Efficient industrial operations hinge on the optimal performance of critical components such as steam traps and valves.
While often relegated to routine maintenance, these components however help achieve substantial energy savings, ensure safe operations and guarantee environmental sustainability. The Vigilant remote monitoring solution allows better maintenance of these assets, enabling industries to achieve predictive maintenance goals and meet modern energy efficiency standards.
The role of steam traps in industrial operations
Steam traps are indispensable in industrial environments, where they function to discharge condensate from steam systems while preventing the loss of live steam. These components play a big role in conserving energy and maintaining the integrity of production systems. However, without regular monitoring, steam traps are prone to failure.
It is estimated that up to 30% of steam traps in operation fail at any given time, resulting in massive energy losses. A single malfunctioning steam trap with a small leak—just 3 mm in size—can cost facilities over €6,000 annually in energy waste. This figure grows exponentially across a large network of steam traps. The environmental impact is similarly significant, with increased carbon dioxide emissions undermining corporate sustainability initiatives and compliance with ISO 50001 energy management standards.

Neglecting steam traps leads to more than financial and environmental consequences. Failed traps can cause operational disruptions such as water hammer, pipeline corrosion, and excessive wear on critical equipment. These issues can culminate in costly system failures, unplanned downtime, and even catastrophic incidents. A well-known example is the 2007 New York City steam pipe explosion, where a clogged steam trap contributed to significant damage, injuries, and litigation.
The Vigilant addresses these challenges by providing real-time diagnostics for steam trap performance. Using ultrasound technology, it detects leaks and blockages with high precision, enabling facility managers to take proactive action and avoid costly failures.
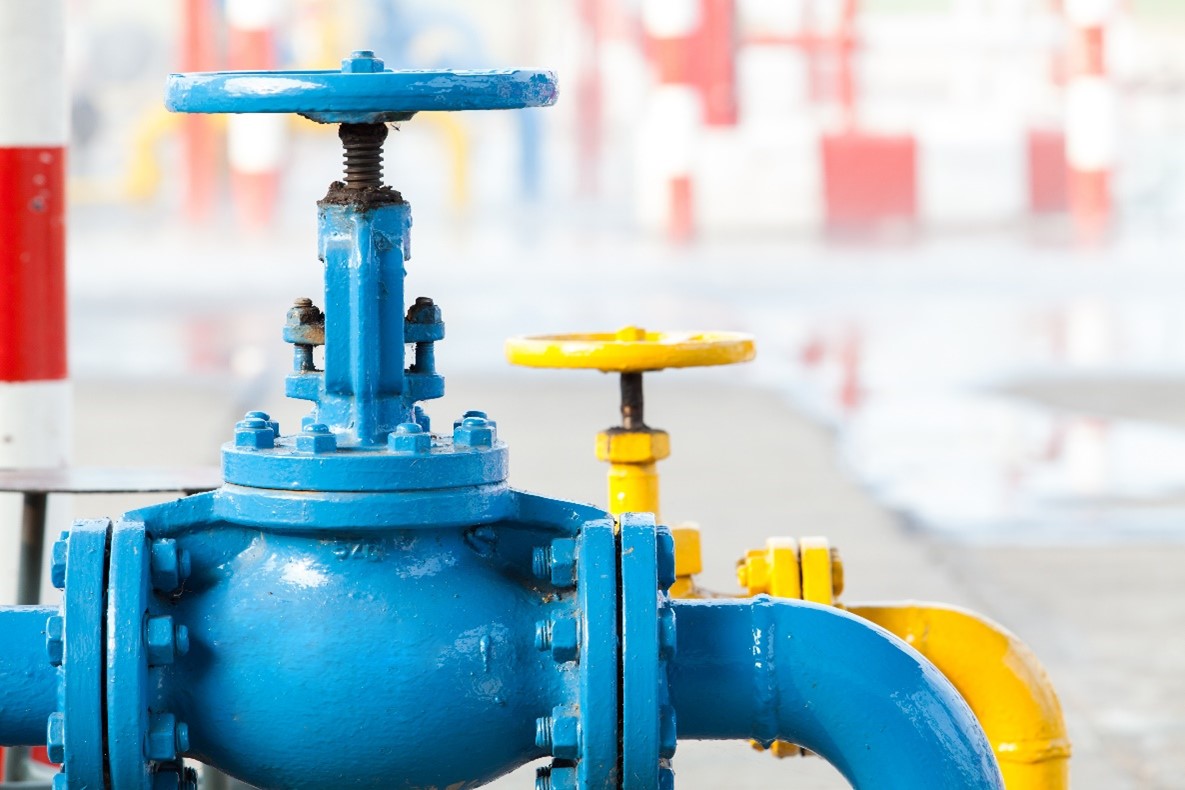
Valves: A critical yet overlooked asset
Valves are another very important component in industrial systems, regulating the flow of fluids, gases, and steam. They are used across applications, from flow control to safety systems, yet are often deprioritized in maintenance programs. This oversight can lead to significant inefficiencies and safety hazards.
