Ultrasound Hears above the Roar of your Factory
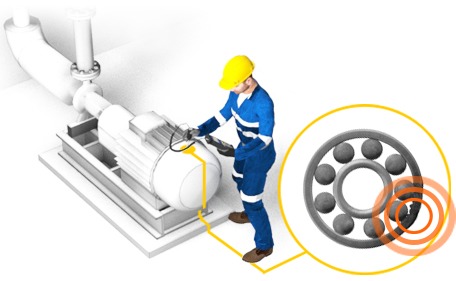
Ultrasound signals from failing assets are measured, trended, and analyzed so we can execute an action plan that minimizes the impact.
Manufacturing is noisy. Factories are loud. When you’re in a deafening loud facility it’s hard to hear the metal on metal scraping of your faulty bearings, or the perpetual hissing of compressed air seeping through leaks. Many of these faults go unnoticed because they are impossible to find without the proper tools, training and mentorship. That is when ultrasound detectors come into play.
An SDT ultrasound detector is able to listen past the roar of production to find, and pinpoint faults that are not detectable otherwise. Ultrasound is able to find these faults far earlier than any other asset condition management technology.
Reliable plants need FIT assets
Most defects that threaten uptime produce Friction, Impacting, and Turbulence (FIT). These conditions exist silently in the ultrasound region. Find one – or any combination – of these and you now have data to monitor the asset condition at an advanced level.
Why use ultrasound detectors in your factory?
Ultrasound detectors let you detect, measure and analyze friction and impacting in mechanical systems. Turbulent flow from compressed air and steam leaks helps you quickly identify costly energy waste. Ultranalysis Suite software lets you establish baseline readings and set alarms that tell you when your equipment is transitioning from good to bad.
Versatility
Ultrasound’s versatility is unlike any other condition monitoring technology. SDT identified eight application pillars and within each pillar there are virtually hundreds of ways to increase safety, eliminate unplanned downtime, and reduce energy waste. Ultrasound is the first line of defense for industries seeking higher profits and a sustainable future.
Ultrasound testing is your first line of defense against unplanned downtime
Ninety-nine percent of all bearings fail, and when they do, your production comes to a standstill.
How do you prevent a single component from crippling your entire facility? By predicting failures before they happen.
Your production depends on healthy, rotating assets. Bearing monitoring is one of many ultrasound applications that gauge the health of your factory. All bearings emit ultrasound signals that are masked by the sounds of your operation. Ultrasonic bearing monitoring enables you to hear, measure and trend these signals and decide if your asset is OK.
Most bearings do not live to their engineered lifecycle, and bad lubrication practices are the leading cause. Lubrication of bearings is one of the most misunderstood and abused tasks in the industry. Knowing when and how much to grease is the key to optimizing bearing lubrication. With ultrasonic bearing monitoring, you’re able to lubricate bearings based on their condition rather than on a fixed schedule. Predict relubrication intervals and add just the right amount of grease with SDT’s integrated ultrasound greasing solutions.