Compressed air, the versatile force of industry, powers tools, automates manufacturing and propels various machines. The fourth most important utility, along with electricity, water and gas, its omnipresence is accompanied by high energy costs, making it the most voracious consumer of all.
Let’s break it down: when investing in an air compression system, barely 25% is spent on the initial installation, while 75% is spent on the energy required to compress the air. A crucial question then arises: how can this be remedied, and why might ultrasound be the tool of choice for detecting leaks in compressed air systems?
Ultrasound is particularly effective at detecting friction, impact or turbulence. When compressed air escapes through a leak, it generates a turbulent flow and a high-frequency whistling sound. Audible in almost total silence, this whistling sound is often lost in the hubbub of production workshops. Although other techniques exist, such as the soapy water test, ultrasound is a cleaner, more effective solution for detecting air leaks quickly and efficiently.
Let’s take a look at why it’s imperative for every plant to adopt a compressed air leakage management program. The goal is clear: zero injuries, zero downtime and zero waste. Although only one piece of the puzzle in a comprehensive predictive maintenance plan, a leakage management program plays a vital role in significantly reducing, if not eliminating, compressed air wastage. The repercussions of compressed air shortages go beyond inconvenience; they hamper production speed and compromise product quality. Plants that adopt these practices not only see improvements in these areas, but also a positive impact on their bottom line.
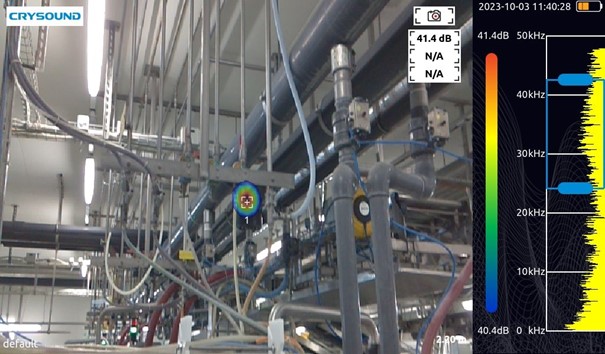
Among reliability initiatives, leak detection campaigns scheduled and planned as part of a compressed air leak management program are distinguished by the fastest return on investment. It’s the logical first step in a plant’s reliability journey, delivering tangible savings in terms of downtime and energy consumption.
Addressing the common reasons why a leaky compressed air system might be low on the priority list for maintenance staff:
- Some may not associate compressed air with significant energy consumption.
- Not all maintenance technicians might be aware of the quickest and easiest ways to locate compressed air leaks.
- Maintenance teams might be hesitant to use ultrasound detectors for fear of the time and effort involved in identifying and fixing leaks.
In essence, a leaking system compromises production demand, depletes resources and contributes to unnecessary greenhouse gas emissions, all of which have a negative impact on our environment.
The CRYSOUND acoustic imager is a game-changer in compressed air leak detection. Capable of accurately locating leaks up to 120 meters away, CRYSOUND features 128 state-of-the-art MEMS sensors for ultra-sensitive detection of compressed air leaks. Its capabilities extend to covering vast distances and displaying the exact distance of the fault on the camera screen.
In noisy industrial environments, the CRYSOUND acoustic imager’s focusing function eliminates ambient noise and interference, allowing users to concentrate on the task in hand. The camera’s ability to detect the slightest variations in sound ensures accurate identification of leak sources.
But innovation doesn’t stop at detection. SDT Ultrasound Solutions also offers the LEAKReporter, a comprehensive management system providing a free platform for easy reporting. By simply inserting photos taken by the CRYSOUND imager into the LEAKReporter app or CMS, users can effectively document their findings and track their initiatives to contribute to a more sustainable environment.
Indeed, reporting and documenting leaks becomes a seamless process thanks to this tool. Basically, it works like this:
- Create a survey and thoroughly inspect your factory for leaks.
