For years, the reclaimer at a paper mill in north-western France had worked reliably, pivoting on three pinions mounted on reducers. The reclaimer is used to collect wood chips from a pile and convey them by buckets. However, quite unexpectedly, the structure supporting this equipment collapsed. Fortunately, the company had implemented a monthly preventive maintenance program to monitor the condition of these slewing rings.
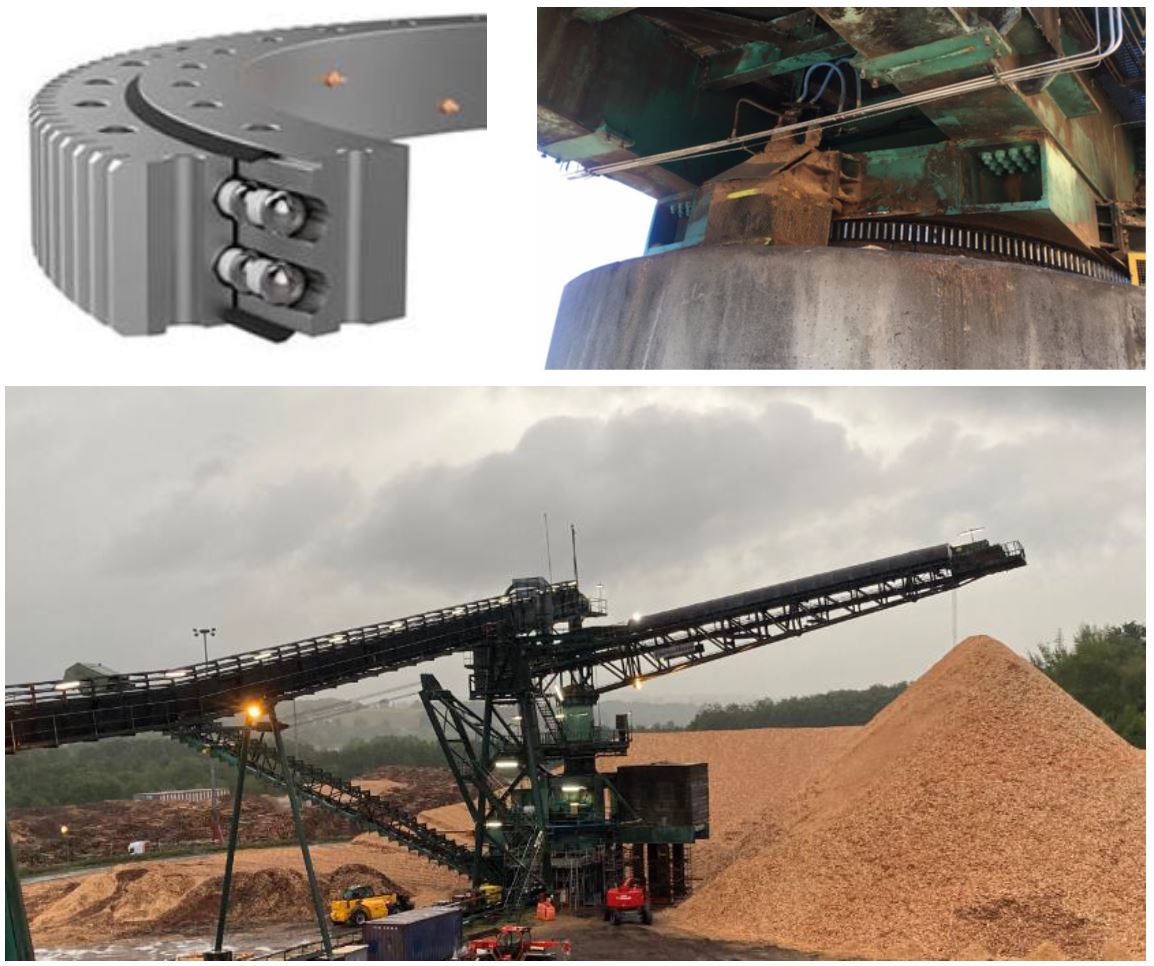
It was at this point that the company made a key decision. They decided to rely on technology to assess the severity of the ring’s breakdown after the collapse. They used an ultrasound measuring device (SDT340), the only technology that could provide an in-depth analysis of the situation. Reference measurements taken prior to the incident were retained to enable the current state to be compared with the initial state.
The measurement process was complex. To make an accurate assessment, they had to rotate the equipment between two of the three sprockets for one rotation cycle, which took about two minutes. In addition, there was no known frequency, at least none provided by the manufacturer, for these slewing rings. The speed of rotation was not always constant, making the task even more complicated.
However, the company was not discouraged. They knew that only a time waveform and careful listening could reveal the signs of a potential problem. By analyzing the data collected using ultrasound measurement technology, they were able to identify anomalies and deformations in the crown, indicating significant degradation.
