Mechanical Condition Monitoring
Detecting mechanical faults before they stop production
Bearing and Machine Maintenance
Industry runs on machinery. Bearings, pumps, electric motors, compressors, presses, gearboxes and much more. All of which can break unexpectedly, causing production to stop. When production stops your organization loses money.
Few bearings make it to the end of their engineered lifecycle. This is due to poor workmanship, bad lubrication practices and neglect. Therefore, problems can even arise right after installation due poor installment of the machine.
No two machines are the same. Across industry, machines operate under different loads, climates and conditions, making their maintenance requirements unpredictable. Also, many machines are still maintained on calendar based PM’s, while others are run-to-failure. Both strategies are wasteful. There has to be a better way…
Poorly Maintained Equipment leads to Catastrophic Failures
Without regular inspections and condition monitoring there’s no way of knowing the exact condition of your assets. Subsequently, unexpected machine breakdowns sneak up on you, threatening your bottom line, the environment, and worst of all, workers’ safety.
Downtime is expensive, and that cost is amplified when it is unplanned. A condition monitoring program trends and analyzes asset health to anticipate and plan for futures failures.
Knowing the condition of your assets is the only way to ensure ZERO unplanned downtime, and that your factory’s machinery is running efficiently and safely.
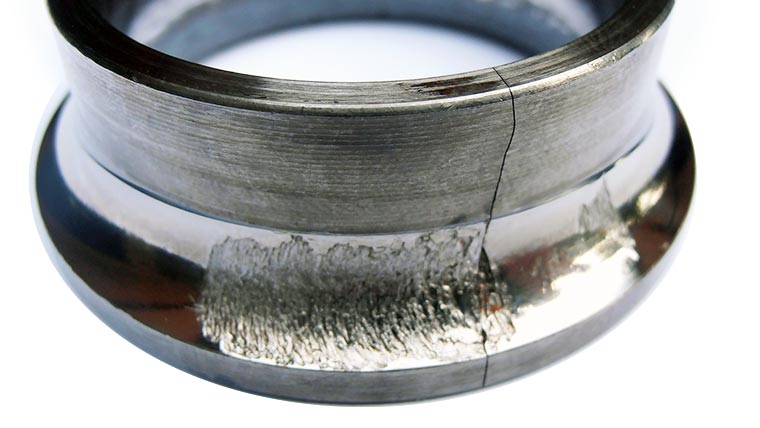
Why use Ultrasound for Mechanical Inspection?
Ultrasound detects friction, impacting and turbulence earlier than any other condition monitoring technology.
Bearing defects cause friction and impacting. Lubrication issues, whether it’s under or over lubrication, cause increased bearing friction and eventually impacting. However, ultrasound detects these faults early before the bearing reaches the point of no return, in order to plan a corrective maintenance to restore the bearing and machinery.
Ultrasound owns the APEX of the D-I-P-F Curve, giving maintenance the biggest window of opportunity to prepare.
How to Predict Bearing Failures with Ultrasonic Condition Monitoring
The first step to ultrasound bearing monitoring is establishing a baseline dB level for each machine. There isn’t a decibel domain a bearing should reside within which is why each machine needs its own baseline to be established. This can be done a few different ways. For example, analysis can be performed on a new, healthy bearing or it can be performed on other, similar bearings which operate under similar loads.
Establishing accurate baselines for healthy equipment is very important to your bearing condition monitoring program as it creates a reference point for multiple aspects of future bearing analysis.
Next, it’s time to take readings with your ultrasound device. Your sensor should be placed on top of the bearing housing for the most accurate measurement. Record your measurement and look for dB gains that could indicate a mechanical fault. As a rule of thumb anything over an 8 dB gain requires investigation. This gain could be a result of under or over lubrication or possibly the early stages of a bearing failure. A dB gain that eclipses 12-16 over the baseline is an indication of bearing degradation. When dB gains get anywhere above 30 over baseline it is a warning of a potential catastrophic failure. Thus, maintenance should be planned immediately to avoid the failure.
More advanced analysis can be done in the FFT, timewave form of the recording. This can help determine what the cause of the dB gain might be. Consistent, repetitive dB spikes could be the indication of imperfections on the bearing, which will worsen over time if left unchecked. Whereas relatively inconsistent dB spikes could be the result of under or over lubrication.
Why you need a Condition Monitoring Program in your Facility
A condition monitoring program is specifically designed to combat unexpected breakdowns and unplanned downtime. The only thing worse than unplanned downtime caused by an unexpected asset failure is a worker injury caused by that same unexpected failure. Unmonitored, poorly maintained equipment is more likely to be running inefficiently and spontaneously breakdown. The results can be dangerous and costly.
A condition monitoring program puts establishing baselines and alarms, scheduling routes, recording measurements, analyzing those measurements and planning and performing maintenance tasks all together to improve plant reliability.
Ultrasound testing can significantly advance reliability. Sadly, these initiatives often fail due to lack of dedication, training, implementation and mentoring. Partnered Ultrasound defines a road mapped strategy, unique to your plant and situation. Partnered Ultrasound ensures training, implementation, mentoring and dedication are all taken care of. Allowing you to realize the full potential of your Ultrasound program.
Questions concerning Mechanical Condition Monitoring
The Best Tools for your Ultrasound Mechanical Condition Monitoring Program
Mechanical Condition Monitoring Highlights