- Document your findings with pictures, input the ultrasonic readings.
- Use measurements to estimate the cost impact of leaks.
- Synchronize your completed survey with the web browser.
- Generate comprehensive reports and share your wins throughout your organization.
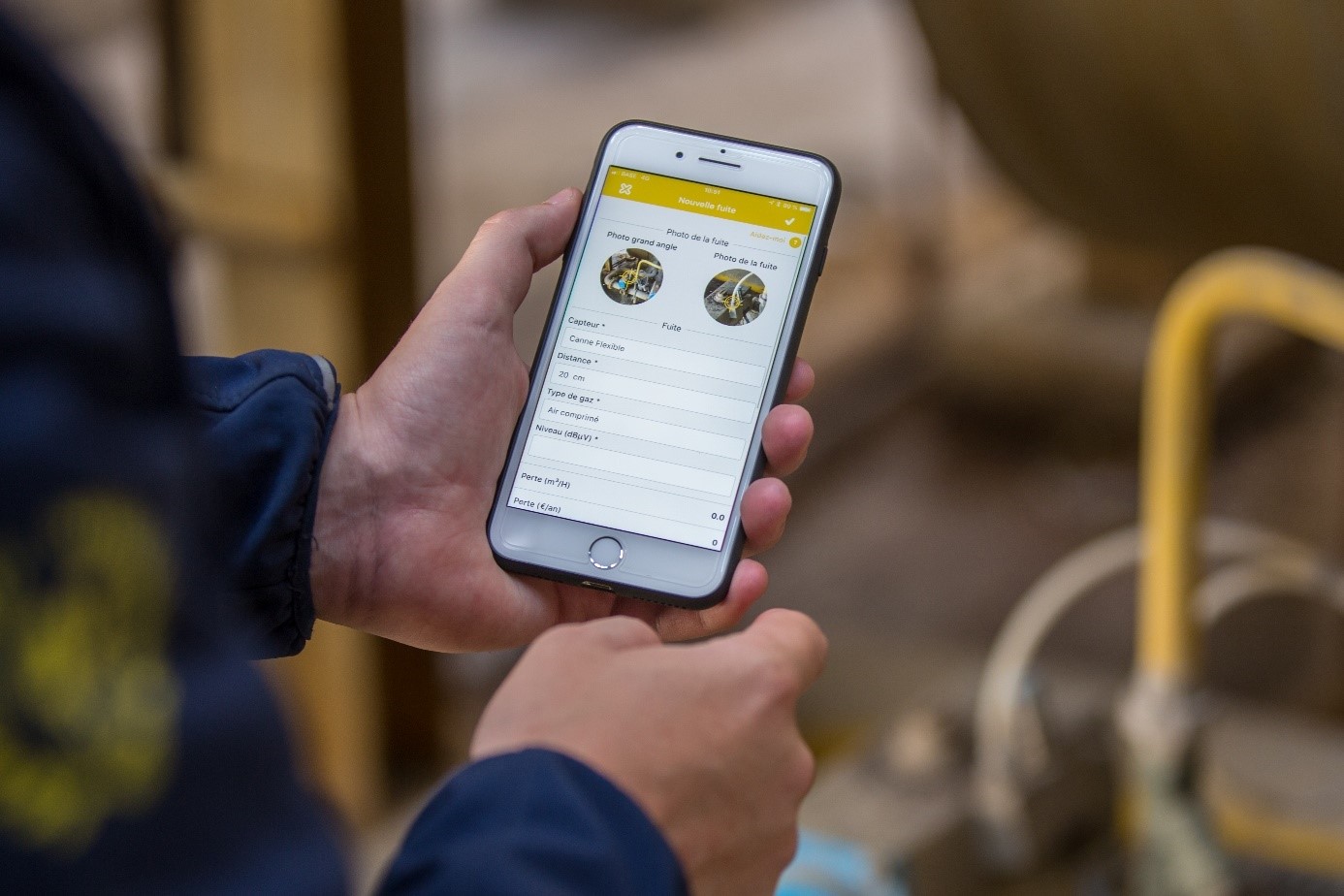
A few figures to illustrate just how useful the combination of the CRYSOUND imager and the LEAKReporter can be:
Over the last 6 years, the LEAKReporter app has facilitated the gathering of data from 15 050 leak detection surveys. Among 5 243 users, a grand total of 189 485 leaks were successfully identified. The app allowed for an estimated €2 188 976 114 of potential losses resulting from these leaks if left unrepaired. Out of those, 32 235 leaks were successfully repaired, resulting in a staggering €99 771 976 in savings.
