Our client, a utility company operating in Europe was looking for a reliable method for the inspection of their high-voltage electrical assets under management. They recognize that total electrical systems failures are often 10 times more expensive than planned maintenance. Not to mention all the potential safety risks associated with a run-to-failure strategy with electrical assets.
Ultrasound is an effective way to pinpoint common electrical system defects such as arcing, tracking, partial discharge, and corona.
Arcing: Arcing occurs when electricity jumps between two conductors, creating a visible or invisible arc. Ultrasound can detect the high-frequency noise generated by arcing, helping technicians locate the source of the problem.
Tracking: Tracking is the formation of a conductive path on the surface of an insulating material, typically due to electrical breakdown. Ultrasound can detect the corona discharge and tracking sounds, allowing technicians to identify and repair damaged components.
Partial Discharge: Partial discharge is a localized breakdown of insulation that can lead to equipment failure. Ultrasound can detect the high-frequency noise produced by partial discharge, helping technicians identify areas of concern before a major failure occurs.
Corona: Corona discharge is a type of partial discharge that occurs in high-voltage systems, often leading to equipment degradation. Ultrasound can detect the ultrasonic signals produced by corona discharge, aiding in the early detection of potential issues.
The SDT340, UAS3, & Flexible Wand
By implementing an ultrasound-based inspection program using the SDT340 ultrasound data collector with a Flexible Sensor attachment, maintenance technicians can perform a wide range of inspections and checks on electrical systems, and equipment components utilizing airborne ultrasound.
Typically, inspections of electrical assets such as this transformer consist of scanning around air gaps in the paneling or vents. Circled in Figure 1 is where the inspectors found the defect. We’re listening for distinct buzzing noises. Pristine electrical equipment is silent. Further analysis can be performed in UAS3.
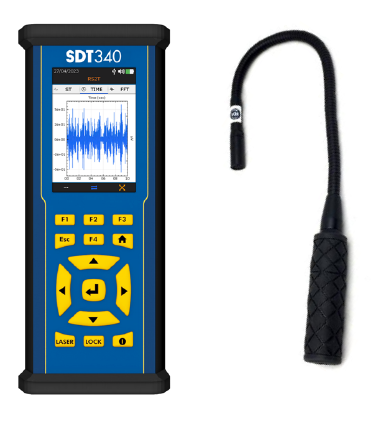
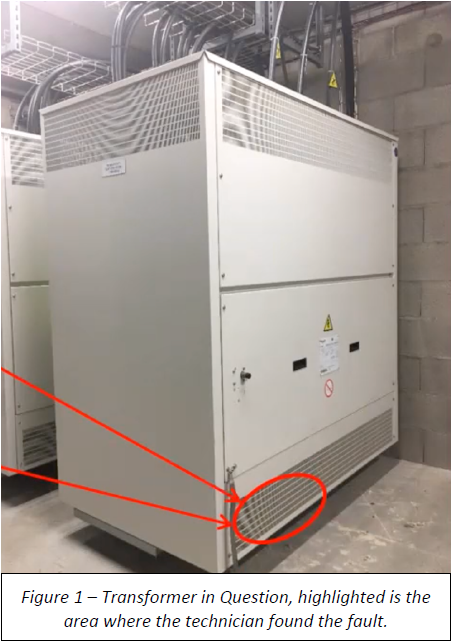
In the Ultrasound Spectrum seen in Figure 2 we can see peaks with a Delta F= 50Hz (electrical frequency in Europe where the readings were taken).
Periodic shocks such as this are linked to a destructive corona effect. Which will degrade insulation further.
It was recommended that the transformer be thoroughly cleaned.
The successful implementation of ultrasound technology helped our client better monitor the health of their high-voltage electrical systems. They were able to proactively address a potential issue right away. Reducing future downtime.
The insights gained from these inspections, coupled with the advanced analysis capabilities of UAS3, provided ultrasound inspectors with a comprehensive solution for ensuring the reliability and longevity of their electrical assets.
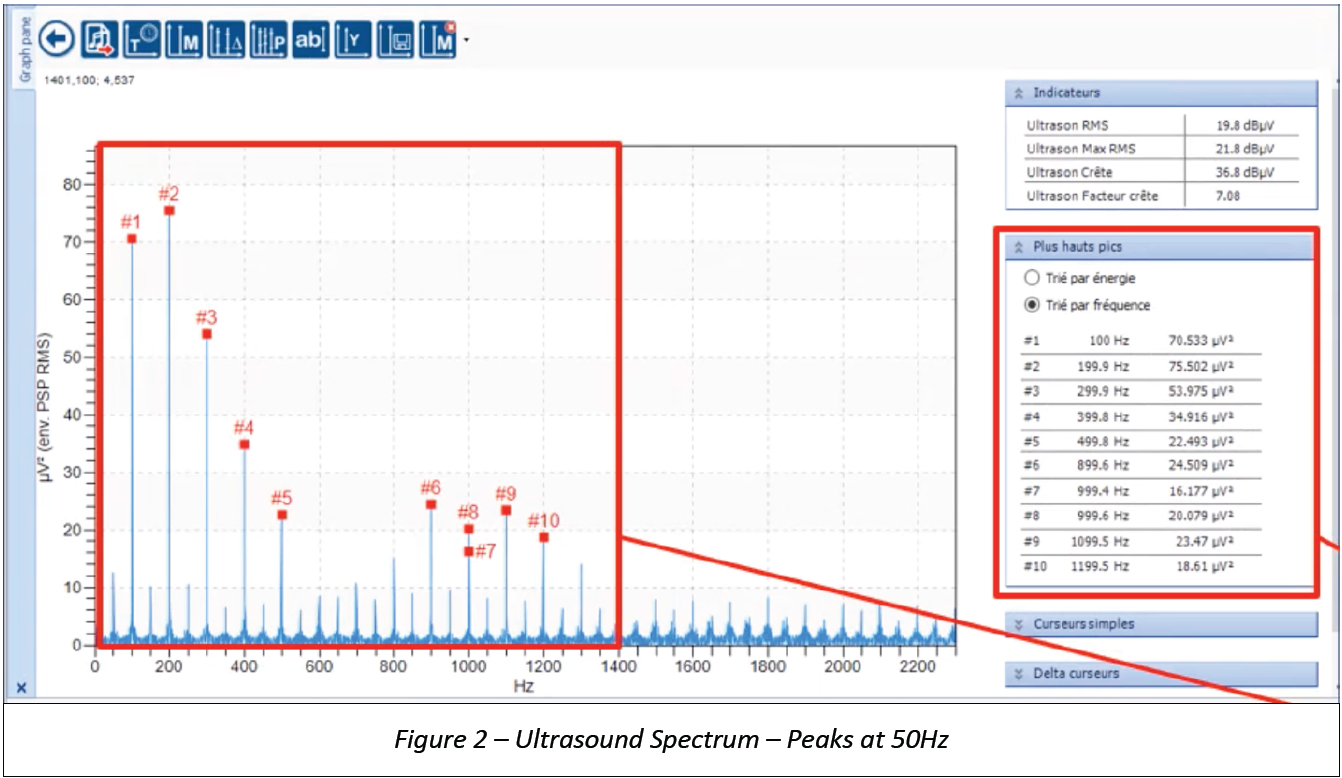