Valves can fail in numerous ways: they may become blocked, leak, or experience cavitation due to high-pressure differentials. In many cases, these failures compromise the operational reliability of entire systems, increasing the risk of downtime, safety incidents, and energy waste. On offshore installations, valve failures carry even higher stakes, with potential for environmental disasters and non-compliance with strict regulatory standards.
Despite their importance, valves often suffer from a “run-to-failure” maintenance mentality, where issues are addressed only after a failure occurs. The Vigilant helps with valve maintenance by enabling continuous condition monitoring. It excels at identifying failure modes related to turbulent flow, mechanical friction, and cavitation. By detecting these problems early, the Vigilant ensures that valves function efficiently, reducing energy consumption and preventing costly downtime.
The cost of neglect
Neglecting the maintenance of steam traps and valves carries steep consequences across financial, operational, and environmental domains. Energy loss from leaking steam traps directly translates to higher operational costs. For a plant with 10% of its steam traps failing, the annual financial losses can reach tens of thousands of euros.
Operationally, faulty traps and valves increase the risk of equipment breakdowns and production delays. For example, a single blocked valve or steam trap can cause water hammer, leading to extensive pipeline damage and the disruption of entire processes. The cost of repairing such damage and addressing the resulting downtime can quickly escalate into millions of euros.
Safety risks are another significant concern. Leaking steam traps and valves increase the likelihood of accidents, including pipe bursts and burns from steam leaks. These incidents endanger personnel, expose companies to legal liabilities, and damage reputations.
On the environmental front, inefficient steam systems contribute to higher greenhouse gas emissions. According to the United States Environmental Protection Agency (EPA), maintaining steam traps can reduce CO₂ emissions by up to 10%. Companies that fail to prioritize these maintenance tasks risk undermining their sustainability commitments and environmental compliance efforts.
The Vigilant solution
The Vigilant offers an approach to steam trap and valve maintenance. By harnessing ultrasound technology, it detects the early signs of failure, allowing facility managers to implement predictive maintenance strategies. Unlike traditional reactive or time-based maintenance methods, the Vigilant provides real-time insights into the health of these components, enabling immediate corrective actions.
For steam traps, the Vigilant identifies common issues such as:
- Leaks: These occur when trap components wear out, allowing live steam to escape and causing energy losses.
- Blow-through conditions: Excessive wear may allow steam to bypass the trap, leading to wasted energy and potential system damage.
- Blockages: Condensate buildup due to blocked traps can result in water hammer and corrosion.

For valves, it monitors conditions such as:
- Turbulent flow: This indicates leaks or blockages that compromise system efficiency.
- Mechanical friction: Excessive wear and tear can lead to valve failure.
- Cavitation: High-pressure differentials can cause turbulence, which the Vigilant detects with precision.
Long-term benefits
The Vigilant’s integration into maintenance programs delivers far-reaching benefits:
- By identifying and addressing inefficiencies early, the Vigilant prevents energy waste and reduces repair costs. Facilities that implement the Vigilant have reported energy savings of up to 25% and significant reductions in unplanned downtime.
- With real-time monitoring, the Vigilant helps industries meet ISO 50001 standards and reduce their environmental footprint. By minimizing steam losses, facilities can achieve substantial reductions in CO₂ emissions.
- Continuous monitoring mitigates risks associated with steam and valve failures, ensuring a safer working environment and uninterrupted operations.
Case study: Realizing tangible benefits
A European manufacturing plant implemented the Vigilant to monitor its steam traps and valves. Within the first six months, the facility achieved:
- A 25% reduction in steam losses.
- Annual energy savings of €120,000.
- Fewer maintenance interventions, resulting in lower labor costs.
The company not only improved its operational efficiency but also achieved compliance with environmental regulations, enhancing its corporate image and securing its competitive edge.
Conclusion
With energy efficiency and sustainability becoming ever more important, Vigilant offers a powerful tool for optimizing industrial systems. Its ability to continuously monitor steam traps and valves changes maintenance practices, ensuring operational efficiency, cost savings, and environmental compliance.
By adopting the Vigilant, industries can move beyond traditional maintenance approaches and embrace a predictive strategy that safeguards their assets, enhances sustainability, and secures their competitive edge.