Steam Trap Testing and Maintenance
Keep Your Steam Trap Clean, Safe and Energy-Efficient
Steam is an essential resource used in many industrial processes. Facilities using steam have a vast network of piping, valves, flanges, and steam traps designed to deliver clean, hot, pure, and efficient steam from the boiler room to its intended point of use. Within steam systems there exists constant flow and turbulence.
As pure steam travels from boilers to the intended point of use, cooling is inevitable. The result is accumulated condensate and gases. A Steam traps purpose within this system is to purge the waste and contaminants, keeping the steam and steam system pure.
Steam Traps accomplish this by opening, closing, and modulating automatically, discharging condensate once formed, unless the heat from the condensate can be used. Steam traps are designed to be energy-efficient and not waste quality steam. It removes impurities from the live steam and maintains purity and efficiency throughout the system.
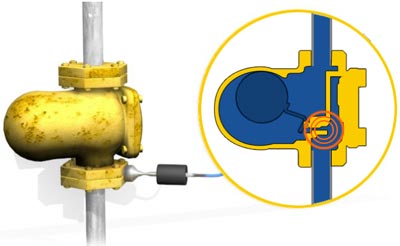
Steam Trap Failure Leads to Lesser Product Quality, Energy Waste, and Safety Concerns
Steam traps are essential in efficiently transferring heat energy through the steam system. When traps fail, money and energy is wasted. Failed steam traps also create back pressure within the steam system, and cause process failures and quality issues during production. In short, failed steam traps lead to unnecessary waste that can be avoided with simple, easy-to-perform, and semi-regular checkups.
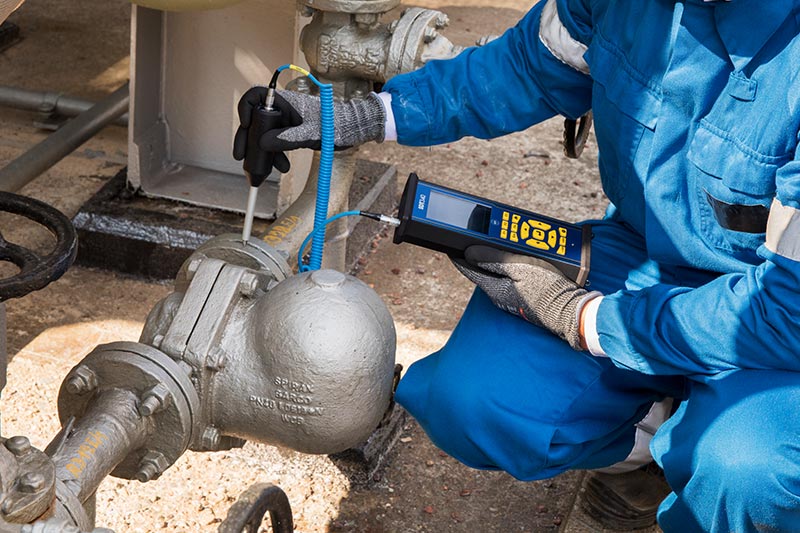
Ultrasound is best for Monitoring Steam Traps
Steam is a gas and as it flows through piping and steam traps there is turbulent flow, or lack thereof. Ultrasound technology’s ability to detect turbulence, even through thick piping makes it an essential tool when looking for faulty, failed steam traps.
Detecting Failed Steam Traps using Ultrasound
Ultrasound technology is the go-to industry standard tool for detecting failed steam traps. Faults are easily detected when the machine is online.
Using Ultrasound, Technicians can hear:
- The opening and closing of a steam trap;
- Silence when a steam trap is stuck in the closed position;
- Turbulent flow when a steam trap is stuck in the open position;
- Mechanical clattering when a steam trap’s valve is fluttering open and shut.
For a complete Steam Trap Inspection, technicians can combine ultrasound measurements with a temperature reading using advanced ultrasound instruments.
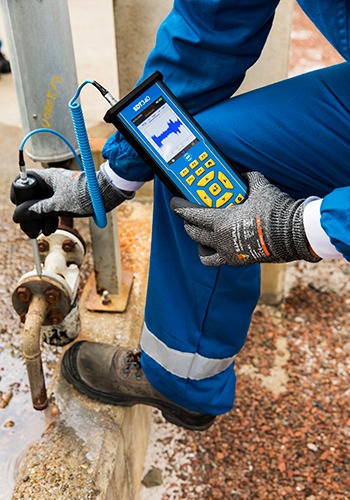
Steam Trap Goals every Maintenance Team should Strive for:
- Minimum Steam Loss;
- Maximum Transfer of Heat;
- Timely removal of condensable gasses;
- Zero Unplanned Downtime resulting from failures in the Steam System.
Inspection methods will vary from one steam system to another and from one trap to another. There are four common types of steam traps:
- Inverted Bucket;
- Float and Thermostatic;
- Thermostatic or Bimetallic;
- Thermodynamic or Disk.
They operate based on either changes in density, temperature or velocity.
While testing methods vary depending on the type of trap, the ultrasonic testing method works for most scenarios. What a technician is listening for on steam traps varies, making the importance of a technician knowing their system and steam traps crucial.
When a technician understands the way their steam system and steam traps sound through an ultrasound device, they can determine the health of their steam system simply by touching the contact sensor to the housing of the trap, and by taking upstream, and downstream temperature measurements.
Steam Trap Testing and Maintenance Highlights