Leak detection should be a top priority when we know that, without a leak detection program, leaks represent 30-40% of the volume consumed.
Unfortunately, maintenance managers all too often tend to ignore the problem. How can you justify a “detection project” to management? Here are some arguments…
In recent years, maintenance and production managers have been faced with exceptionally complex requirements. Indeed, the goals of making a company more competitive often seem contradictory. Energy costs must be reduced, maintenance investments must be decreased and better service must be provided with less manpower, while ensuring optimal equipment operation in order to produce more, better and cheaper.
Compressed air leaks = serious consequences
Malfunctions and breakdowns leading to deficiencies in production facilities can have major consequences for production and logistics. Consequences that competitiveness objectives can no longer allow! Under these circumstances, a predictive maintenance program (or condition-based maintenance, depending on the vocabulary used) is one of the decisive and strategic priorities. Detecting and repairing even the smallest compressed air leaks fits perfectly into this strategy. Especially since compressed air is very energy intensive.
Widely used and energy intensive
Compressed air is easy to produce. It generates no pollution or waste. It uses inexpensive and robust components and is easy to transport via inexpensive piping. There is no risk in case of accidental leakage. These advantages explain why compressed air is the fourth most used energy source in industry, after electricity, natural gas and water. On average, it represents 13% of industrial electricity consumption in France. However, its use is not without drawbacks. Air is not compressed in its natural state. Energy is, therefore, required to compress it artificially. Compressing air is extremely energy intensive due to its low efficiency. Optimizing the production and distribution of compressed air is, therefore, crucial. In this context, the search for and repair of leaks remains the most cost-effective operation in the short term.
The main expense of producing it is the consumption of electrical energy. For example, if the system is used for 6 000 hours per year for 5 years (24/7 operation), the energy consumed represents 75% of the cost of the compressed air. This rises to 80% for intensive use of 8 000 hours per year for 5 years.
In routine operation, the useful energy is barely 8%, especially when there is no leakage campaign in place. This explains why compressed air is so expensive. Leak detection and repair should be a top priority when it is known that, generally, without a leak detection program, leaks represent 30 to 40% of the volume consumed.
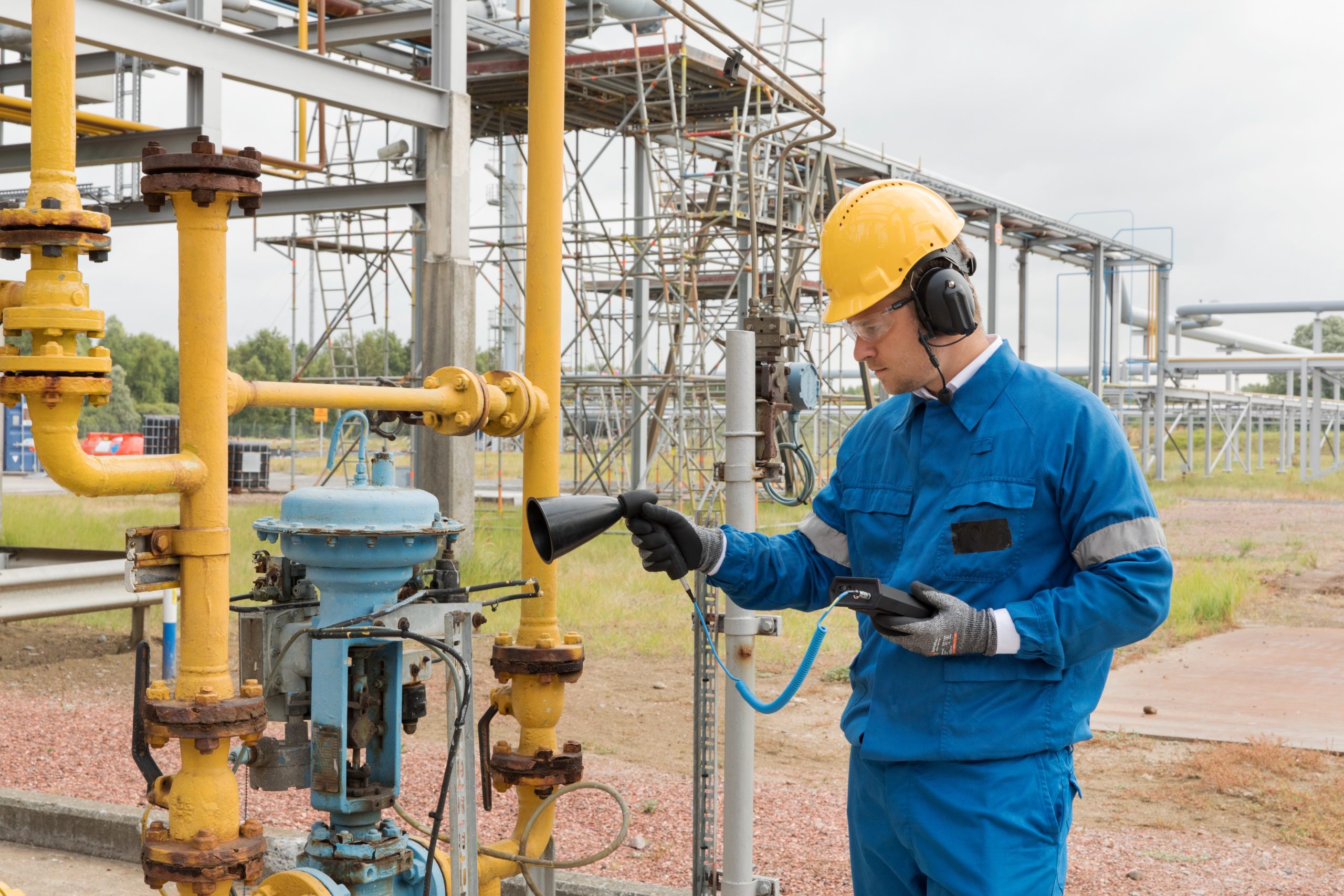
An unacceptable waste
