearings with grease nipples require greasing; some are designed to be “sealed for life.”
Effective lubrication requires a balanced approach, not an excess of grease. Over-greasing can force thickener into the “war zone” of bearings, leading to premature lubricant degradation and altered viscosity. The goal is to transition bearings from the churning phase, where thickener is present, to the bleeding phase, where only the base oil lubricates contact points, minimizing friction and wear.
The LUBExpert connection
LUBExpert’s sophisticated ultrasound technology monitors friction levels, providing precise guidance during the lubrication process. This ensures that bearings receive the exact amount of grease needed at the right intervals, eliminating the guesswork that often leads to over or under lubrication. By monitoring the condition of bearings, LUBExpert helps prevent premature failures and extends the lifespan of critical assets.
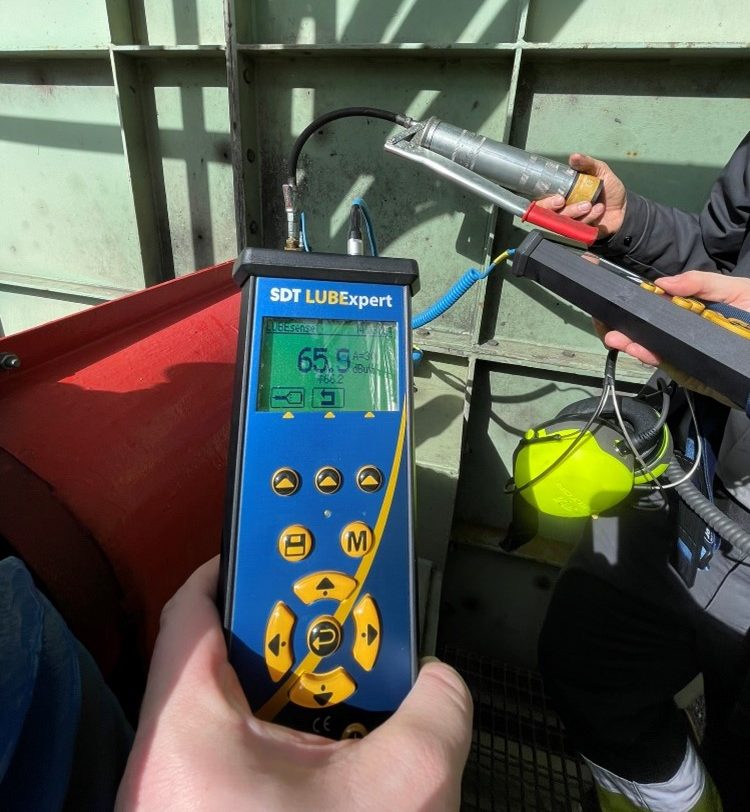
Features and Benefits of LUBExpert:
- Bearing Database: LUBExpert maintains a comprehensive database of all your assets, including bearing types and dimensions. This allows for tailored lubrication strategies for each asset, ensuring optimal performance and longevity.
- Automation: The system automates the calculation of stabilization time between grease pumps, removing guesswork and ensuring consistency in lubrication practices.
- Guided and Free Modes: Whether your lubrication program is well-established or just beginning, LUBExpert offers both guided and free modes to suit your needs. The guided mode provides step-by-step instructions, while the free mode allows experienced technicians to operate with more flexibility.
- Shopping List and Work Orders: LUBExpert simplifies daily tasks by generating shopping lists for the right grease type and quantity needed. It also creates work orders, reminding technicians which bearings need lubrication, thus restoring order and discipline to your maintenance schedule.
- System Messaging: The system documents and communicates reasons for skipped assets, ensuring transparency and continuous improvement in lubrication practices.
- Dynamic Option: LUBExpert’s dynamic option connects the lubrication team with the condition monitoring team. This integration allows for the collection and analysis of dynamic data, bridging information gaps and enhancing overall asset management.
On the path to proper lubrication
By adopting LUBExpert, organizations can transition from reactive, time-based lubrication practices to proactive, condition-based strategies. This shift not only reduces the risk of bearing failures but also optimizes energy consumption and operational efficiency.
Training and proper tool usage are critical to achieving lubrication excellence. LUBExpert empowers lubrication technicians with the data and guidance needed to perform their tasks with precision, transforming them into true LUBExperts.
Lubrication is more than just adding grease to moving parts. It’s about understanding the science behind it and applying that knowledge to achieve optimal performance. With LUBExpert, you can elevate your lubrication practices, ensuring that your assets operate smoothly and reliably.