Vigilant
A turn-key condition monitoring solution combining the versatility of ultrasound, the analytics of vibration, standard communication protocols and an embedded trending and analysis software.
Configure Vigilant to any Critical Asset
Vigilant is a flexible data collection pod. Input any combo of eight ultrasound and vibration sensors and receive continuous feedback from your assets.
4 channels for Temperature, Tach and Pressure create an all-in-one solution for critical and guarded assets.
Vigilant Highlights:
- 8 channels (Ultrasound or Vibration)
- 4 channels (Temp/Tach/Process)
- Embedded data management software
- Trends/Spectrum/Waveform/Waterfall
- Open communications protocol
- Static and Dynamic data
Designed for CONMONSense
Vigilant accepts data from commonly available sensors including the CONMONSense Sensors from SDT, designed to provide repeatability in any industrial environment.
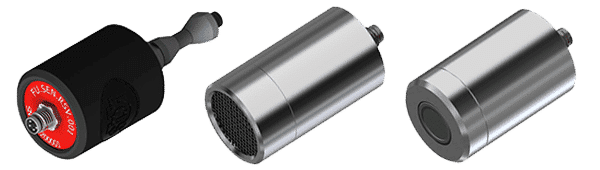
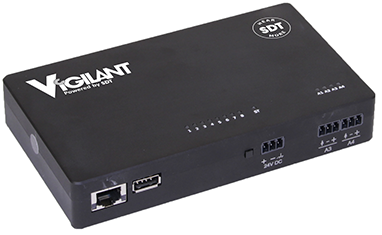
Embedded Data Management Software
View the status of any asset from the security and convenience of your favorite web browser.
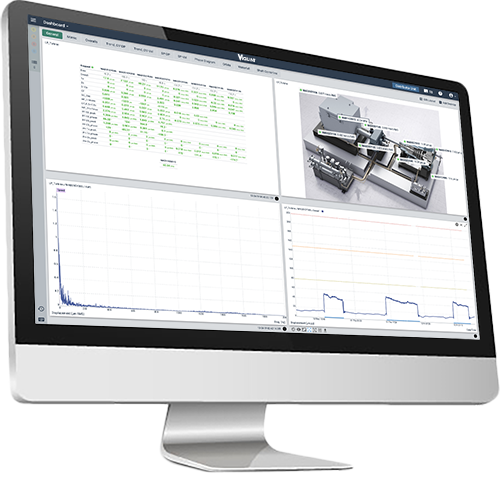
Configuration
Vigilant includes a web interface to configure all the system options and monitoring features available on the units.
Alarm Log
From any of the desktops the users have access to the “Alarm Log” that shows all the events or anomalies detected in the monitored machine in real-time.
Widgets
Widgets for static trends, dynamic time waveform plots, as well as spectral analysis.
Layouts
Size, position, and arrange widgets to create custom desktop layouts.
Dashboard
The Dashboard visualizes the real time measurements performed by the Vigilant. It also shows the historical data stored in the unit.
Applications
- Early detection of rolling element bearing faults (especially in slow speed applications);
- Status of couplings on critical assets in limited access locations;
- Monitor guarded assets such as robotics or CNC machine centres;
- Lubrication status of roller bearings;
- Valves deemed critical to a process;
- Detection of partial discharge in electrical assets such as MCC panels and switchgear cabinets;
- Detection of friction or impacting in linear motion applications;
- Detection of turbulence produced by cavitation in pumps and valves;
- Detection of hydro-cyclones used in mining processes.
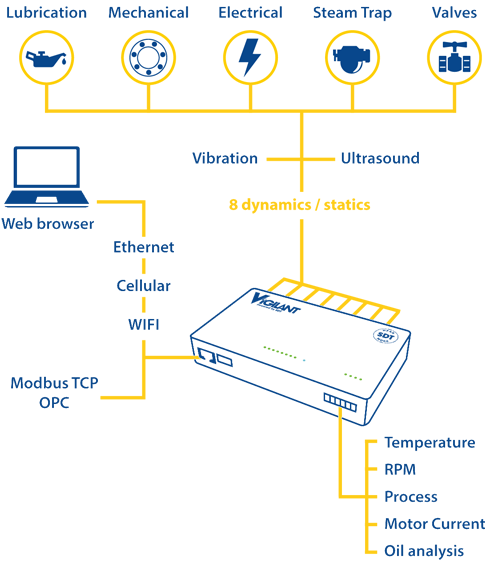
Vigilant Permanent
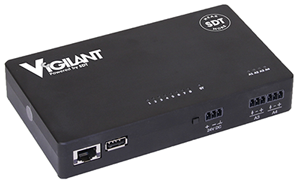
- 8 high-speed (Dynamic) multipurpose analog inputs;
- 4 channels (Temp/Tach/Process);
- ICP power source available on all dynamic inputs;
- Ethernet TCP/IP communications;
- Powered at +24 Vdc.
Vigilant Mobility

- Same function as Vigilant Permanent;
- Packaged in rugged, custom waterproof case;
- Designed to travel to off-site assets;
- Install on assets in alarm to closely monitor until planned shutdown.