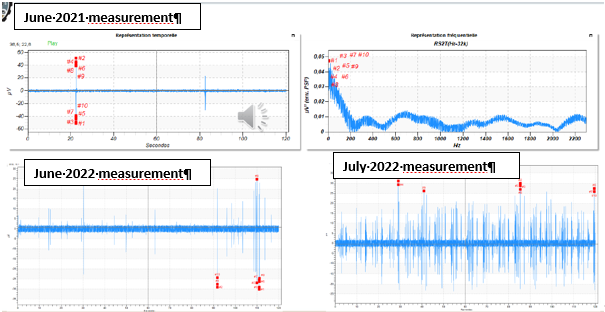
The image above shows a rather evolutionary time waveform. Relatively normal measurements in June 2021 gradually shift towards the beginnings of unusual shocks in June 2022, culminating in a much more serious situation the following July.
After extensive work, the team was able to determine that some equipment was missing a number of rolling elements essential to its proper functioning. The missing rolling elements were probably due to wear of the “spacers” between the balls acting as cages.
Thanks to this early discovery, the company was able to take corrective action to avoid a major malfunction that would have had serious consequences for the safety and efficiency of their products. They undertook immediate repairs and reinforced their preventive maintenance procedures.
The decision to invest in ultrasound measurement technology proved to be a wise one for this company. Not only did it prevent a major incident, it also reinforced their reputation as an industry leader, demonstrating their commitment to product quality and safety. This success story illustrates how cutting-edge ultrasound technology, prevention and innovation can save companies from potentially catastrophic situations.
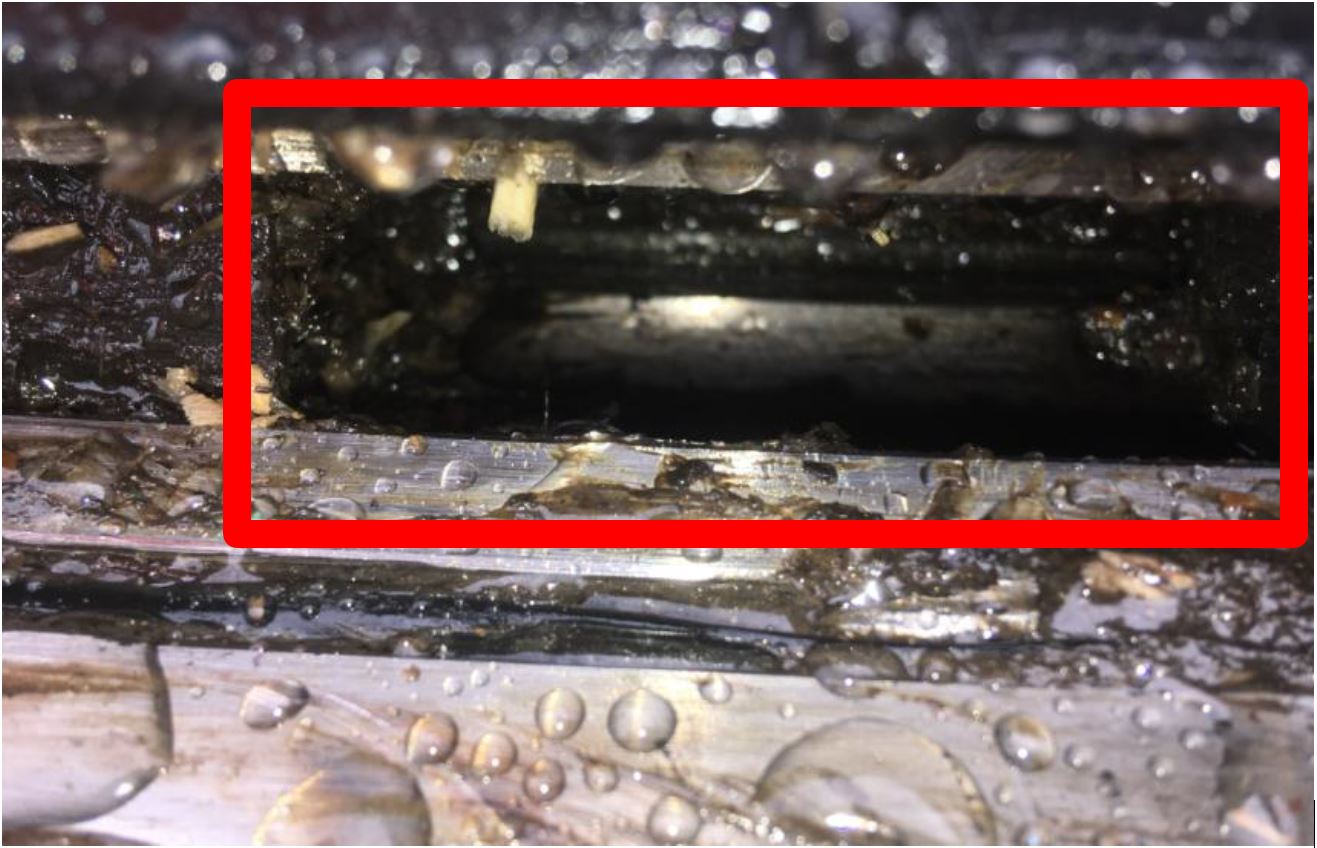
Author: Gauthier Ghislain