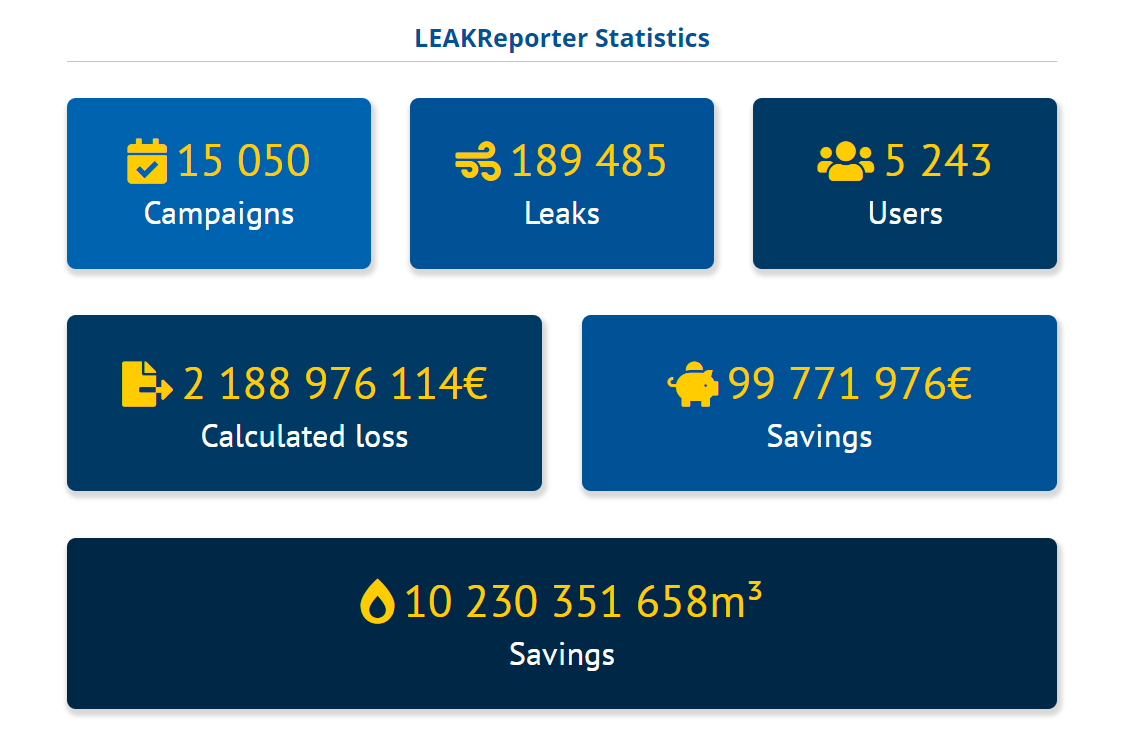
When you’re faced with figures like these, you start to wonder. And we’ve got the answers.The CRYSOUND acoustic imager, combined with the LEAKReporter, is an indispensable duo in the quest for efficiency, savings and sustainability in the industrial landscape. With its cutting-edge technology, intuitive reporting system and substantial return on investment, it not only addresses the pressing problem of compressed air leaks, but also propels factories towards a more reliable and environmentally-friendly future.