for Heating Systems in 20th Century Buildings
A local private school conducts annual maintenance checks on their steam heating system during the Christmas Holidays when the students all go home. Their goal is to ensure the components of their steam heating system are functioning correctly before the students return for the cold season from December to February.
Overview
- This schools steam powered heating system is comprised of over 400 Steam Traps spread out over multiple buildings. It took an SDT Ultrasound Technician two days to complete the survey using their SDT340.
- Their final report indicated that 64% of the traps were functioning correctly, 15% were out of operation, 3% had failed open, another 3% had failed closed, 15% of the traps were beginning to show early signs of impending failure.

A Brief History About Steam Heating Systems, and where They’re Commonly Found.
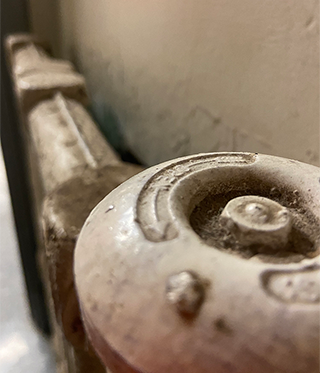
Steam heating systems for buildings has been around for more than a century. It is a simple and reliable way to distribute heat throughout a large building. Steam heating systems use boilers to heat water and create steam, which can then be piped to radiators throughout the building, where the steam then rises, giving off heat and warming the rooms.
Steam heating systems were the most popular method of heating buildings in the 20th century, and many buildings constructed before the 1950s still use them today, as retrofitting newer and more efficient systems proves challenging.
Steam heating systems are most commonly found in the northeastern United States, particularly in cities such as New York, Boston, and Philadelphia, where many buildings were constructed before the 1950s.
Hospitals also use intricate steam systems for a variety of reasons not limited to heating. Medical facilities utilize steam to heat water for laundry and cleaning, as well as to sterilize medical equipment, instruments, as well as linens and clothing.
The Steam Trap
As steam travels from the boiler room to its intended point of use it gradually cools and condensate accumulates.
Simply put, a steam trap is a component of a steam system that removes condensate, and non-condensable gasses from a steam system ensuring that only hot, pure steam reaches the intended point of use.
A steam trap achieves this by opening and closing automatically depending on the presence or absence of condensate.
When there is condensate present, the steam trap opens and allows the condensate to be discharged. When it is not, the steam trap remains closed, preventing steam to escape.
They come in different types, shapes, and sizes which all vary depending on the different applications the steam system is being used for.
Some categories of steam traps are mechanical, thermodynamic, and thermostatic.
It is important for maintenance and reliability teams to regularly schedule maintenance and condition monitoring on their steam traps, as they can fail open or closed, which leads to wasted energy, heat loss, and impure steam reaching the intended point of use, resulting in gradual equipment damage.

Testing a Steam Trap

The most popular non-invasive form of testing the condition of a steam trap involves two readings and an ultrasound detector. One taken a few feet upstream of the steam trap to ensure there is a flow of steam, and the other reading taken immediately after the steam trap.
If the steam trap is operational, the cycle will be audible with the assistance of an ultrasound device. To put it in ultrasonic terms, this means that the signal downstream of the steam trap should be silent, followed by intermittent increases in dBμV levels, indicating a discharge.
Failed Closed
As previously mentioned, steam traps either fail open or closed. A great way to determine one has failed closed is using an ultrasound detector built in spot radiometer to measure the traps temperature.
Most sophisticated ultrasound data collectors have a spot radiometer for recording and measuring temperature readings.
Using the SDT340’s Spot Radiometer, maintenance and reliability teams can check to see if live steam has reached the steam trap. If the steam trap is failed closed, condensate will have gathered near the opening of the steam trap, reducing the temperature of the trap.
While preforming this inspection, technicians must consider heat transfer. Heat transfer is simply how much thermal loss occurs from the inside of the piping system to the outside of the piping system, where temperature readings are being taken. It is safe to assume that there will be about a 10% thermal loss from the interior of the steam system to its exterior. Therefore, maintenance and reliability teams can expect a 100 PSI steam system which is internally 338 degrees Fahrenheit to show an external temperature of around 300 degrees Fahrenheit.
Failed Open
Once maintenance and reliability teams have concluded their steam trap is not failed closed, they must check for the other common steam trap failure mode – failed open.
Using an ultrasound detector, determining if live steam is getting past the steam trap and dumping into the condensate system is an easy process. Technicians are simply trying to detect turbulent flow inside the steam system’s piping.
Take a contact ultrasound probe and touch it to the upstream side of the steam trap. Technicians should look for any inherent background ultrasonic signatures in the system.
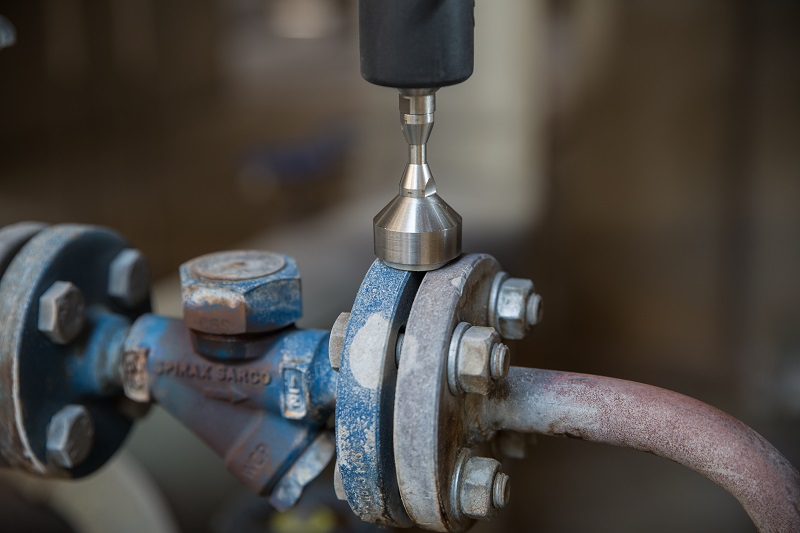
Now touch the contact sensor to the downstream side of the trap and listen. With a functioning trap, technicians should expect to hear an ultrasound signal less than or equal to the original ultrasound reading taken upstream. If the ultrasonic signal is significantly louder on the downstream side of the trap, that is the sound of a steam trap discharging. If it continuously discharges, that is a faulty steam trap that has failed open. Time to fix it.
Conclusion
To put it into a few succinct words, if a steam trap is hot and quiet, it is working correctly.