Before thinking of savings on the compressed air system itself to increase efficiency and reduce energy costs, it would be better to think first of correcting the enormous amount of waste generated by leaks. Repairing a single 2 mm leak at 8 bar represents a saving of 3 000 euros per year (or even more depending on local energy costs). It is also important to remember that leaks can occur anywhere in the system: line connections, traps, filters, pressure regulators, valves, quick couplings, rubber hoses, etc. And there are many other places, in the most hidden and inaccessible places.
A real proactive program to hunt down this type of waste is more than necessary to reduce the loss to a reasonable 5% of the volume consumed. From a volume loss of 30 to 40%, the energy and financial savings are considerable. The international average loss (source: Plant Support & Evaluation Inc.) is 34%. This means that one out of every three compressors is only running to supply leaks!
The elimination of leaks is an absolute priority
Eliminating leaks is not the only way to optimize compressed air costs. Optimization of production (control, variable speed and heat recovery) and processing (dryer, filters and condenser) should not be overlooked either. There is, therefore, still a great potential for energy savings among users in the field of pneumatic actuators.
Leakage detection should be a top priority. The search for leaks is relatively simple: two hours are sufficient. Finally, the savings are substantial for an immediate return on investment.
What means do you have at your disposal?
There are several types of ultrasonic detectors that can be used to find leaks. The most effective ones are designed to be safe, easy and fun. These detectors can be equipped with accessories and sensors that are chosen based on two key parameters: distance from the equipment being inspected and ease of access. The internal sensor, with or without its precision tips, is designed for easily and directly accessible areas, while the flexible sensor is used for hard-to-reach areas or to bypass an obstacle. The AIRSense, compatible with the Extended Distance Sensor and used with the SDT340 or the LEAKChecker, is highly recommended for detecting leaks that produce low levels of ultrasound (very small leaks or vacuum leaks, for example) or if the distance between the operator and the equipment is 5 meters or less. The parabolic sensor is the most appropriate tool to use when the areas to be monitored are at distances greater than 5 meters and up to 30 meters. Its laser sighting also makes it possible to locate the location of the leak at a distance.
How does one go about presenting a leak detection project?
When presenting your project to management, you can highlight the results of a leak detection campaign. For this purpose, SDT has developed the LEAKReporter, a free app designed to quantify the recorded compressed air losses and highlight the energy savings after the repair operations. This app is based on the recording of leakage data and the conversion of measured losses (dBµV on the detector screen) into L/h and euros/year. It quantifies the detected leaks, establishes the repair priority and calculates the profit generated by each repair.